Hot Isostatic Pressing (HIP) is a material processing method that involves applying high temperatures and isostatic pressure simultaneously to compress, sinter, or densify materials. The temperature range for HIP varies depending on the material being processed, but it typically falls between 1000°C to 2200°C (1832°F to 3992°F). For ceramics and carbon-based materials, temperatures can reach up to 1500°C (2700°F). The process uses inert gases like argon as the pressure medium, with pressures ranging from 100 to 300 MPa (15,000 to 45,000 psi). The temperature and pressure are carefully controlled to achieve the desired material properties, such as improved density, strength, and microstructure.
Key Points Explained:
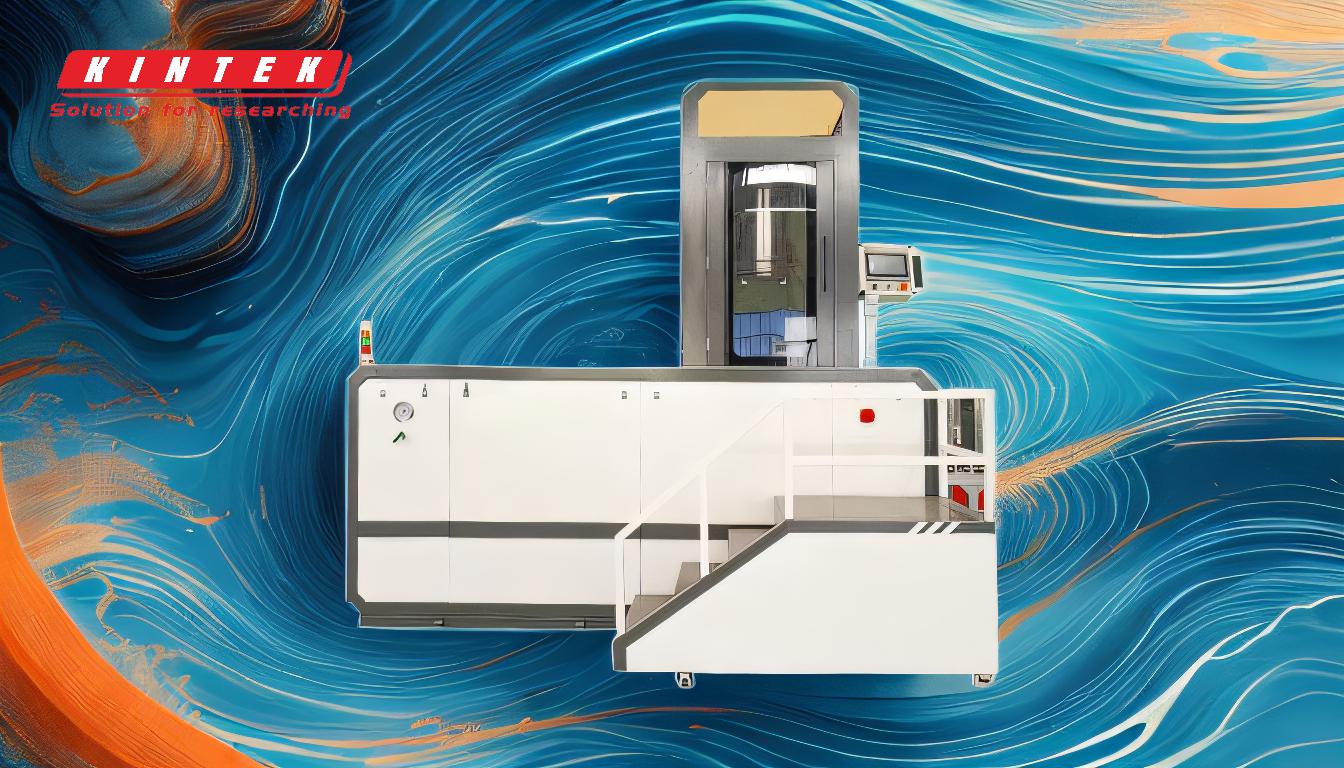
-
Temperature Range for HIP:
- The temperature for Hot Isostatic Pressing typically ranges from 1000°C to 2200°C (1832°F to 3992°F).
- For ceramics and carbon-based materials, temperatures can go up to 1500°C (2700°F).
- The exact temperature depends on the material being processed and the desired outcome, such as sintering or densification.
-
Material-Specific Temperature Requirements:
- Different materials require different temperatures for optimal results. For example:
- Metals and alloys typically use temperatures in the range of 1000°C to 1200°C (1832°F to 2192°F).
- Ceramics and carbon-based materials may require higher temperatures, up to 1500°C (2700°F).
- Different materials require different temperatures for optimal results. For example:
-
Pressure Medium and Conditions:
- The process uses inert gases like argon as the pressure medium.
- Pressures typically range from 100 to 300 MPa (15,000 to 45,000 psi).
- The combination of high temperature and pressure ensures uniform densification and improved material properties.
-
Equipment Capabilities:
- HIP systems are designed to handle extreme temperatures and pressures.
- Industrial equipment can heat parts to 1000°C to 1200°C (1832°F to 2192°F) for most materials.
- Specialized units for ceramics and carbon-based materials can reach temperatures up to 1500°C (2700°F).
-
Process Applications:
- HIP is used for sintering powders, densifying castings, and eliminating porosity in materials.
- It is widely applied in industries such as aerospace, automotive, and medical devices to produce high-performance components.
-
Comparison with Other Processes:
- HIP is similar to hot pressing but differs in the application of isostatic pressure, which ensures uniform compression from all directions.
- Unlike temperature isostatic pressing, which operates at much lower temperatures (80°C to 450°C), HIP involves significantly higher temperatures and pressures.
By understanding these key points, a purchaser can evaluate the suitability of HIP for specific materials and applications, ensuring optimal results in terms of material properties and performance.
Summary Table:
Key Aspect | Details |
---|---|
Temperature Range | 1000°C to 2200°C (1832°F to 3992°F) |
Ceramics/Carbon Materials | Up to 1500°C (2700°F) |
Pressure Range | 100 to 300 MPa (15,000 to 45,000 psi) |
Pressure Medium | Inert gases like argon |
Applications | Sintering, densifying castings, eliminating porosity in aerospace, automotive, and medical industries |
Equipment Capabilities | Handles extreme temperatures and pressures; specialized units for ceramics |
Discover how Hot Isostatic Pressing can transform your materials—contact us today for expert guidance!