CVD (Chemical Vapor Deposition) and PVD (Physical Vapor Deposition) are two widely used coating technologies, each operating at distinct temperature ranges due to their differing mechanisms. CVD typically requires much higher temperatures, ranging from 600°C to 1100°C, as it involves chemical reactions between gases and the substrate. In contrast, PVD operates at significantly lower temperatures, usually between 70°C and 600°C, as it relies on physical processes like vaporization and condensation. The choice between CVD and PVD often depends on the substrate material and its thermal tolerance, with PVD being more suitable for heat-sensitive materials like plastics.
Key Points Explained:
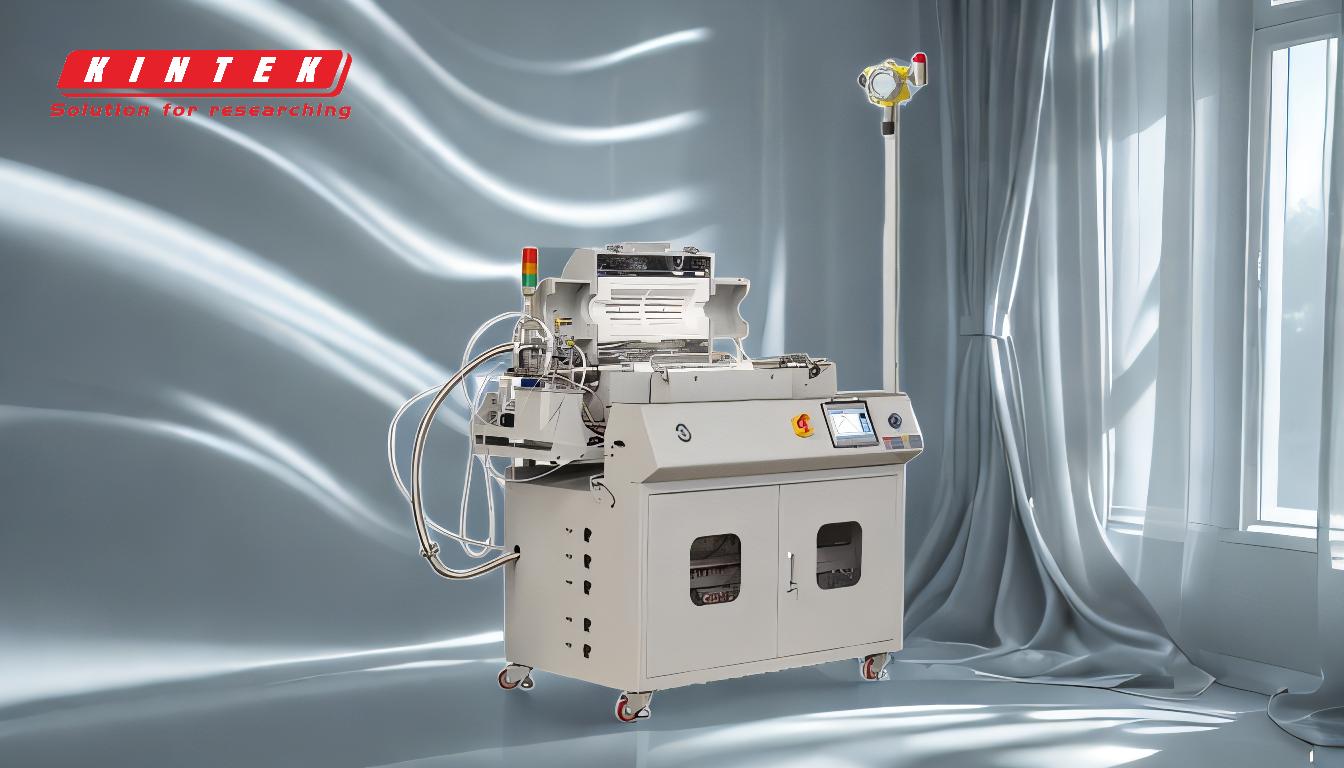
-
Temperature Ranges for CVD and PVD:
- CVD: Operates at high temperatures, typically between 600°C and 1100°C. This is because CVD involves chemical reactions between gaseous precursors and the substrate, which require substantial thermal energy to proceed.
- PVD: Operates at lower temperatures, generally between 70°C and 600°C. PVD relies on physical processes such as sputtering or evaporation, which do not require the same level of thermal energy as CVD.
-
Mechanisms Behind Temperature Differences:
- CVD Mechanism: In CVD, gases are heated to high temperatures to facilitate chemical reactions that deposit a solid material onto the substrate. The high temperatures are necessary to break chemical bonds in the gas and form new bonds on the substrate surface.
- PVD Mechanism: PVD involves the physical vaporization of a solid material, which then condenses onto the substrate. Since this process is primarily physical rather than chemical, it can occur at much lower temperatures.
-
Impact on Substrate Materials:
- CVD Limitations: The high temperatures required for CVD make it unsuitable for substrates that cannot withstand thermal stress, such as certain plastics or low-melting-point metals.
- PVD Advantages: PVD's lower operating temperatures make it ideal for coating heat-sensitive materials, including plastics and some alloys, without risking thermal damage.
-
Applications Based on Temperature:
- CVD Applications: Commonly used in applications requiring high-temperature stability, such as semiconductor manufacturing, where substrates like silicon wafers can tolerate the high temperatures.
- PVD Applications: Widely used in industries where substrates are heat-sensitive, such as in the coating of cutting tools, decorative finishes, and optical components.
-
Energy Sources for Heating:
- CVD Heating Methods: CVD processes often use furnaces, RF coils, or lasers to achieve the necessary high temperatures.
- PVD Heating Methods: PVD typically uses simpler heating mechanisms, such as resistive heating or plasma generation, which do not require the same energy input as CVD.
-
Comparative Summary:
- CVD: Higher temperatures (600°C – 1100°C), suitable for high-temperature-tolerant substrates, involves chemical reactions.
- PVD: Lower temperatures (70°C – 600°C), suitable for heat-sensitive substrates, involves physical processes.
Understanding these temperature differences is crucial for selecting the appropriate coating technology based on the substrate material and the desired application.
Summary Table:
Aspect | CVD | PVD |
---|---|---|
Temperature Range | 600°C – 1100°C | 70°C – 600°C |
Mechanism | Chemical reactions | Physical processes |
Substrate Suitability | High-temperature-tolerant materials | Heat-sensitive materials (e.g., plastics) |
Applications | Semiconductor manufacturing | Cutting tools, decorative finishes |
Energy Sources | Furnaces, RF coils, lasers | Resistive heating, plasma generation |
Need help selecting the right coating technology? Contact our experts today for personalized guidance!