A muffle furnace is a specialized heating device designed to achieve high temperatures for processes such as smelting, casting, heat treatment, and combustion analysis. It operates on the principles of electrical heating, insulation, and temperature control. The furnace uses heating elements, often made of materials like Nichrome, to generate heat, which is then transferred to a refractory-lined chamber. This chamber, or muffle, isolates the sample from combustion byproducts and prevents heat loss, ensuring efficient and controlled heating. Modern muffle furnaces incorporate advanced features such as PID controllers and thermocouples for precise temperature regulation. They are widely used in industrial and research applications due to their energy efficiency, rapid heating and cooling capabilities, and ability to maintain high temperatures in a controlled environment.
Key Points Explained:
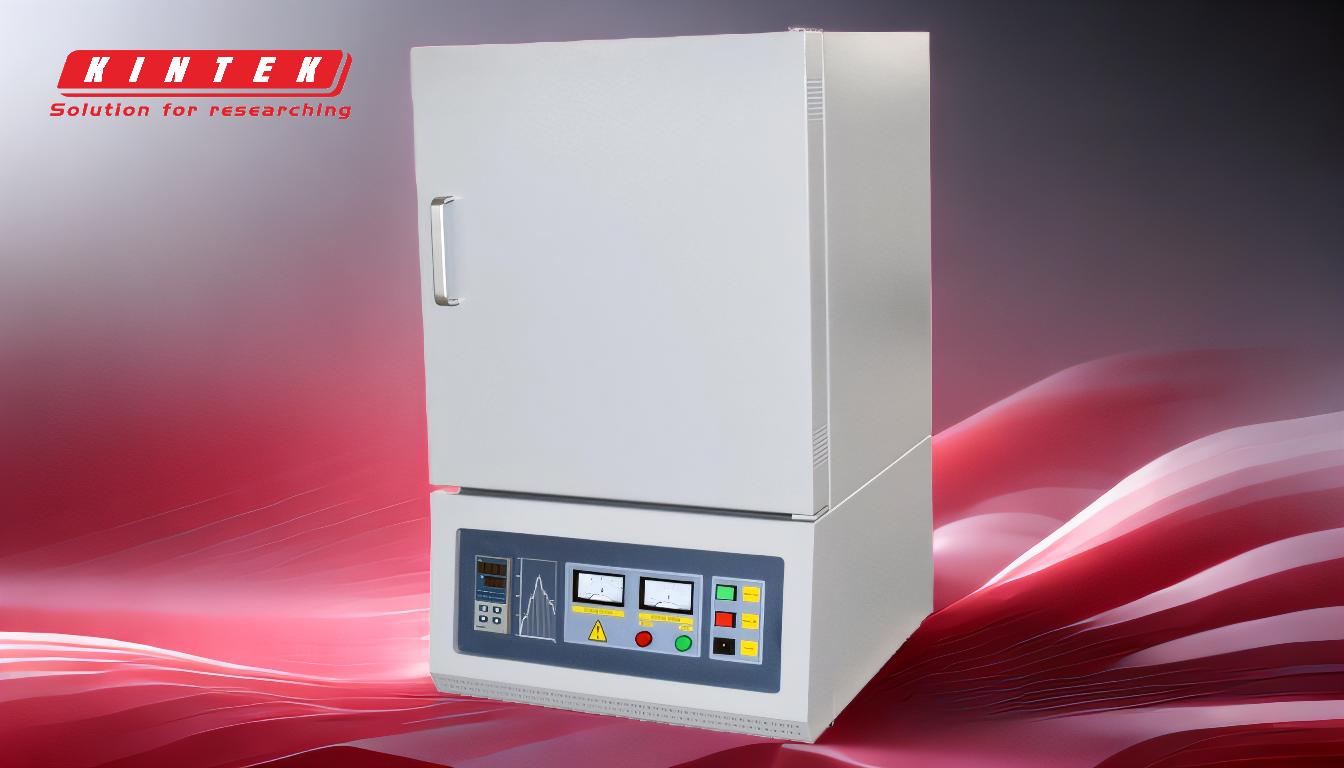
-
Basic Working Principle:
- A muffle furnace operates by converting electrical energy into heat using heating elements.
