The temperature of the annealing process depends on the type of metal being treated, as different metals have unique crystalline structures and properties. Generally, annealing involves heating the metal to a specific temperature where its crystalline structure becomes fluid but remains in a solid state. This temperature is typically below the melting point of the metal but high enough to allow defects to repair themselves. The metal is held at this temperature for a set duration (e.g., 1 hour) and then cooled slowly to room temperature to achieve a more ductile and workable material. The exact temperature varies based on the metal's composition and desired properties.
Key Points Explained:
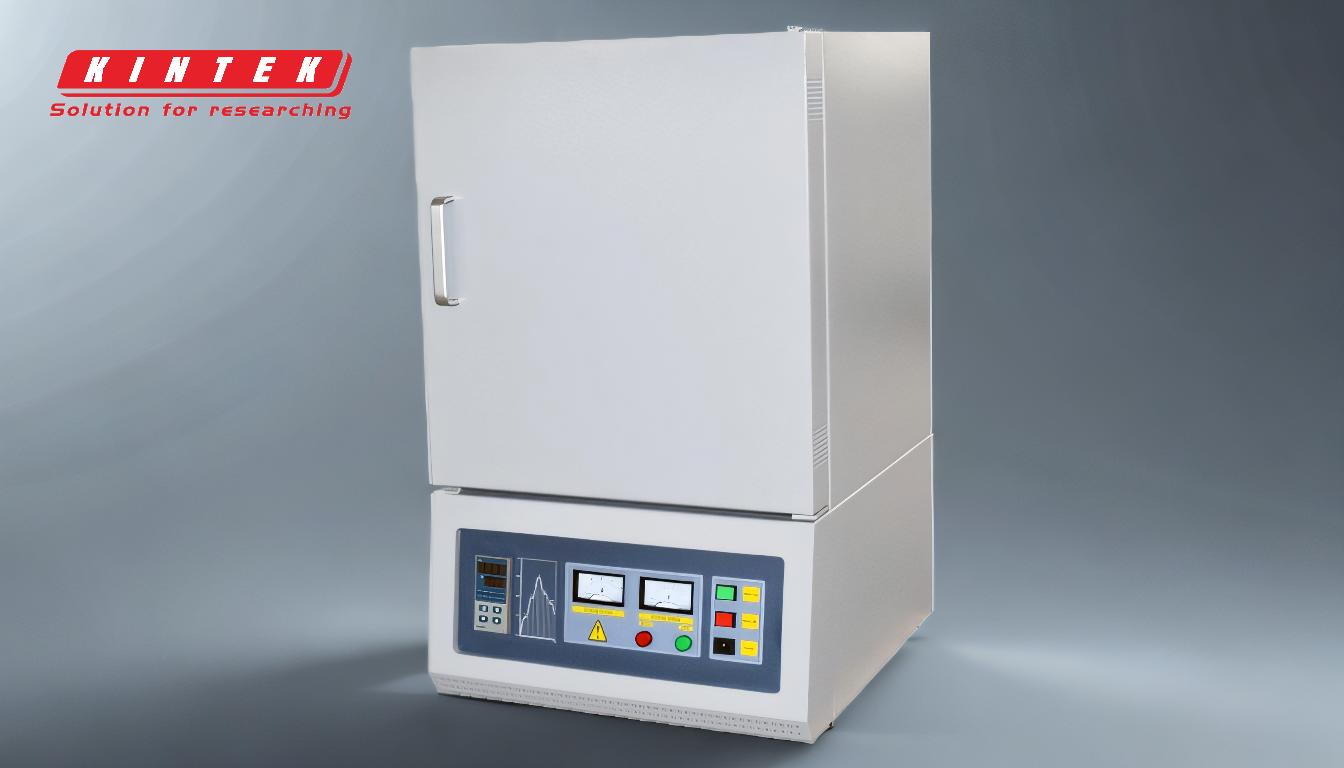
-
Definition of Annealing:
- Annealing is a heat treatment process used to alter the physical and sometimes chemical properties of a metal to increase its ductility, reduce hardness, and improve machinability.
- The process involves heating the metal to a specific temperature, holding it there, and then cooling it slowly.
-
Temperature Range for Annealing:
- The annealing temperature is typically below the metal's melting point but high enough to allow the crystalline structure to become fluid.
- For example:
- Steel: Annealing temperatures for steel usually range between 700°C and 900°C, depending on the type of steel (e.g., low-carbon steel, high-carbon steel, or alloy steel).
- Copper: Copper is annealed at around 400°C to 700°C.
- Aluminum: Aluminum alloys are annealed at temperatures between 300°C and 400°C.
- The exact temperature depends on the metal's composition and the desired outcome.
-
Importance of Temperature Control:
- Heating the metal to the correct temperature is crucial for achieving the desired crystalline structure.
- If the temperature is too low, the defects in the material may not fully repair, leading to incomplete annealing.
- If the temperature is too high, the metal may partially melt or develop undesirable properties.
-
Holding Time:
- The metal is held at the annealing temperature for a specific duration to ensure uniformity in the crystalline structure.
- For example, the reference mentions a holding time of 1 hour, which is common for many metals.
- The holding time allows defects to repair and the crystalline structure to stabilize.
-
Cooling Process:
- After holding at the annealing temperature, the metal is cooled slowly to room temperature.
- Slow cooling is essential to prevent the formation of internal stresses and to achieve a more ductile and workable material.
- Rapid cooling (quenching) is avoided during annealing, as it can lead to increased hardness and brittleness.
-
Material-Specific Considerations:
- Different metals require different annealing temperatures and cooling rates.
- For example, stainless steel may require a higher annealing temperature compared to carbon steel due to its alloying elements.
- The annealing process must be tailored to the specific metal and its intended application.
-
Practical Implications for Purchasers:
- When purchasing equipment or consumables for annealing, it is essential to consider the specific temperature requirements of the metals being treated.
- Ensure that the equipment (e.g., furnaces) can accurately maintain the required temperature and cooling rates.
- For consumables, such as protective atmospheres or flux, verify their compatibility with the annealing temperature and the metal being processed.
By understanding these key points, equipment and consumable purchasers can make informed decisions to ensure the annealing process is carried out effectively and efficiently.
Summary Table:
Metal Type | Annealing Temperature Range |
---|---|
Steel | 700°C - 900°C |
Copper | 400°C - 700°C |
Aluminum | 300°C - 400°C |
Key Considerations:
- Temperature must be below the metal's melting point.
- Holding time (e.g., 1 hour) ensures defect repair.
- Slow cooling prevents internal stresses and brittleness.
Need help selecting the right annealing equipment? Contact our experts today for tailored solutions!