The temperature of a heat treatment furnace is not fixed but varies depending on the specific requirements of the heat treatment process, the material being treated, and the desired metallurgical results. Heat treatment furnaces are designed to regulate and maintain precise temperatures to achieve consistent and repeatable outcomes. The temperature is controlled using algorithms, thermocouples, or temperature-sensing devices, and factors such as furnace atmosphere, air flow, and material properties influence the process. Continuous furnaces, for example, operate at permanent temperatures for specific processes like annealing or hardening. The temperature is adjusted during the heating phase and then maintained at a constant level to ensure uniformity and precision.
Key Points Explained:
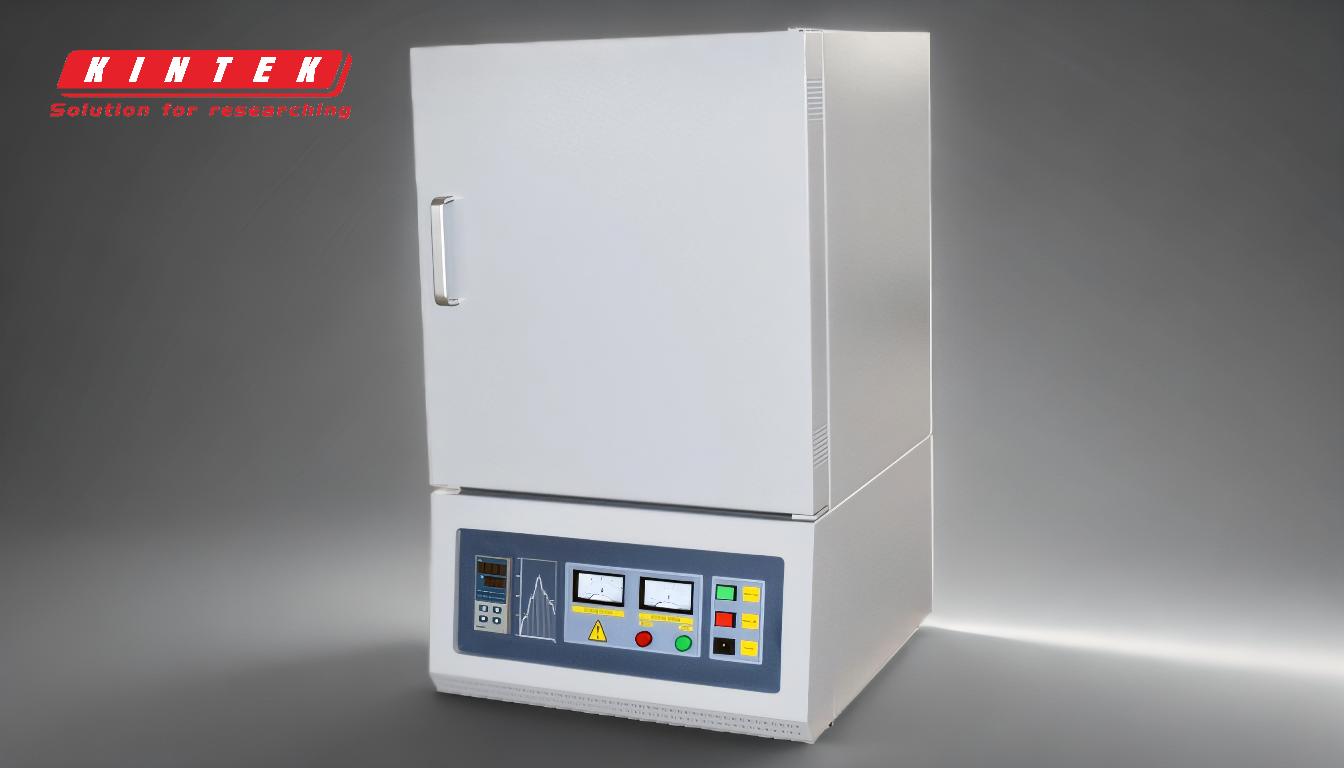
-
Temperature Regulation in Heat Treatment Furnaces:
- The temperature in a heat treatment furnace is dynamically regulated based on the stage of the process. During the initial heating phase, more heat is applied to raise the furnace to the desired temperature. Once the target temperature is achieved, the heat is maintained at a constant level to ensure stability and uniformity throughout the furnace.
