The temperature of a batch type furnace, particularly in the context of a sintering furnace, varies significantly based on the material being processed and the desired outcome. Sintering furnaces are designed to operate at high temperatures, often reaching up to 1600°C or more, depending on the material's requirements. The process involves heating the material to a temperature below its melting point to allow particle fusion without liquefaction. Temperature control is critical, often managed through PID (Proportional-Integral-Derivative) systems to ensure precise and automated heating and cooling cycles. The specific temperature settings are influenced by factors such as the material's properties, the required density of the final product, and the furnace's atmospheric conditions.
Key Points Explained:
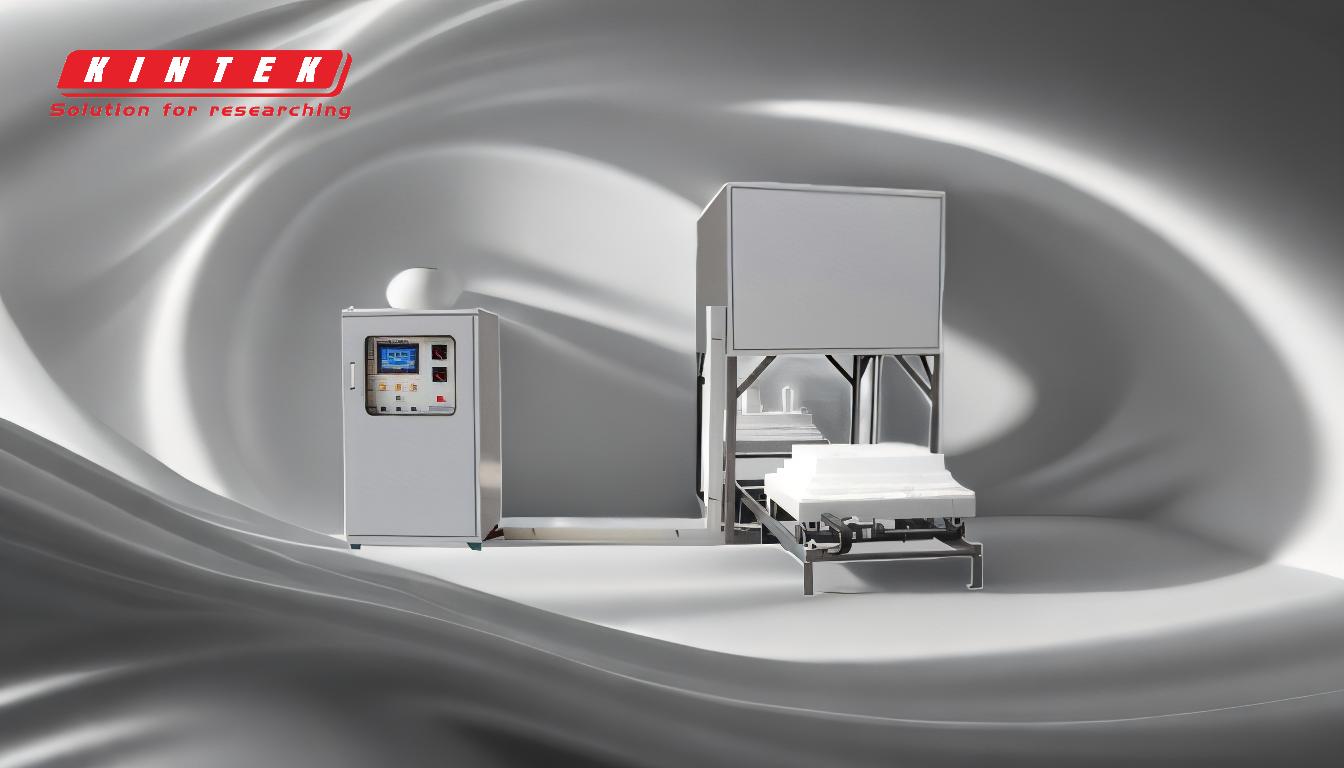
-
Temperature Range in Sintering Furnaces:
- Sintering furnaces typically operate at high temperatures, often ranging from 1200°C to 1600°C or higher, depending on the material being processed.
- The temperature must be high enough to allow atomic diffusion across particle boundaries, facilitating particle fusion, but it must remain below the material's melting point to prevent liquefaction.
-
Material Dependency:
- The specific temperature required for sintering varies based on the material being used. For example, ceramics, metals, and alloys each have different sintering temperature requirements.
- The desired density and properties of the final product also influence the temperature settings.
-
Atmospheric Control:
- Sintering furnaces operate in carefully controlled atmospheric environments, which can include vacuum, inert gas, or reducing atmospheres, depending on the material and process requirements.
- The atmospheric conditions help prevent oxidation and other unwanted chemical reactions during the sintering process.
-
Temperature Control Systems:
- Modern sintering furnaces often use PID control systems to manage temperature precisely. These systems allow for automated heating and cooling cycles, ensuring consistent and repeatable results.
- The temperature control points, such as the ignition temperature, end temperature, and exhaust gas temperature, are critical for achieving high-quality sintered products.
-
Process Automation:
- Once the sintering program is set, the furnace can carry out the heating and cooling processes automatically, reducing the need for manual intervention and improving process efficiency.
- This automation is particularly beneficial in industrial applications where consistency and precision are paramount.
-
Influence of External Factors:
- Temperature control in sintering furnaces can be affected by external factors such as soiling, deposits, and chemical reactions from the materials being processed.
- Regular maintenance and calibration of the furnace are necessary to ensure accurate temperature control and optimal performance.
By understanding these key points, purchasers of sintering furnaces can make informed decisions about the equipment that best meets their specific material processing needs and desired outcomes. For more detailed information on sintering furnaces, you can visit sintering furnace.
Summary Table:
Aspect | Details |
---|---|
Temperature Range | 1200°C to 1600°C or higher, depending on material and desired outcome. |
Material Dependency | Varies for ceramics, metals, and alloys; influenced by final product density. |
Atmospheric Control | Vacuum, inert gas, or reducing atmospheres to prevent oxidation. |
Control Systems | PID systems ensure precise, automated heating and cooling cycles. |
Process Automation | Automated programs reduce manual intervention, enhancing efficiency. |
External Factors | Soiling, deposits, and chemical reactions can affect temperature control. |
Need a sintering furnace tailored to your material processing needs? Contact our experts today for personalized solutions!