The strength of sintered parts is influenced by a variety of factors, including the material properties, sintering conditions, and the presence of porosity. While sintered parts may not always match the strength of forged or machined parts, they can achieve comparable mechanical properties when manufactured correctly. The strength of sintered parts is closely tied to their relative density, porosity, and grain size, which are controlled by factors such as temperature, pressure, and particle size during the sintering process. Sintered ceramics, for example, exhibit high durability and resistance to environmental factors due to the extreme heat and pressure applied during their creation. Understanding these factors is crucial for optimizing the strength of sintered parts for specific applications.
Key Points Explained:
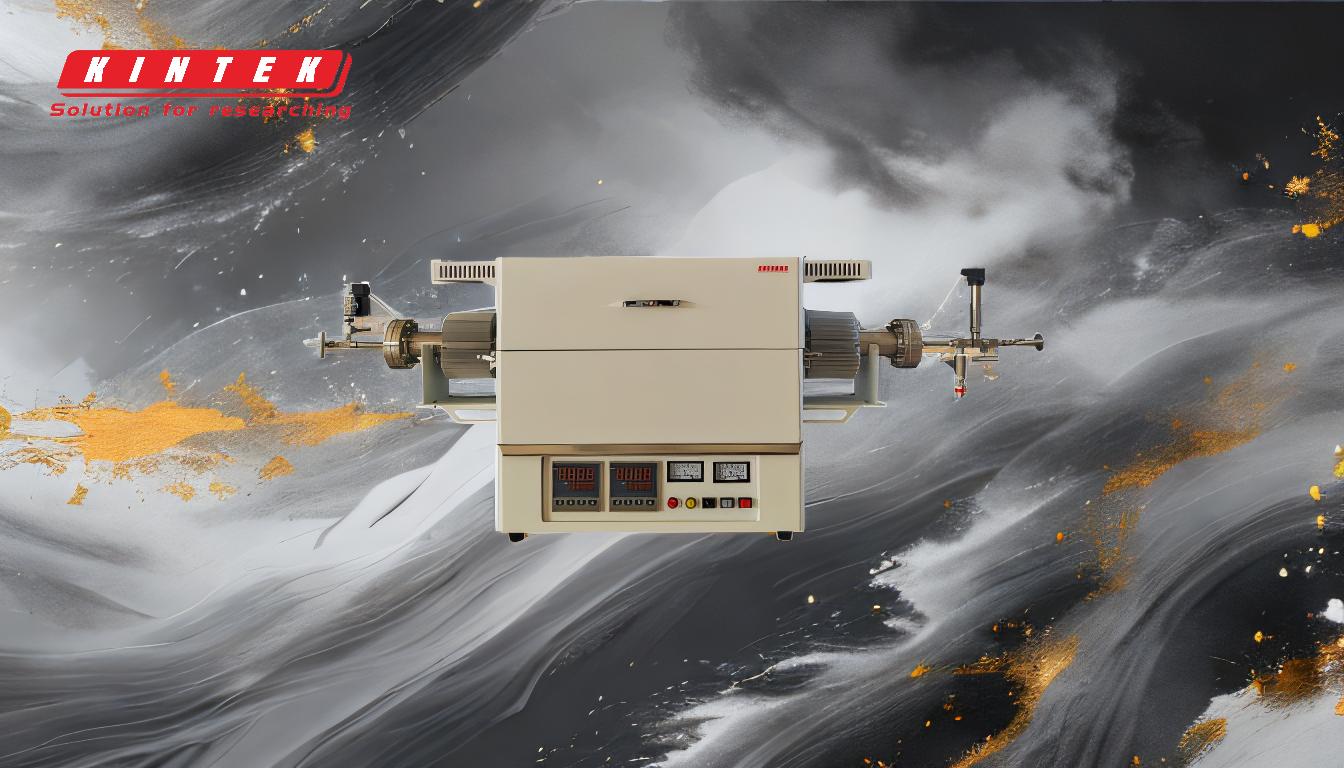
-
Factors Affecting Strength of Sintered Parts:
- Material Properties: The strength of sintered parts is influenced by the properties of the raw powder, including particle size and composition. Smaller particles and homogeneous compositions generally promote better densification and higher strength.
- Sintering Conditions: Temperature, heating rate, and pressure are critical in determining the final strength. Higher temperatures and applied pressure can reduce porosity and enhance particle bonding, leading to stronger parts.
- Porosity: The presence of pores can significantly reduce the strength of sintered parts. The final porosity is influenced by the initial green compact porosity and the sintering conditions.
-
Comparison with Forged or Machined Parts:
- Sintered parts are generally not as strong as forged or machined parts due to the presence of residual porosity and larger crystal grain sizes. However, with optimal manufacturing conditions, sintered parts can achieve comparable strength to machined equivalents.
- The fatigue strength of sintered parts may be slightly lower due to these factors.
-
Strength of Sintered Ceramics:
- Sintered ceramics are highly durable and resistant to environmental factors such as UV rays, extreme temperatures, and abrasion. This durability is a result of the natural materials used and the extreme heat and pressure applied during sintering.
- The strength of sintered ceramics is also influenced by the sintering time and temperature, with pure oxide ceramics requiring longer sintering times and higher temperatures for optimal strength.
-
Measurement of Strength-Related Properties:
- Relative Density: This is the ratio of the porous body density to the non-porous material density. Higher relative density generally correlates with higher strength.
- Radial Crushing Strength: This measures the breaking strength under radial pressure, providing a direct indication of the part's mechanical strength.
- Porosity and Pore Size Distribution: These properties affect the overall strength and durability of the sintered part. Lower porosity and a more uniform pore size distribution generally lead to higher strength.
-
Optimization of Sintered Parts Strength:
- Temperature Control: Proper temperature management during sintering is crucial for achieving the desired material properties and strength.
- Pressure Application: Applying pressure during sintering can enhance particle rearrangement and reduce porosity, leading to stronger parts.
- Particle Size and Composition: Using smaller particles and homogeneous compositions can improve densification and, consequently, the strength of the sintered parts.
By carefully controlling these factors, manufacturers can optimize the strength of sintered parts to meet specific application requirements, ensuring they perform reliably in their intended environments.
Summary Table:
Factor | Impact on Strength |
---|---|
Material Properties | Smaller particles and homogeneous compositions improve densification and strength. |
Sintering Conditions | Higher temperatures and pressure reduce porosity and enhance particle bonding. |
Porosity | Lower porosity and uniform pore size distribution lead to higher strength. |
Relative Density | Higher relative density correlates with increased mechanical strength. |
Particle Size | Smaller particles improve densification and strength. |
Need help optimizing the strength of your sintered parts? Contact our experts today for tailored solutions!