Magnetron sputtering is a versatile and widely used technique for depositing thin films in various industries, including microelectronics, optics, energy, and medical devices. It involves the use of a magnetic field to control the movement of charged particles, enabling efficient and precise deposition of materials onto substrates. The process begins with the introduction of an inert gas, typically argon, into a vacuum chamber. A high voltage is applied to create a plasma, which ionizes the gas. Positively charged argon ions are then attracted to a negatively charged target material, causing atoms to be ejected from the target. These atoms settle on the substrate, forming a thin film. Magnetron sputtering offers advantages such as compatibility with a wide range of materials, the ability to deposit uniform coatings, and the capacity to work with compounds and alloys without altering their composition. Applications range from semiconductor manufacturing and solar panel production to medical device coatings and wear-resistant machine parts.
Key Points Explained:
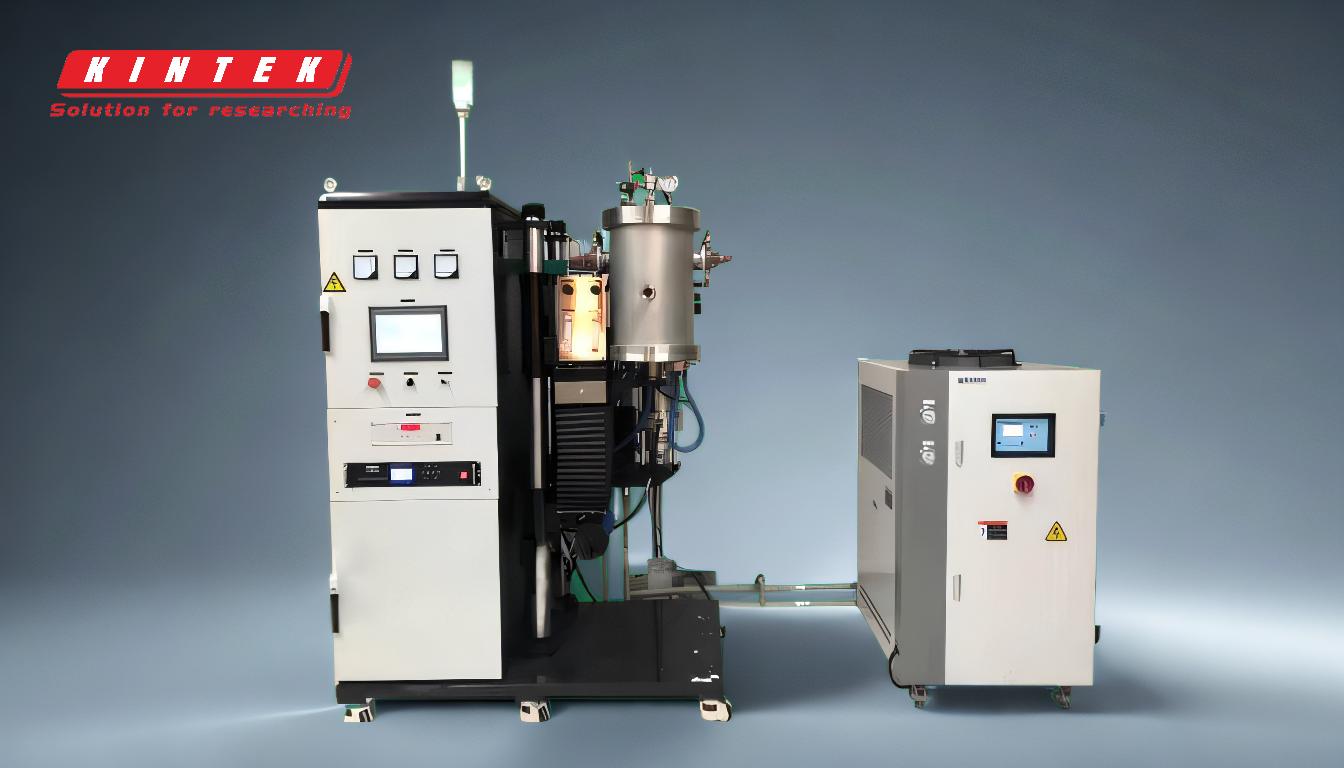
-
Basic Principle of Magnetron Sputtering:
- Magnetron sputtering uses a magnetic field to control the movement of charged particles in a plasma.
- An inert gas, such as argon, is introduced into a vacuum chamber and ionized to create a plasma.
- Positively charged ions are attracted to a negatively charged target material, causing atoms to be ejected and deposited onto a substrate.
-
Components and Process:
- Target Material: The material to be deposited, which is bombarded by ions.
- Substrate: The surface onto which the thin film is deposited.
- Magnetic Field: Generated by magnets behind the cathode, it traps electrons and enhances the efficiency of the sputtering process.
- Plasma Formation: High voltage ionizes the inert gas, creating a plasma that contains ions, electrons, and neutral atoms.
-
Advantages of Magnetron Sputtering:
- Material Compatibility: Works with almost all materials, including metals, alloys, and compounds.
- Uniform Coatings: Produces thin films with consistent thickness and composition.
- Low Temperature: Can deposit films at low temperatures, making it suitable for heat-sensitive substrates.
- High Deposition Rates: Achieves faster deposition compared to other techniques.
-
Applications in Various Industries:
- Microelectronics: Used for depositing thin films in semiconductor manufacturing, such as gate dielectrics and interlayer dielectrics.
- Optics: Creates anti-reflective coatings and solar control layers.
- Energy: Applied in solar panels and gas turbine blade coatings.
- Medical Devices: Used for anti-rejection coatings, radiation capsules, and dental implants.
- Machining: Provides wear-resistant and low-friction coatings for machine parts.
-
Research and Development:
- Magnetron sputtering is used in research to develop advanced materials, such as thin-film transistors (TFTs) made from amorphous indium gallium zinc oxide (a-IGZO) and zinc oxide.
- These materials are used in flexible electronics and high-performance displays.
-
Role of Magnetic Fields:
- Magnetic fields play a crucial role in controlling the trajectory of electrons, preventing them from bombarding the substrate and improving deposition efficiency.
- This allows for the use of a ptfe magnetic stirring bar in related applications, where precise control over material deposition is essential.
-
Future Prospects:
- Magnetron sputtering continues to evolve, with ongoing research focused on improving deposition rates, film quality, and the development of new materials for emerging technologies.
By understanding the principles and applications of magnetron sputtering, industries can leverage this technique to create high-performance coatings and thin films for a wide range of applications.
Summary Table:
Aspect | Details |
---|---|
Basic Principle | Uses a magnetic field to control charged particles in a plasma. |
Key Components | Target material, substrate, magnetic field, and plasma. |
Advantages | Material compatibility, uniform coatings, low temperature, high deposition. |
Applications | Microelectronics, optics, energy, medical devices, and machining. |
Future Prospects | Ongoing research for improved deposition rates and new materials. |
Discover how magnetron sputtering can enhance your projects—contact us today for expert guidance!