Brazing is a metal-joining process that involves heating a filler metal above its melting point and distributing it between two or more close-fitting parts by capillary action. The temperature range for brazing typically falls between 450°C (842°F) and 900°C (1652°F), depending on the materials being joined and the type of filler metal used. This range is chosen to ensure that the filler metal melts and flows properly without damaging the base materials. The specific temperature depends on factors such as the melting point of the filler metal, the thermal properties of the base metals, and the desired joint strength. Brazing is widely used in industries like automotive, aerospace, and HVAC due to its ability to create strong, leak-proof joints.
Key Points Explained:
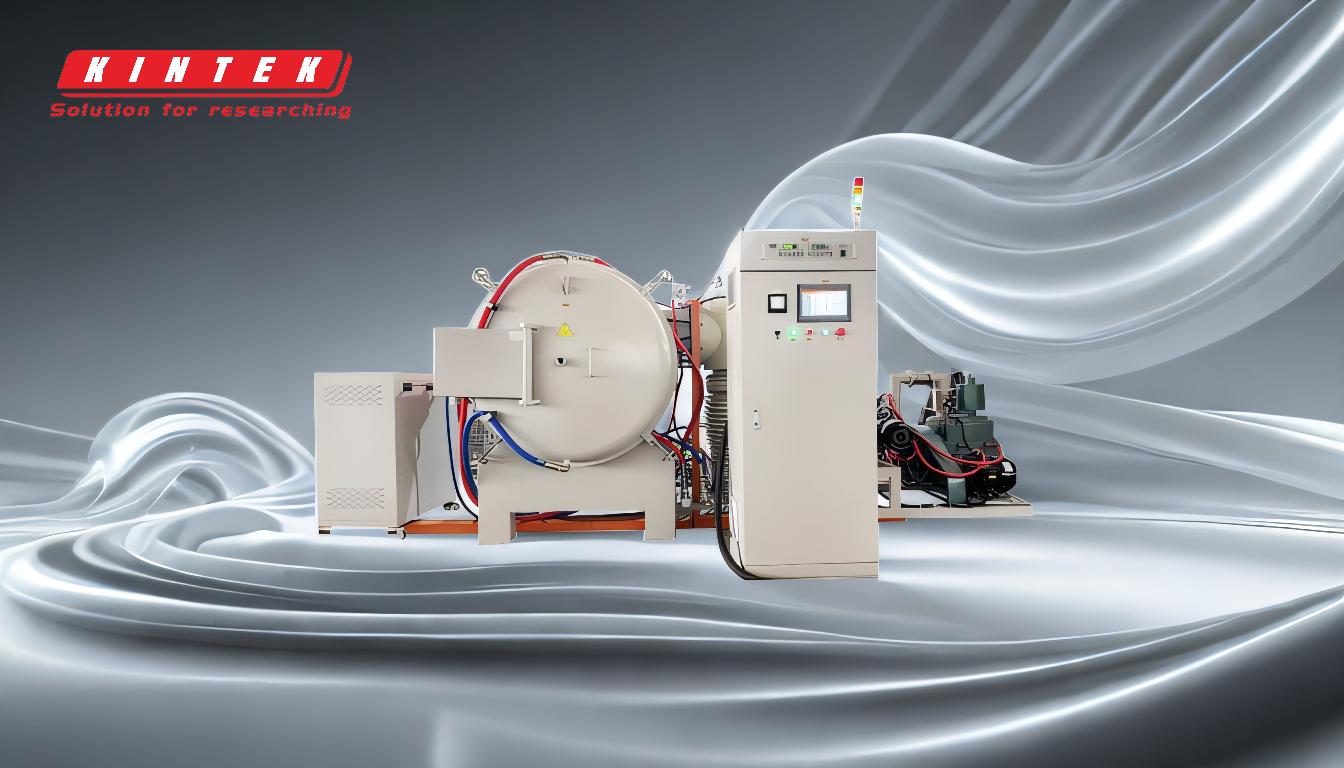
-
Definition of Brazing:
- Brazing is a metal-joining process that uses a filler metal with a melting point above 450°C (842°F) but below the melting point of the base metals being joined. The filler metal flows into the joint by capillary action, creating a strong bond.
-
Temperature Range for Brazing:
- The typical temperature range for brazing is 450°C to 900°C (842°F to 1652°F). This range ensures that the filler metal melts and flows properly while the base metals remain solid.
- The exact temperature depends on the type of filler metal and the base materials. For example:
- Aluminum brazing: 580°C to 620°C (1076°F to 1148°F).
- Copper brazing: 600°C to 900°C (1112°F to 1652°F).
- Silver brazing: 620°C to 840°C (1148°F to 1544°F).
-
Factors Influencing Brazing Temperature:
- Filler Metal Melting Point: The filler metal must melt at a temperature lower than the base metals but high enough to ensure proper flow and bonding.
- Base Metal Properties: The thermal conductivity and melting point of the base metals determine the maximum temperature that can be used without causing damage.
- Joint Design: The gap between the parts being joined affects the capillary action and the flow of the filler metal.
- Application Requirements: The desired strength, corrosion resistance, and thermal performance of the joint influence the choice of filler metal and brazing temperature.
-
Advantages of Brazing:
- Strong Joints: Brazed joints are often stronger than the base metals due to the metallurgical bond formed.
- Leak-Proof Seals: Brazing creates leak-proof joints, making it ideal for applications like plumbing and refrigeration.
- Versatility: Brazing can join dissimilar metals, such as copper to steel or aluminum to stainless steel.
- Minimal Distortion: Since the base metals do not melt, brazing causes less distortion compared to welding.
-
Common Applications of Brazing:
- Automotive Industry: Used for joining components like radiators, heat exchangers, and air conditioning systems.
- Aerospace Industry: Brazing is used for assembling turbine blades, fuel systems, and other critical components.
- HVAC Systems: Brazing is essential for creating leak-proof joints in refrigeration and air conditioning systems.
- Electronics: Used for joining electrical contacts and heat sinks.
-
Types of Brazing Processes:
- Torch Brazing: Uses a gas flame to heat the joint and filler metal. Suitable for small-scale or manual operations.
- Furnace Brazing: Involves heating the entire assembly in a controlled atmosphere furnace. Ideal for mass production.
- Induction Brazing: Uses electromagnetic induction to heat the joint. Suitable for precise, localized heating.
- Dip Brazing: The assembly is immersed in a molten salt or metal bath to achieve the required temperature.
-
Safety Considerations:
- Ventilation: Ensure proper ventilation to avoid inhaling fumes from the filler metal or flux.
- Protective Gear: Wear heat-resistant gloves, goggles, and clothing to protect against burns and splashes.
- Flux Handling: Use flux to prevent oxidation and improve wetting, but handle it carefully as it can be corrosive.
By understanding the temperature range and key factors involved in brazing, you can select the appropriate materials and methods for your specific application, ensuring strong and reliable joints.
Summary Table:
Aspect | Details |
---|---|
Temperature Range | 450°C to 900°C (842°F to 1652°F) |
Aluminum Brazing | 580°C to 620°C (1076°F to 1148°F) |
Copper Brazing | 600°C to 900°C (1112°F to 1652°F) |
Silver Brazing | 620°C to 840°C (1148°F to 1544°F) |
Key Factors | Filler metal melting point, base metal properties, joint design, application requirements |
Advantages | Strong joints, leak-proof seals, versatility, minimal distortion |
Common Applications | Automotive, aerospace, HVAC, electronics |
Need help selecting the right brazing process for your project? Contact our experts today!