- This regulation is crucial for achieving consistent results in processes like annealing, hardening, and carburizing.
-
Role of Furnace Type and Process:
- Continuous furnaces, for instance, are designed to operate at permanent temperatures for specific heat treatment cycles. These furnaces are specialized for processes such as annealing, hardening, normalizing, or carburizing, where the same components made of the same grade of steel are treated repeatedly.
- The furnace type and process dictate the temperature requirements, ensuring that the material properties are modified as intended.
-
Factors Influencing Temperature Control:
- Furnace Atmosphere: The choice of atmosphere (inert or active) depends on the material being treated, design requirements, and cost considerations. The atmosphere affects how heat is distributed and absorbed, influencing the overall temperature control.
- Air Flow: Proper air flow ensures even heat distribution, which is critical for maintaining consistent temperatures throughout the furnace.
- Material Properties: The type of material and its flow properties (e.g., in a Rotary Tube Furnace) also influence the heat treatment time and temperature requirements.
-
Temperature Control Mechanisms:
- Temperature control in heat treatment furnaces is achieved using sophisticated algorithms, controllers, and temperature-sensing devices like thermocouples. These tools ensure that the desired temperature is maintained within precise limits, as defined by the part or customer requirements.
- The ability to transform the material to deliver the desired metallurgical results is directly tied to accurate temperature control.
-
Importance of Temperature Uniformity:
- Even heat distribution is critical for consistent results. Uneven temperatures can lead to variations in material properties, affecting the quality and performance of the treated components.
- Furnace design and operational parameters (e.g., inclination angle, rotational speed in Rotary Tube Furnaces) are optimized to achieve uniform temperature distribution.
-
Selection of Heat Treatment Furnaces:
- The choice of furnace depends on factors such as the material being treated, temperature requirements, and production volume. Selecting the right furnace ensures that the desired temperature and heat treatment results are achieved efficiently.
- For example, specialized furnaces are chosen for specific processes like carbonitriding or sintering, where precise temperature control is essential.
-
Heat Treatment Processes and Temperature Ranges:
- Different heat treatment processes require specific temperature ranges. For instance:
- Annealing: Typically involves heating to temperatures between 700°C and 900°C, followed by slow cooling.
- Hardening: Requires heating to temperatures above the material’s critical point (e.g., 800°C to 950°C for steel), followed by rapid cooling.
- Carburizing: Often performed at temperatures around 900°C to 950°C to introduce carbon into the material surface.
- The exact temperature depends on the material composition and the desired outcome.
- Different heat treatment processes require specific temperature ranges. For instance:
-
Practical Considerations for Equipment Purchasers:
- When selecting a heat treatment furnace, purchasers should consider:
- The specific heat treatment processes required.
- The temperature range and control precision needed.
- The furnace’s ability to maintain uniform temperatures and distribute heat evenly.
- The compatibility of the furnace with the materials and production volume.
- These factors ensure that the furnace meets operational requirements and delivers consistent, high-quality results.
- When selecting a heat treatment furnace, purchasers should consider:
By understanding these key points, equipment purchasers can make informed decisions about heat treatment furnaces, ensuring they select the right equipment for their specific needs and achieve the desired material properties through precise temperature control.
Summary Table:
Key Aspect | Details |
---|---|
Temperature Regulation | Dynamically adjusted during heating phase, then maintained for uniformity. |
Furnace Type & Process | Continuous furnaces operate at permanent temps for annealing, hardening, etc. |
Factors Influencing Control | Furnace atmosphere, air flow, and material properties. |
Control Mechanisms | Algorithms, controllers, and thermocouples ensure precise temperature. |
Temperature Uniformity | Critical for consistent results; uneven temps affect material properties. |
Heat Treatment Processes | Annealing (700°C–900°C), Hardening (800°C–950°C), Carburizing (900°C–950°C). |
Furnace Selection | Depends on material, temperature range, and production volume. |
Need a heat treatment furnace tailored to your needs? Contact our experts today for personalized solutions!