Vacuum hardening is a heat treatment process used to enhance the mechanical properties of metals, particularly steel, by heating them in a vacuum environment to prevent oxidation and decarburization. The temperature for vacuum hardening typically ranges between 800°C and 1300°C, depending on the material being treated and the desired properties. The process involves precise temperature control and uniformity, which is achieved through advanced furnace design, including circulation fans, heating elements, and control systems. The vacuum environment ensures a clean, oxidation-free surface, leading to improved hardness, wear resistance, and overall performance of the treated material.
Key Points Explained:
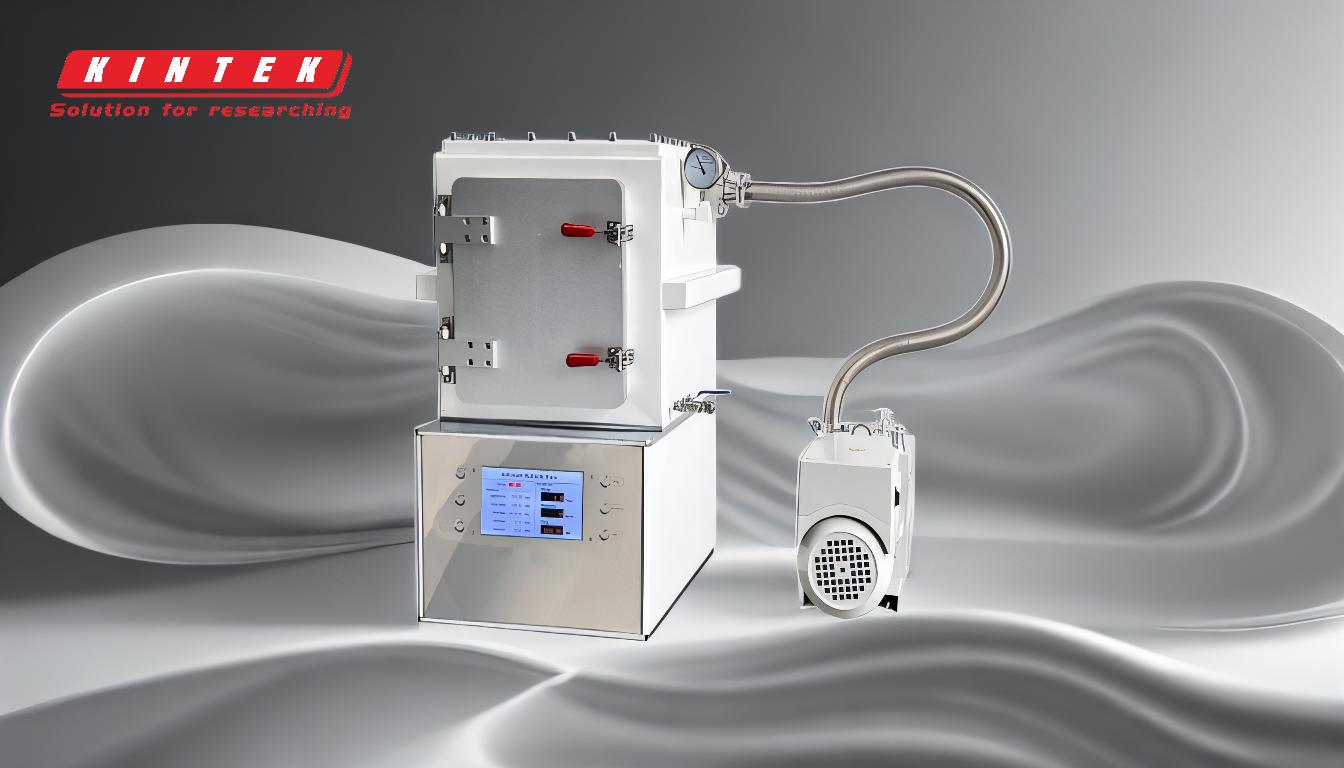
-
Temperature Range for Vacuum Hardening:
- Vacuum hardening temperatures generally range from 800°C to 1300°C. This range varies based on the type of material and the specific hardening requirements.
- For example, tool steels may require temperatures closer to 1000°C to 1300°C, while other alloys might harden effectively at lower temperatures.
-
Importance of Temperature Uniformity:
- Temperature uniformity is critical in vacuum hardening to ensure consistent material properties throughout the workpiece.
- This is achieved through the design of the vacuum hardening furnace, including features like circulation fans, ventilation blisters, and optimized heating element layouts. These components work together to distribute heat evenly across the furnace chamber.
-
Role of the Vacuum Environment:
- The vacuum environment prevents oxidation and decarburization, which are common issues in traditional hardening processes.
- By eliminating air, the vacuum ensures a clean surface finish and enhances the material's mechanical properties, such as hardness and wear resistance.
-
Control Systems for Temperature Regulation:
- Modern vacuum hardening furnaces use advanced control systems to maintain precise temperatures. These systems include:
- Proportional control: Adjusts both fuel and air supply for efficient and consistent heating.
- Pulse control: Maintains a fixed fuel-to-air ratio while ensuring high flame velocity, which stabilizes temperature distribution.
- These control methods improve energy efficiency and reduce operating costs while maintaining process quality.
- Modern vacuum hardening furnaces use advanced control systems to maintain precise temperatures. These systems include:
-
Applications and Benefits:
- Vacuum hardening is widely used in industries requiring high-performance components, such as aerospace, automotive, and tool manufacturing.
- Benefits include:
- Enhanced hardness and wear resistance.
- Improved surface finish without oxidation.
- Greater control over material properties, leading to longer-lasting components.
-
Comparison with Other Heat Treatment Processes:
- Unlike sintering, which operates below the material's melting point to shape it without liquefaction, vacuum hardening focuses on altering the material's microstructure to improve strength and durability.
- The vacuum environment sets it apart from traditional hardening methods, which often require additional post-treatment steps to remove oxidation.
By understanding these key points, equipment and consumable purchasers can make informed decisions about selecting the right vacuum hardening furnace and optimizing the process for their specific needs.
Summary Table:
Key Aspect | Details |
---|---|
Temperature Range | 800°C to 1300°C, depending on material and hardening requirements. |
Temperature Uniformity | Achieved via circulation fans, ventilation blisters, and optimized heating. |
Vacuum Environment | Prevents oxidation and decarburization, ensuring a clean surface finish. |
Control Systems | Proportional and pulse control for precise temperature regulation. |
Applications | Aerospace, automotive, and tool manufacturing industries. |
Benefits | Enhanced hardness, wear resistance, and longer-lasting components. |
Optimize your vacuum hardening process—contact our experts today for tailored solutions!