- The heat is transferred to a chamber (muffle) made of refractory materials, which insulates the chamber and prevents heat loss.
- The sample or workpiece is placed inside this chamber and heated to the desired temperature.
-
Heating Mechanism:
- Heating elements, typically made of Nichrome or other high-resistance materials, are located outside the muffle chamber.
- These elements heat the walls of the chamber, which then radiate heat to the sample inside.
- The temperature is controlled by adjusting the power supplied to the heating elements.
-
Insulation and Heat Retention:
- The muffle chamber is lined with refractory materials such as ceramic fiber or bricks.
- These materials provide excellent insulation, minimizing heat loss and ensuring high thermal efficiency.
- The insulation also protects the outer structure of the furnace from damage due to high temperatures.
-
Temperature Control:
- Modern muffle furnaces are equipped with PID (Proportional-Integral-Derivative) controllers for precise temperature regulation.
- A thermocouple is used to monitor the temperature inside the chamber, and the PID controller adjusts the power to the heating elements to maintain the set temperature.
- This ensures consistent and accurate heating, which is crucial for processes like heat treatment and combustion analysis.
-
Separation of Sample and Combustion Byproducts:
- One of the key features of a muffle furnace is the separation of the sample from the heat source and any combustion byproducts.
- This is achieved by the muffle chamber, which isolates the sample and ensures that it is heated in a clean environment.
- This feature is particularly important for applications like ash content determination, where contamination from combustion byproducts must be avoided.
-
Applications:
- Muffle furnaces are used in a wide range of industrial and research applications, including:
- Heat treatment of metals and alloys.
- Smelting and casting processes.
- Combustion analysis and ash content determination.
- Ceramic and glass processing.
- Their ability to achieve and maintain high temperatures in a controlled environment makes them indispensable in these fields.
- Muffle furnaces are used in a wide range of industrial and research applications, including:
-
Energy Efficiency and Rapid Heating/Cooling:
- Muffle furnaces are designed to be energy-efficient, with insulated chambers that retain heat and reduce energy consumption.
- They are capable of rapid heating and cooling, which is essential for processes that require quick temperature changes.
- The self-contained nature of the furnace cabinets further enhances their efficiency and ease of use.
-
Safety Features:
- Muffle furnaces are equipped with safety features to prevent overheating and ensure safe operation.
- These may include thermal cutoffs, over-temperature protection, and alarms to alert users to any issues.
- The robust construction and insulation also contribute to the overall safety of the furnace.
In summary, a muffle furnace is a versatile and efficient heating device that operates on the principles of electrical heating, insulation, and precise temperature control. Its ability to isolate samples from combustion byproducts, combined with its energy efficiency and rapid heating/cooling capabilities, makes it an essential tool in various industrial and research applications.
Summary Table:
Feature | Description |
---|---|
Working Principle | Converts electrical energy into heat using heating elements. |
Heating Mechanism | Nichrome elements heat the chamber walls, radiating heat to the sample. |
Insulation | Refractory materials minimize heat loss and ensure thermal efficiency. |
Temperature Control | PID controllers and thermocouples maintain precise temperature regulation. |
Sample Isolation | Muffle chamber isolates samples from combustion byproducts. |
Applications | Heat treatment, smelting, combustion analysis, ceramic/glass processing. |
Energy Efficiency | Insulated chambers reduce energy consumption and enable rapid heating/cooling. |
Safety Features | Includes thermal cutoffs, over-temperature protection, and alarms. |
Ready to enhance your lab's capabilities with a muffle furnace? Contact us today for expert guidance!