The suitable temperature for processing materials during the sintering stage depends on the material being sintered and the desired properties. For zirconia, the optimal sintering temperature typically ranges between 1200°C and 1550°C, with 1500°C being the most effective for achieving maximum strength and density. Temperatures below or above this range can lead to reduced strength due to grain growth or insufficient densification. Additionally, the ramp rate from 900°C to the top temperature, consistent temperature maintenance during the hold time, and controlled cooling back to 900°C are critical for ensuring high-quality results.
Key Points Explained:
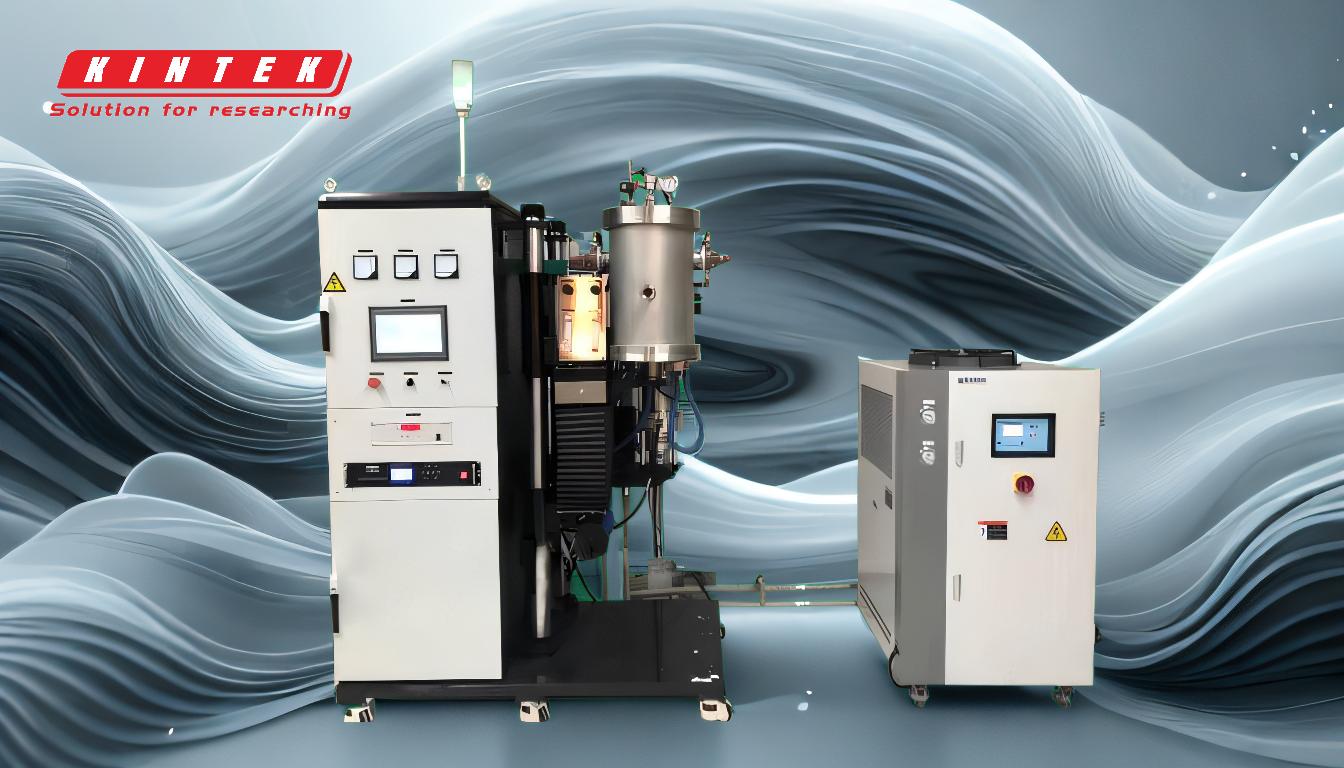
-
General Sintering Temperature Range:
- The sintering process for materials like zirconia typically requires high temperatures, often ranging from 1200°C to 1400°C. This range ensures proper densification and transformation of the material's microstructure.
-
Optimal Temperature for Zirconia:
- Recent studies suggest that 1500°C to 1550°C is the optimal temperature range for sintering zirconia. At this range, the material achieves maximum strength, with values around 1280 MPa.
- Deviating from this range by just 150°C can significantly reduce strength. For example:
- At 1600°C, strength drops to about 980 MPa.
- At 1700°C, strength further decreases to approximately 600 MPa.
-
Transformation Temperature:
- The transformation of zirconia from a monoclinic to a polytetragonal structure occurs at around 1100°C to 1200°C. This phase change is critical for achieving the desired material properties.
-
Effect of Higher Temperatures:
- Sintering at higher temperatures, such as 1500°C, results in denser zirconia, often reaching close to 99% of the theoretical maximum density. However, excessive temperatures can lead to grain growth, which reduces strength.
-
Ramp Rate and Cooling:
- The ramp rate from 900°C to the top temperature is critical. A controlled and consistent ramp ensures uniform heating and avoids thermal stress.
- Maintaining a consistent temperature during the hold time is essential for achieving uniform densification.
- The cooling rate back to about 900°C must also be controlled to prevent cracking or warping of the material.
-
Experimental and Practical Considerations:
- Some experiments have used sintering temperatures as high as 1800°C, but this is not typical for most industrial or dental applications.
- For practical purposes, 1500°C is often the preferred temperature due to its balance of strength, density, and material integrity.
-
Impact of Temperature Consistency:
- Consistency in temperature during sintering is vital. Variations can lead to uneven densification, reduced strength, or structural defects in the final product.
-
Material-Specific Considerations:
- While the focus here is on zirconia, other materials may have different optimal sintering temperatures. Always refer to material-specific guidelines for the best results.
By carefully controlling the sintering temperature within the optimal range and managing the ramp rate, hold time, and cooling process, manufacturers can achieve high-quality, dense, and strong sintered products.
Summary Table:
Key Factor | Details |
---|---|
Optimal Temperature Range | 1500°C–1550°C for maximum strength (~1280 MPa) and density (~99% theoretical). |
General Range | 1200°C–1400°C for proper densification and microstructure transformation. |
Transformation Temperature | 1100°C–1200°C for monoclinic to polytetragonal phase change. |
Ramp Rate | Controlled ramp from 900°C to top temperature to avoid thermal stress. |
Cooling Rate | Controlled cooling back to 900°C to prevent cracking or warping. |
Impact of Deviations | Deviations of ±150°C can reduce strength significantly (e.g., 600 MPa at 1700°C). |
Need help optimizing your sintering process? Contact our experts today for tailored solutions!