Pyrolysis oil, also known as bio-oil, is a complex, oxygenated hydrocarbon mixture derived from biomass through pyrolysis. Its temperature range during production is critical for optimizing yield and quality. The optimal temperature range for producing pyrolysis oil is typically between 500°C and 600°C, with fast pyrolysis conditions (heating rates of around 1000°C/s and short residence times) yielding the highest bio-oil output (60-70 wt%). This temperature range ensures efficient biomass decomposition while minimizing secondary reactions that could degrade the oil's quality. Pyrolysis oil is thermally unstable, corrosive, and has a high water content (20-30 wt-%), making it distinct from conventional fossil fuels. Its properties, such as low pH, high viscosity, and high oxygen content, can be improved using catalysts during the pyrolysis process.
Key Points Explained:
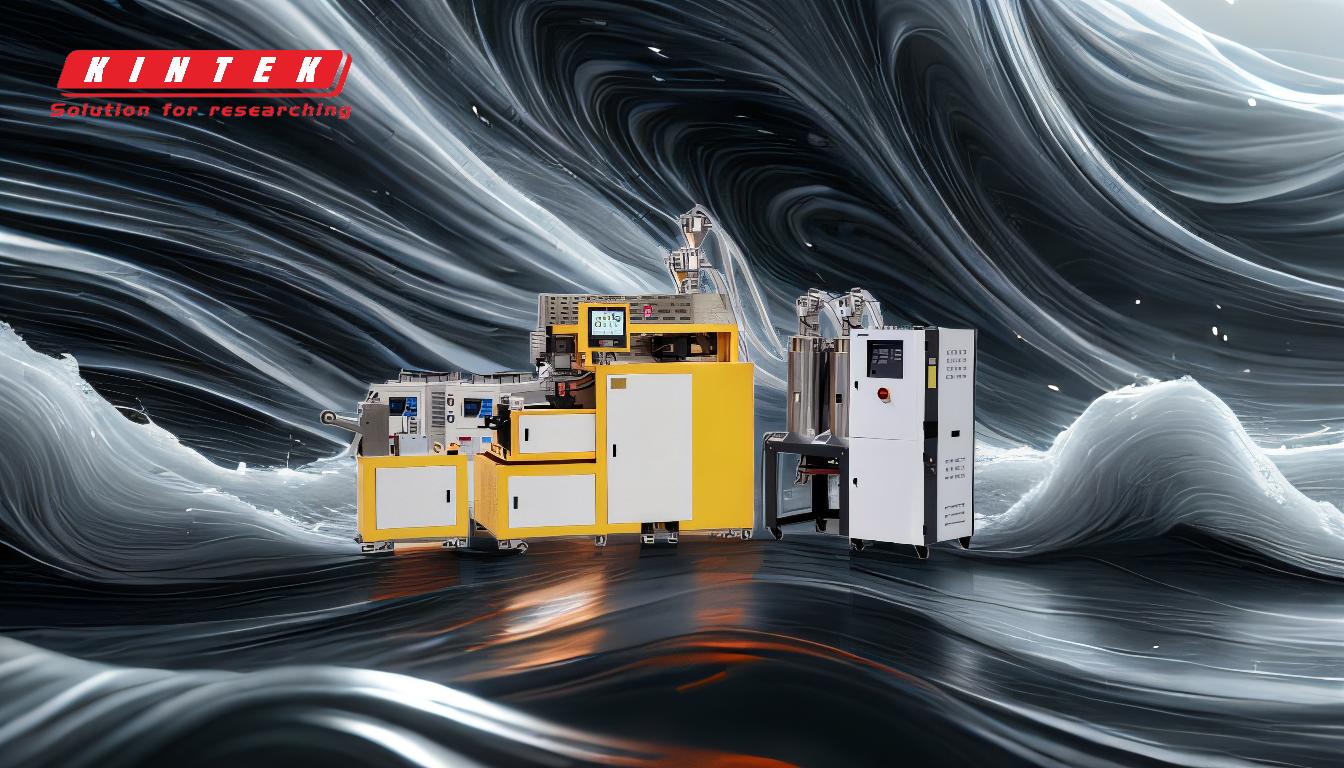
-
Optimal Temperature Range for Pyrolysis Oil Production:
- The ideal temperature range for producing pyrolysis oil is 500°C to 600°C.
- This range maximizes bio-oil yield (60-70 wt%) while minimizing production costs.
- Higher temperatures beyond this range can lead to secondary cracking reactions, reducing oil yield and quality.
-
Fast Pyrolysis Conditions:
- Fast pyrolysis involves rapid heating of biomass particles at rates of approximately 1000°C/s.
- Short residence times of pyrolysis vapors and fast quenching are essential to condense the bio-oil effectively.
- These conditions are critical for achieving high bio-oil yields and maintaining its quality.
-
Properties of Pyrolysis Oil:
- High Water Content: Pyrolysis oil typically contains 20-30 wt-% water, which affects its stability and energy density.
- Low pH and Corrosiveness: The oil is acidic and corrosive, requiring specialized storage and handling equipment.
- High Viscosity: The oil is highly viscous, which can complicate its use in certain applications.
- High Oxygen Content: The oil's high oxygen content (up to 40 wt-%) makes it thermally unstable and prone to polymerization over time.
-
Thermal Stability and Storage Challenges:
- Pyrolysis oil is thermally unstable and tends to polymerize when exposed to air, leading to increased viscosity over time.
- It cannot be completely re-vaporized once recovered, limiting its reusability in some processes.
- Proper storage conditions, such as low temperatures and inert atmospheres, are necessary to maintain its stability.
-
Comparison to Fossil Fuels:
- Pyrolysis oil has a similar viscosity and heating value to diesel fuel but differs significantly in other properties.
- It has a higher sulfur content and a lower flashpoint, making it less suitable for direct use in conventional engines without upgrading.
- Its immiscibility with fossil fuels further complicates its integration into existing fuel infrastructure.
-
Catalytic Upgrading:
- The use of catalysts during pyrolysis can enhance the quality of the bio-oil by reducing oxygen content and improving stability.
- Catalytic upgrading can also improve the oil's heating value and volatility, making it more compatible with conventional fuels.
-
Applications and Limitations:
- Pyrolysis oil is used in boilers, turbines, and as a feedstock for producing chemicals and biofuels.
- Its corrosive nature and thermal instability limit its direct use in internal combustion engines.
- Ongoing research focuses on improving its properties through upgrading and blending with other fuels.
By understanding the temperature range and conditions required for pyrolysis oil production, as well as its unique properties and challenges, stakeholders can better optimize its production and utilization in various applications.
Summary Table:
Key Aspect | Details |
---|---|
Optimal Temperature Range | 500°C to 600°C |
Bio-Oil Yield | 60-70 wt% |
Heating Rate | ~1000°C/s (fast pyrolysis) |
Water Content | 20-30 wt-% |
Key Properties | High viscosity, low pH, high oxygen content, thermally unstable |
Storage Requirements | Low temperatures, inert atmospheres |
Applications | Boilers, turbines, chemical feedstock, biofuels |
Challenges | Corrosive, thermally unstable, immiscible with fossil fuels |
Optimize your pyrolysis oil production—contact our experts today for tailored solutions!