The temperature range for pyrolysis varies depending on the type of pyrolysis process being conducted. Generally, pyrolysis can occur at temperatures ranging from 350°C to 1200°C, depending on the specific application and desired output. For instance, high-temperature pyrolysis typically occurs at 350-400°C, medium-temperature pyrolysis at 600-700°C, and processes involving liquid and gaseous species can reach temperatures between 700-1200°C. These temperature ranges are crucial for breaking down waste materials into valuable products such as pyrolysis oil, carbon black, and syn-gas.
Key Points Explained:
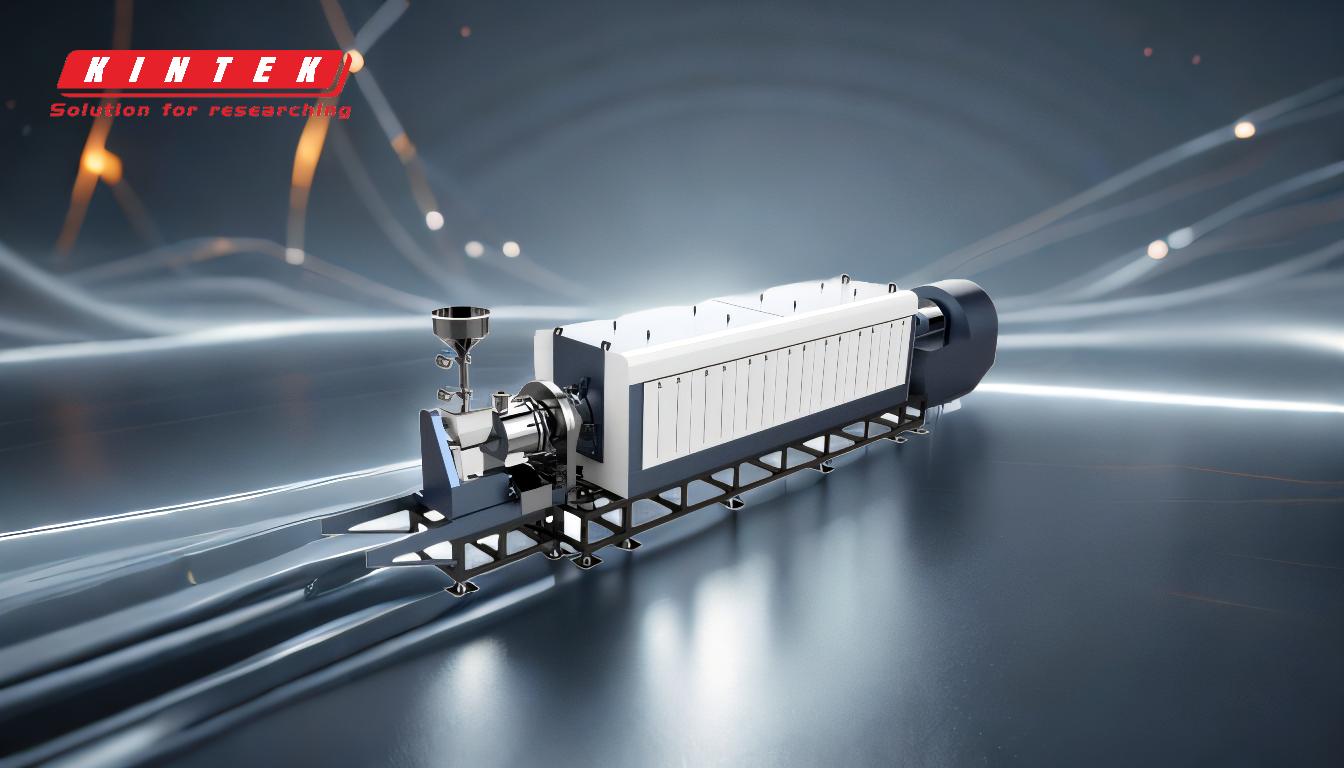
-
High-Temperature Pyrolysis (350-400°C):
- This temperature range is necessary for the high-temperature pyrolysis process.
- It leads to the breakdown of waste materials into valuable products like pyrolysis oil, carbon black, and syn-gas.
- This range is typically used when the goal is to maximize the production of gases and oils.
-
Medium-Temperature Pyrolysis (600-700°C):
- Medium temperature pyrolysis generally occurs between 600 and 700 °C.
- This range is often used for processes that require a balance between gas, liquid, and solid products.
- It is suitable for applications where a moderate temperature is sufficient to break down the feedstock without excessive energy consumption.
-
High-Temperature Pyrolysis for Liquid and Gaseous Species (700-1200°C):
- Pyrolysis processes involving liquid and gaseous species are typically carried out at temperatures ranging from 700 to 1200°C.
- These high temperatures are necessary for the complete breakdown of complex molecules into simpler gaseous and liquid products.
- The process is often conducted in externally heated reactor tubes made of refractory alloys to withstand the high temperatures.
-
Slow Pyrolysis:
- Slow pyrolysis is carried out in an oxygen-limited or oxygen-free environment.
- Typical heating rates are between 1 and 30 °C min−1.
- It is usually conducted at atmospheric pressure, and the process heat is typically supplied from an external energy source, such as the combustion of produced gases or partial combustion of the biomass feedstock.
- This method is often used to maximize the production of biochar, a solid residue rich in carbon.
-
Pressure Considerations:
- Pyrolysis processes involving liquid and gaseous species are typically carried out at pressures between 1-30 bar.
- The pressure can influence the yield and composition of the pyrolysis products.
- Higher pressures can lead to increased production of liquid products, while lower pressures favor the formation of gases.
-
Reactor Design:
- The design of the pyrolysis reactor is crucial for maintaining the desired temperature and pressure conditions.
- Reactors are often made of refractory alloys to withstand high temperatures and corrosive environments.
- The length and diameter of the reactor tubes (20-30 meters long and 1-2 inches in diameter) are optimized to ensure efficient heat transfer and product yield.
Understanding these temperature ranges and their implications is essential for selecting the appropriate pyrolysis process based on the desired products and feedstock characteristics.
Summary Table:
Pyrolysis Type | Temperature Range | Key Products | Applications |
---|---|---|---|
High-Temperature Pyrolysis | 350-400°C | Pyrolysis oil, carbon black, syn-gas | Maximizes gas and oil production |
Medium-Temperature Pyrolysis | 600-700°C | Balanced gas, liquid, solid products | Moderate temperature for efficient feedstock breakdown |
High-Temperature for Gases/Liquids | 700-1200°C | Gaseous and liquid products | Complete breakdown of complex molecules |
Slow Pyrolysis | 1-30°C/min heating | Biochar | Maximizes biochar production in oxygen-limited environments |
Pressure Considerations | 1-30 bar | Influences product yield | Higher pressure favors liquids; lower pressure favors gases |
Reactor Design | 20-30m long, 1-2in diameter | Optimized heat transfer | Ensures efficient product yield and withstands high temperatures and corrosion |
Ready to optimize your pyrolysis process? Contact our experts today for tailored solutions!