The reflow process is a critical step in surface mount technology (SMT) assembly, where the solder paste is melted to form a strong bond between component leads and PCB pads. The temperature during the reflow process typically ranges between 240°C and 250°C for lead-free (Pb-free) solder alloys, such as Sn/Ag (tin/silver). This temperature range ensures proper melting of the solder paste, enabling it to flow and create reliable electrical and mechanical connections. The exact temperature may vary depending on the specific solder alloy, component specifications, and PCB design, but maintaining this range is crucial for achieving high-quality solder joints without damaging components or the PCB.
Key Points Explained:
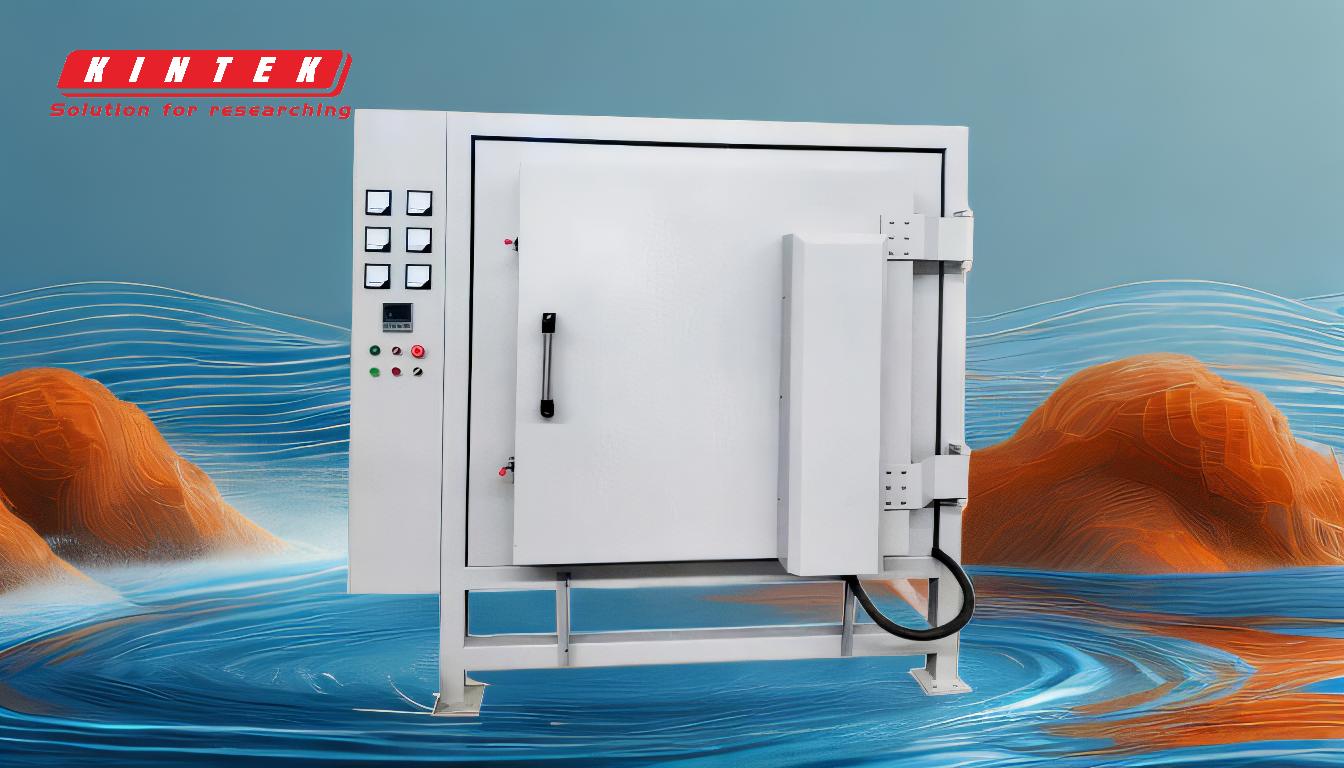
-
Purpose of the Reflow Process:
- The reflow process is designed to melt the solder paste, allowing it to flow and form a strong metallurgical bond between the component leads and the PCB pads.
