The thinnest coating currently achievable is a monolayer coating, which is just one atom or molecule thick. These coatings are often created using advanced techniques like atomic layer deposition (ALD) or molecular self-assembly. Monolayer coatings are used in applications requiring extreme precision, such as semiconductor manufacturing, nanotechnology, and advanced optics. Despite their minimal thickness, they provide significant functional benefits, including enhanced conductivity, corrosion resistance, and optical properties. However, their application is limited by the complexity of the deposition process and the high cost of production.
Key Points Explained:
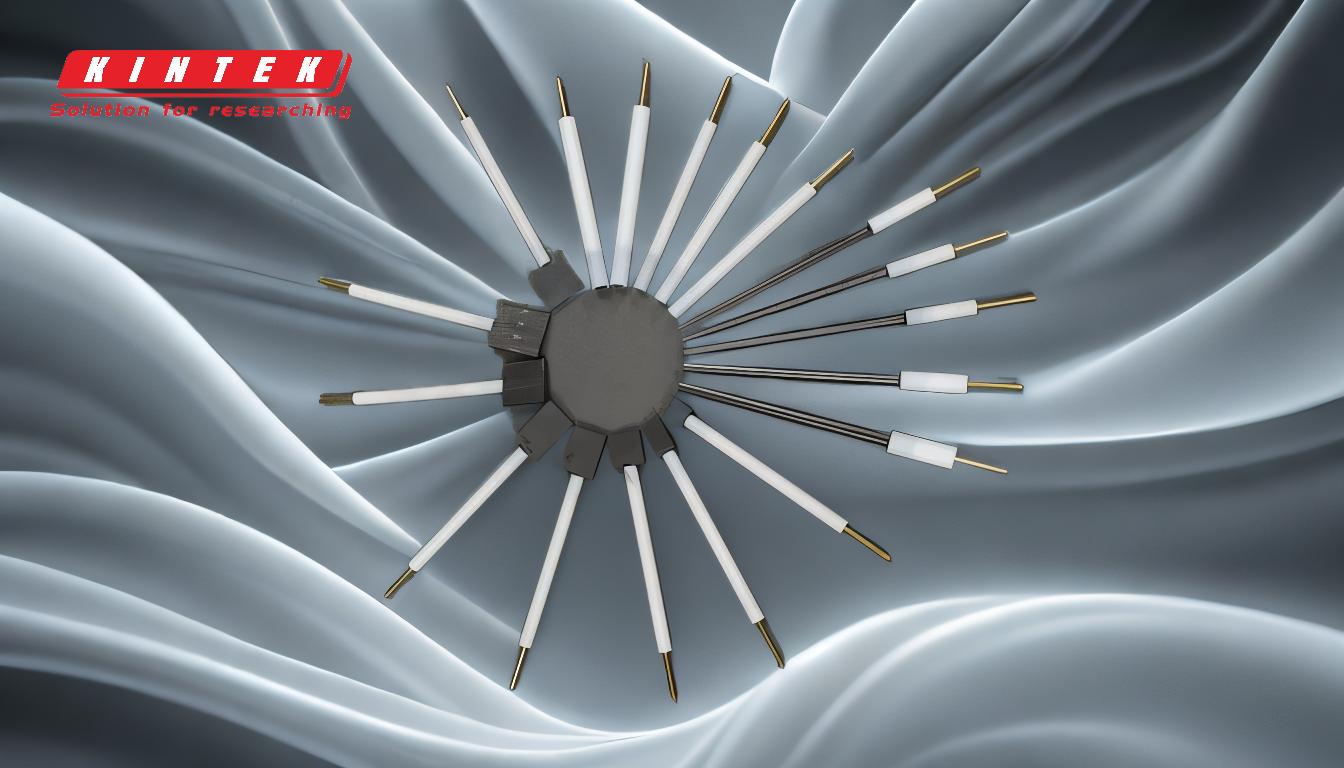
-
Definition of Monolayer Coatings:
- A monolayer coating is the thinnest possible coating, consisting of a single layer of atoms or molecules. This makes it approximately 0.1 to 1 nanometer thick, depending on the material used.
-
Techniques for Creating Monolayer Coatings:
- Atomic Layer Deposition (ALD): A precise technique that deposits one atomic layer at a time, ensuring uniform thickness and high-quality coatings. ALD is widely used in semiconductor and nanotechnology industries.
- Molecular Self-Assembly: A process where molecules spontaneously organize into a structured monolayer. This method is often used in creating coatings for sensors and biomedical devices.
-
Applications of Monolayer Coatings:
- Semiconductors: Monolayer coatings are critical in the production of transistors and other microelectronic components, where precise thickness is essential.
- Optics: Used in anti-reflective coatings and advanced optical filters, monolayer coatings improve light transmission and reduce glare.
- Corrosion Resistance: Applied to metals, these coatings provide a protective barrier against environmental degradation without adding bulk.
-
Advantages of Monolayer Coatings:
- Extreme Precision: The ability to control thickness at the atomic level ensures uniformity and consistency.
- Enhanced Properties: Despite their thinness, monolayer coatings can significantly improve electrical, optical, and mechanical properties.
- Minimal Material Usage: Reduces material costs and waste, making it an environmentally friendly option.
-
Challenges and Limitations:
- Complex Deposition Process: Techniques like ALD require specialized equipment and expertise, increasing production costs.
- Fragility: Due to their thinness, monolayer coatings can be more susceptible to damage during handling or use.
- Limited Scalability: Producing large-area monolayer coatings remains a challenge, restricting their use in some industrial applications.
-
Future Prospects:
- Research is ongoing to improve the scalability and durability of monolayer coatings. Advances in materials science and deposition techniques are expected to expand their applications in fields like energy storage, flexible electronics, and biomedical engineering.
By understanding these key points, equipment and consumable purchasers can evaluate whether monolayer coatings are suitable for their specific needs and explore potential applications in their industries.
Summary Table:
Aspect | Details |
---|---|
Thickness | 0.1 to 1 nanometer (single atom/molecule thick) |
Creation Techniques | Atomic Layer Deposition (ALD), Molecular Self-Assembly |
Applications | Semiconductors, Optics, Corrosion Resistance |
Advantages | Extreme precision, enhanced properties, minimal material usage |
Challenges | Complex deposition process, fragility, limited scalability |
Future Prospects | Improved scalability, durability, and expanded applications |
Discover how monolayer coatings can revolutionize your industry—contact our experts today!