The temperature of vapor deposition, particularly in chemical vapor deposition (CVD), typically ranges around 1000°C. This high temperature is necessary to facilitate the chemical reactions between the gaseous phase and the heated substrate surface, ensuring efficient deposition. The exact temperature can vary depending on factors such as the type of substrate, its surface preparation, and the specific requirements of the deposition process. Understanding these parameters is crucial for determining the most suitable conditions for effective vapor deposition.
Key Points Explained:
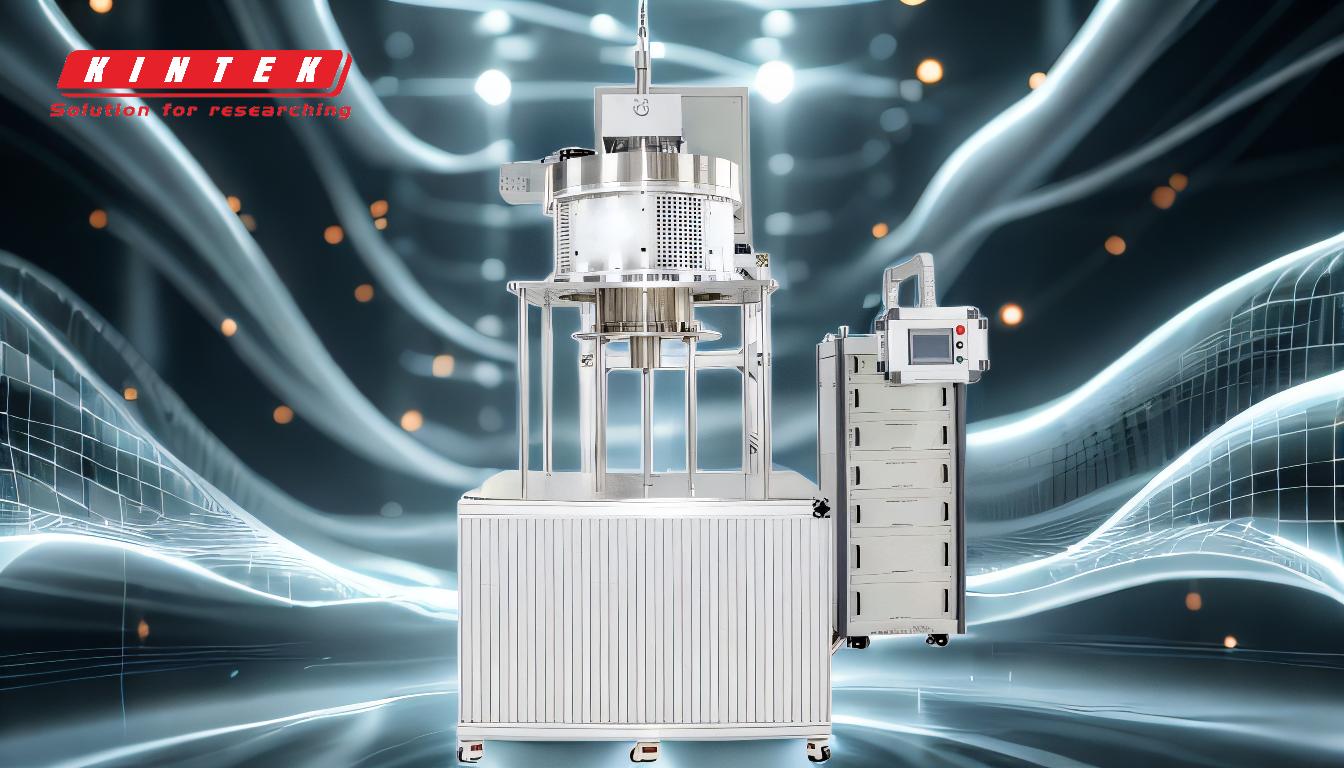
-
Temperature Range in CVD:
- The temperature for chemical vapor deposition typically ranges around 1000°C. This high temperature is essential for the chemical reactions to occur between the gaseous precursors and the substrate surface. The heat provides the necessary energy for the precursors to decompose and react, forming a solid deposit on the substrate.
-
Pressure Conditions:
- CVD processes operate under a wide range of pressures, from a few torr to above atmospheric pressure. The pressure conditions are chosen based on the specific requirements of the deposition process and the materials involved. Lower pressures can lead to more uniform coatings, while higher pressures might be necessary for certain types of reactions.
-
Substrate Influence:
- The type of substrate and its surface preparation play a significant role in the deposition process. The substrate's temperature during deposition affects the sticking coefficient, which is a measure of how well the deposited material adheres to the substrate. Proper surface preparation and optimal temperature settings are crucial for achieving high-quality coatings.
-
Historical Context:
- The concept of CVD has ancient roots, as illustrated by the example of cavemen using lamps, where soot deposited on cave walls represented a primitive form of CVD. This historical perspective highlights the fundamental principles of the process, which have been refined and developed over time into the sophisticated technology used today.
-
Process Optimization:
- Knowledge of substrate compatibility with precursors and the optimal temperature for efficient deposition is crucial. This understanding helps in selecting the most suitable process parameters, ensuring that the deposition is both effective and efficient. Factors such as the chemical nature of the precursors, the desired properties of the deposited film, and the specific application requirements all influence the optimization of the CVD process.
By considering these key points, one can better understand the complexities and requirements of the chemical vapor deposition process, particularly the critical role of temperature in achieving successful deposition outcomes.
Summary Table:
Parameter | Details |
---|---|
Temperature Range | Typically around 1000°C for CVD |
Pressure Conditions | Ranges from a few torr to above atmospheric pressure |
Substrate Influence | Affects sticking coefficient and coating quality |
Historical Context | Ancient roots in soot deposition on cave walls |
Process Optimization | Depends on substrate compatibility, precursor chemistry, and application |
Ready to optimize your vapor deposition process? Contact our experts today for tailored solutions!