- This step is essential for creating reliable electrical connections and ensuring the mechanical stability of the assembled components.
-
Typical Reflow Temperature Range:
- For lead-free (Pb-free) solder alloys, such as Sn/Ag (tin/silver), the reflow temperature typically ranges between 240°C and 250°C.
- This temperature range is chosen because it is high enough to melt the solder paste but low enough to avoid damaging sensitive components or the PCB substrate.
-
Factors Influencing Reflow Temperature:
- Solder Alloy Composition: Different solder alloys have varying melting points. For example, Sn/Ag/Cu (SAC) alloys, commonly used in lead-free soldering, have a melting point around 217°C, but the reflow temperature is set higher to ensure proper wetting and bonding.
- Component Specifications: Heat-sensitive components may require a lower peak temperature or a shorter dwell time above the melting point to prevent damage.
- PCB Design: Thicker or multi-layer PCBs may require adjustments to the reflow profile to ensure even heating across the board.
-
Reflow Profile:
- The reflow process is not just about reaching a specific temperature; it involves a carefully controlled temperature profile with distinct phases:
- Preheat Phase: Gradually raises the temperature to activate the flux and remove solvents from the solder paste.
- Soak Phase: Maintains a steady temperature to ensure uniform heating of the PCB and components.
- Reflow Phase: Rapidly increases the temperature to the peak range (240–250°C) to melt the solder paste.
- Cooling Phase: Slowly lowers the temperature to solidify the solder joints and prevent thermal shock.
- The reflow process is not just about reaching a specific temperature; it involves a carefully controlled temperature profile with distinct phases:
-
Importance of Temperature Control:
- Maintaining the correct reflow temperature is critical for achieving high-quality solder joints. Too low a temperature may result in incomplete melting and weak connections, while too high a temperature can damage components or cause warping of the PCB.
- Modern reflow ovens use precise temperature control and profiling to ensure consistent results across the entire PCB.
-
Lead-Free vs. Leaded Solder:
- Lead-free solder alloys, such as Sn/Ag or Sn/Ag/Cu, require higher reflow temperatures compared to traditional leaded solder (e.g., Sn/Pb). Leaded solder typically reflows at around 183°C, but lead-free alloys require temperatures closer to 240–250°C due to their higher melting points.
- The shift to lead-free soldering is driven by environmental and regulatory requirements, such as the Restriction of Hazardous Substances (RoHS) directive.
-
Practical Considerations for Equipment Purchasers:
- When selecting reflow equipment, consider the following:
- Temperature Uniformity: Ensure the oven can maintain consistent temperatures across the entire heating zone.
- Profile Flexibility: Look for ovens that allow customization of the reflow profile to accommodate different solder alloys and component types.
- Cooling Capability: Adequate cooling is essential to prevent thermal stress and ensure the integrity of solder joints.
- Energy Efficiency: Modern reflow ovens often include energy-saving features, such as optimized heating elements and insulation.
- When selecting reflow equipment, consider the following:
By understanding the reflow temperature and its influencing factors, equipment and consumable purchasers can make informed decisions to ensure high-quality soldering results and minimize production defects.
Summary Table:
Key Aspect | Details |
---|---|
Purpose of Reflow Process | Melts solder paste to create strong electrical and mechanical connections. |
Typical Reflow Temperature | 240–250°C for lead-free solder alloys (e.g., Sn/Ag). |
Influencing Factors | Solder alloy, component specs, PCB design. |
Reflow Profile Phases | Preheat, Soak, Reflow, Cooling. |
Importance of Control | Ensures quality solder joints without damaging components or PCB. |
Lead-Free vs. Leaded | Lead-free requires higher temperatures (240–250°C) than leaded (183°C). |
Equipment Considerations | Temperature uniformity, profile flexibility, cooling capability, efficiency. |
Ensure flawless SMT assembly with the right reflow process—contact our experts today for tailored solutions!