The temperature of an industrial furnace can vary significantly depending on its type, application, and design. Industrial furnaces are designed to operate at specific temperature ranges to meet the requirements of various processes such as heat treatment, melting, sintering, and more. For example, a muffle furnace might operate between 300°C to 1800°C, while an IGBT furnace, which is often used for induction heating, can reach temperatures up to 2500°C or higher depending on the material being processed. The exact temperature range is determined by factors such as the furnace's heating elements, insulation, and control systems. Understanding these factors is crucial for selecting the right furnace for a specific industrial application.
Key Points Explained:
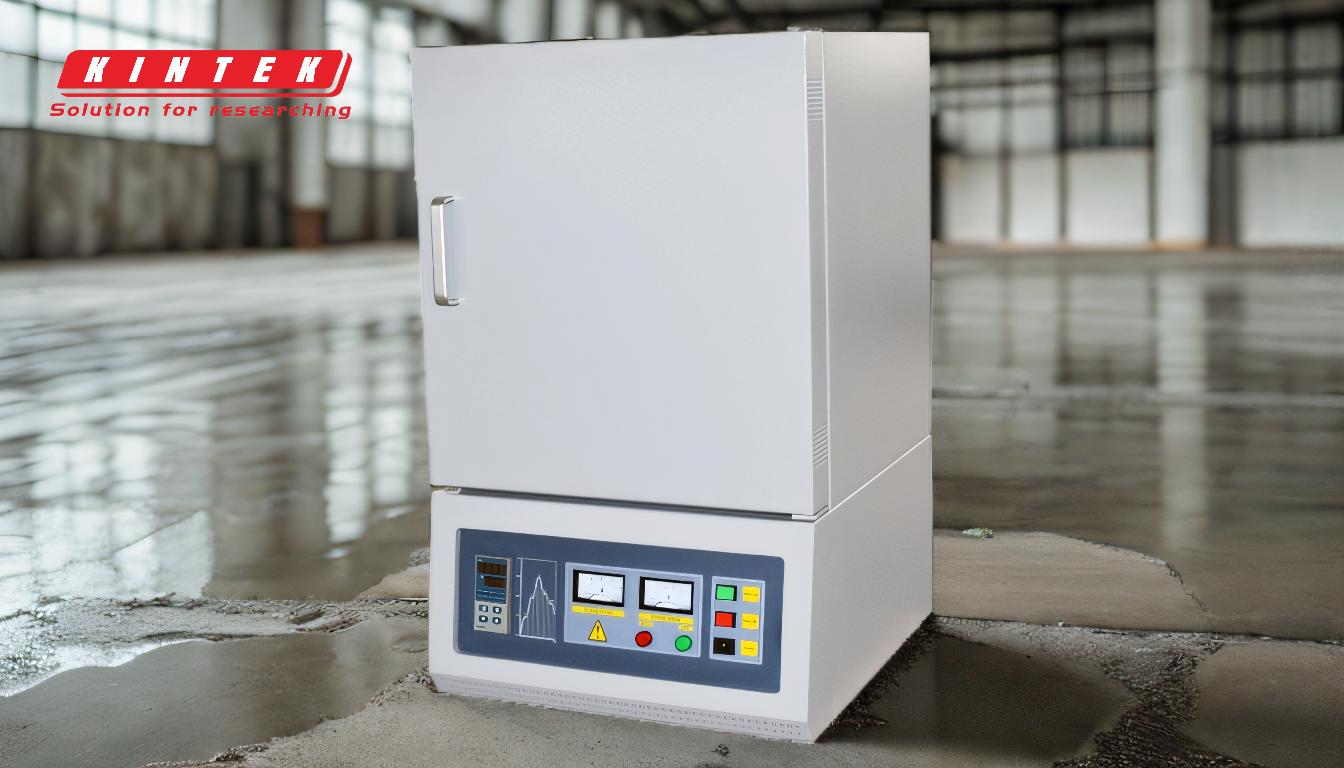
-
Types of Industrial Furnaces and Their Temperature Ranges:
- Muffle Furnace: Typically operates between 300°C to 1800°C. It is commonly used for applications requiring uniform heating, such as laboratory testing and small-scale industrial processes.
- IGBT Furnace: Utilizes induction heating and can reach temperatures up to 2500°C or higher. It is ideal for high-temperature processes like melting metals or sintering ceramics.
- Blast Furnace: Used in metal smelting, operating at temperatures around 1200°C to 1600°C.
- Kiln Furnace: Commonly used in ceramics and cement production, with temperatures ranging from 1000°C to 1400°C.
-
Factors Influencing Furnace Temperature:
- Heating Elements: The type of heating element (e.g., resistance wires, induction coils) determines the maximum achievable temperature.
- Insulation: High-quality insulation materials are essential to maintain high temperatures and improve energy efficiency.
- Control Systems: Advanced temperature control systems ensure precise regulation of the furnace temperature, which is critical for process consistency.
-
Applications and Temperature Requirements:
- Heat Treatment: Processes like annealing, tempering, and hardening typically require temperatures between 500°C to 1200°C.
- Melting: Metal melting processes often require temperatures above 1500°C, making IGBT furnaces suitable for such applications.
- Sintering: Used in powder metallurgy, sintering processes usually operate between 1000°C to 1400°C.
-
Importance of Temperature Control:
- Process Quality: Precise temperature control ensures consistent results and high-quality output.
- Energy Efficiency: Proper temperature management reduces energy consumption and operational costs.
- Safety: Maintaining the correct temperature prevents overheating, which can damage the furnace and pose safety risks.
-
Selecting the Right Furnace:
- Identify Process Requirements: Determine the temperature range and heating uniformity needed for your specific application.
- Evaluate Furnace Features: Consider factors like heating elements, insulation, and control systems when choosing a furnace.
- Consult Experts: Seek advice from furnace manufacturers or industry experts to ensure you select the most suitable equipment.
In summary, the temperature of an industrial furnace depends on its type and intended application. Understanding the specific temperature requirements of your process and the capabilities of different furnace types, such as the igbt furnace, is essential for achieving optimal results in industrial operations.
Summary Table:
Furnace Type | Temperature Range | Common Applications |
---|---|---|
Muffle Furnace | 300°C to 1800°C | Laboratory testing, small-scale processes |
IGBT Furnace | Up to 2500°C+ | Melting metals, sintering ceramics |
Blast Furnace | 1200°C to 1600°C | Metal smelting |
Kiln Furnace | 1000°C to 1400°C | Ceramics, cement production |
Need help selecting the right furnace for your application? Contact our experts today!