To determine the specific heat capacity for melting, it is essential to understand the energy required to change the state of a material from solid to liquid. The specific heat capacity for melting, often referred to as the latent heat of fusion, is the amount of energy needed to melt a unit mass of a substance without changing its temperature. This concept is crucial in industries where melting materials is a common process, such as metallurgy, manufacturing, and energy production.
Key Points Explained:
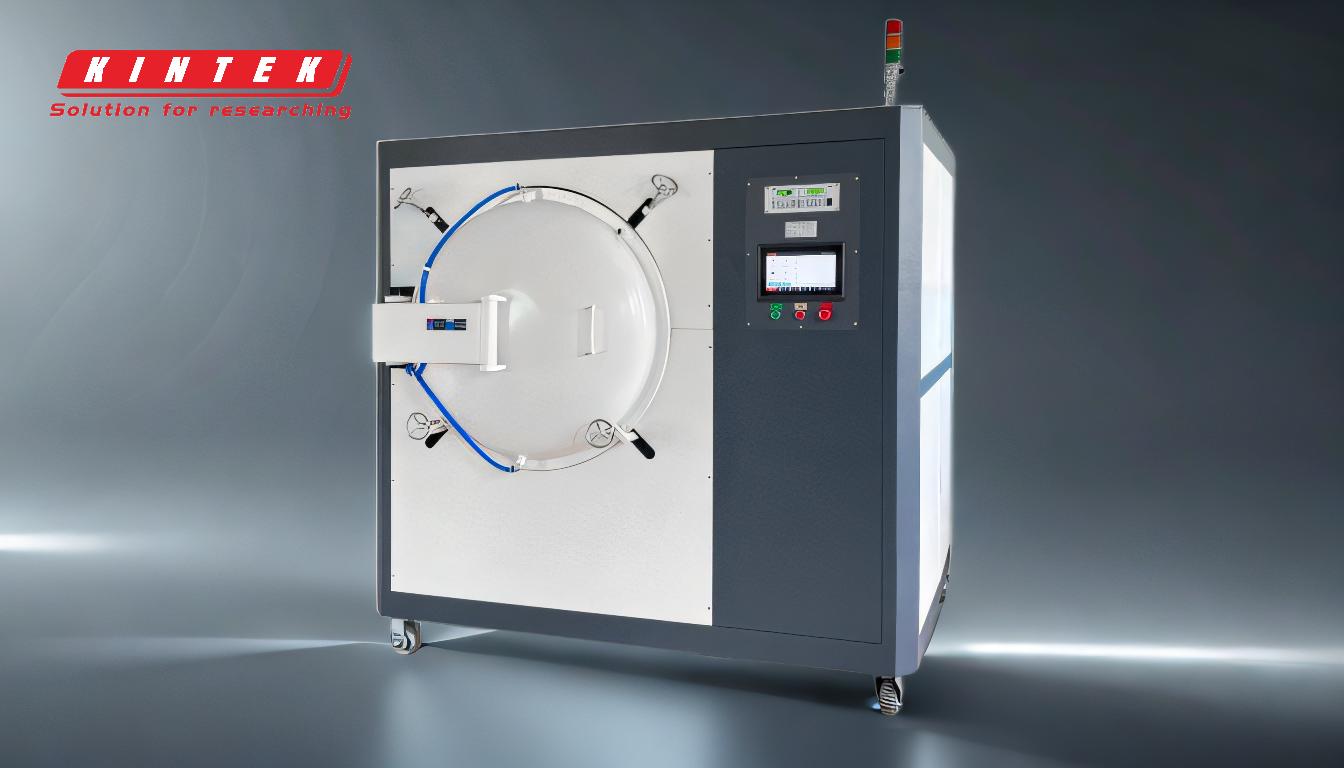
-
Understanding Specific Heat Capacity for Melting:
- The specific heat capacity for melting, or latent heat of fusion, is the energy required to change a substance from a solid to a liquid state at its melting point.
- This energy is used to overcome the intermolecular forces holding the solid together, allowing the molecules to move more freely as a liquid.
-
Formula for Calculating Energy Required for Melting:
- The formula provided,
Required kWh = Power consumption (kWh/ton) x Number of tons
, is a simplified way to calculate the energy needed to melt a specific amount of material. - This formula assumes that the power consumption per ton is known and can be used to scale up the energy requirement based on the mass of the material.
- The formula provided,
-
Factors Influencing Specific Heat Capacity for Melting:
- Material Properties: Different materials have different latent heats of fusion. For example, the latent heat of fusion for water is 334 kJ/kg, while for iron, it is approximately 272 kJ/kg.
- Temperature: The melting point of the material affects the energy required. Materials with higher melting points generally require more energy to melt.
- Purity and Composition: Impurities or alloying elements can alter the melting point and the energy required for melting.
-
Practical Applications:
- In industrial processes, knowing the specific heat capacity for melting helps in designing efficient melting furnaces and estimating energy costs.
- For example, in the steel industry, precise calculations of the energy required to melt iron and other metals are crucial for optimizing production processes and reducing energy consumption.
-
Energy Efficiency Considerations:
- Improving energy efficiency in melting processes can significantly reduce operational costs and environmental impact.
- Techniques such as preheating materials, using advanced insulation, and optimizing furnace design can help minimize energy consumption.
In summary, the specific heat capacity for melting, or latent heat of fusion, is a critical parameter in determining the energy required to melt materials. The formula Required kWh = Power consumption (kWh/ton) x Number of tons
provides a straightforward method to calculate this energy, but it is essential to consider material properties, temperature, and other factors that influence the melting process. Understanding these concepts is vital for optimizing industrial melting processes and achieving energy efficiency.
Summary Table:
Key Concept | Details |
---|---|
Specific Heat Capacity for Melting | Energy required to change a substance from solid to liquid at its melting point. |
Formula | Required kWh = Power consumption (kWh/ton) x Number of tons |
Factors Influencing Melting | Material properties, temperature, purity, and composition. |
Applications | Industrial melting processes like metallurgy, manufacturing, and energy production. |
Energy Efficiency | Techniques include preheating, advanced insulation, and optimized furnace design. |
Optimize your melting processes today—contact our experts for tailored solutions!