The sintering temperature for ceramic parts varies significantly depending on the type of ceramic material and its intended application. Generally, sintering occurs at 50% to 75% of the ceramic's melting temperature, typically exceeding 1000°C. For example, dental zirconia requires high temperatures between 1400°C and 1600°C to achieve optimal hardness and strength, with precise control needed to avoid grain growth and strength loss. Advanced technical ceramics may require even more controlled environments, while simpler ceramics like porcelain can be sintered at lower temperatures in basic kilns. The sintering process is critical for achieving the desired density, hardness, and structural integrity of the ceramic parts.
Key Points Explained:
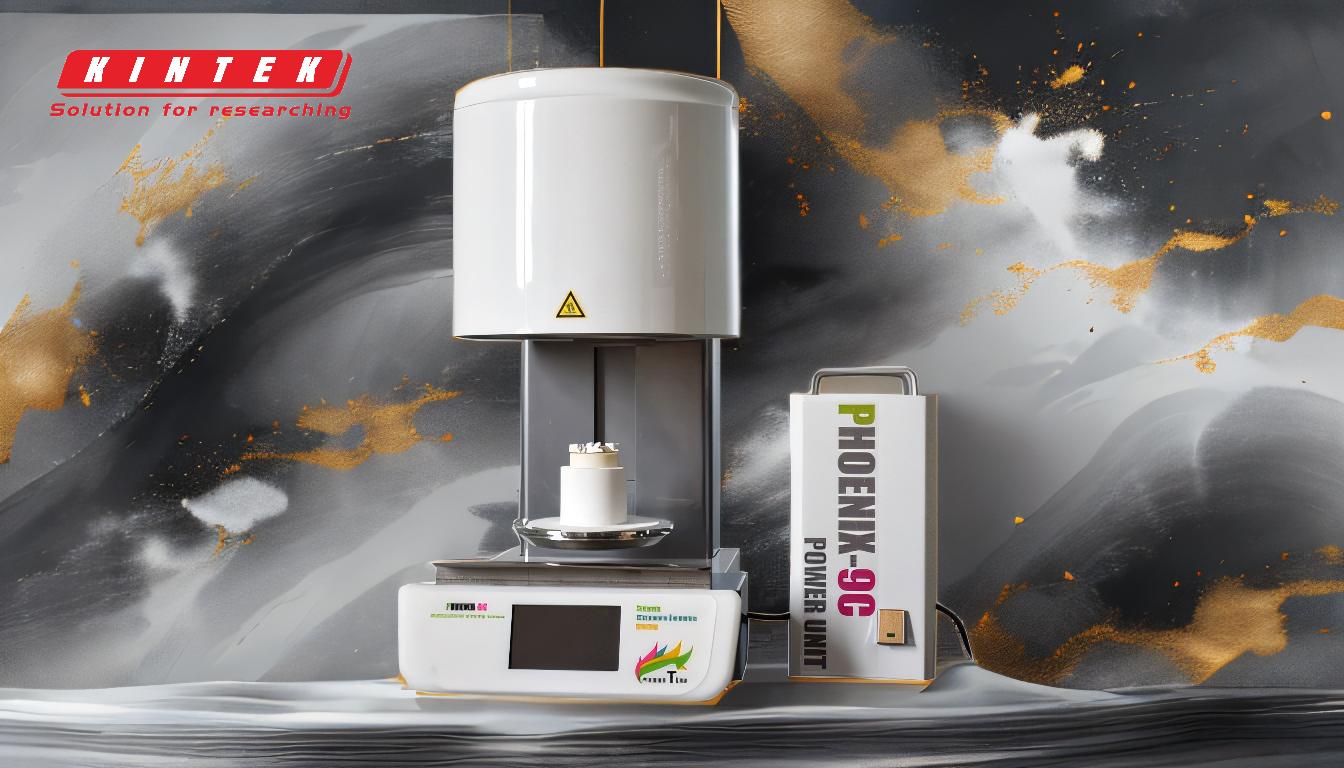
-
General Sintering Temperature Range:
- Ceramic materials are typically sintered at 50% to 75% of their melting temperature, which is usually greater than 1000°C. This range ensures that the material reaches more than 95% of its theoretical density, which is essential for achieving the desired mechanical properties.
-
Dental Zirconia Sintering:
- Dental zirconia requires sintering at high temperatures between 1400°C and 1600°C. This range is critical for achieving the necessary hardness and strength for dental applications.
- Recent studies indicate that firing zirconia at approximately 1500°C to 1550°C produces maximum strength. Deviations from this range, even by just 150°C, can result in significant strength loss due to grain growth.
-
Sintering of Ceramic Composites:
- Ceramic composites are typically sintered at temperatures between 900°C and 1250°C. This range is suitable for achieving the desired properties in composite materials, which may include a combination of different ceramic phases.
-
Importance of Temperature Control:
- The sintering process is highly sensitive to temperature control, especially during the ramp-up, hold, and cooling phases. For example, the ramp rate from 900°C to the top temperature, the consistency of the temperature during the hold time, and the rate of cooling back to about 900°C are all critical factors that influence the final properties of the ceramic.
-
Variability Based on Ceramic Type:
- Different types of ceramics require different sintering conditions. For instance, porcelain can be sintered in a simple, low-cost kiln, while advanced technical non-oxide ceramics need precisely controlled high-temperature sintering in a stabilizing atmosphere. This variability is due to differences in material composition and the desired end properties.
-
Impact of Temperature on Material Properties:
- The sintering temperature directly affects the material's density, hardness, and strength. For example, firing zirconia at 1500°C results in a strength of about 1280 MPa, while firing at 1600°C reduces the strength to about 980 MPa, and at 1700°C, it drops to about 600 MPa. This highlights the importance of precise temperature control to achieve optimal material performance.
-
Practical Considerations for Equipment:
- When selecting sintering equipment, it is crucial to consider the specific temperature requirements of the ceramic material being processed. High-temperature furnaces with precise temperature control are necessary for advanced ceramics, while simpler kilns may suffice for basic ceramics like porcelain.
In summary, the sintering temperature for ceramic parts is a critical parameter that varies depending on the material and application. Precise temperature control is essential to achieve the desired mechanical properties, and the choice of sintering equipment must align with the specific requirements of the ceramic being processed.
Summary Table:
Ceramic Type | Sintering Temperature Range | Key Considerations |
---|---|---|
General Ceramics | 50%-75% of melting temp (>1000°C) | Ensures >95% theoretical density, critical for mechanical properties. |
Dental Zirconia | 1400°C - 1600°C | Optimal hardness and strength; deviations cause grain growth and strength loss. |
Ceramic Composites | 900°C - 1250°C | Suitable for achieving desired properties in multi-phase materials. |
Porcelain | Lower temps in basic kilns | Simpler sintering process; no need for advanced equipment. |
Advanced Technical Ceramics | High temps with precise control | Requires stabilizing atmospheres and precise temperature management. |
Need help selecting the right sintering equipment for your ceramics? Contact our experts today!