A muffle furnace is a critical tool in soil analysis, primarily used for determining soil organic matter, analyzing water content, and preparing samples for trace metal analysis. It operates by heating materials at high temperatures without contamination from combustion gases, ash, or residue, ensuring accurate and reliable results. This equipment is essential in scientific research, environmental testing, and industrial applications, as it allows for precise thermal processing and analysis of materials. Its versatility makes it indispensable for tasks such as ash determination, heat treatment, and sample preparation in fields like soil science, environmental studies, and metallurgy.
Key Points Explained:
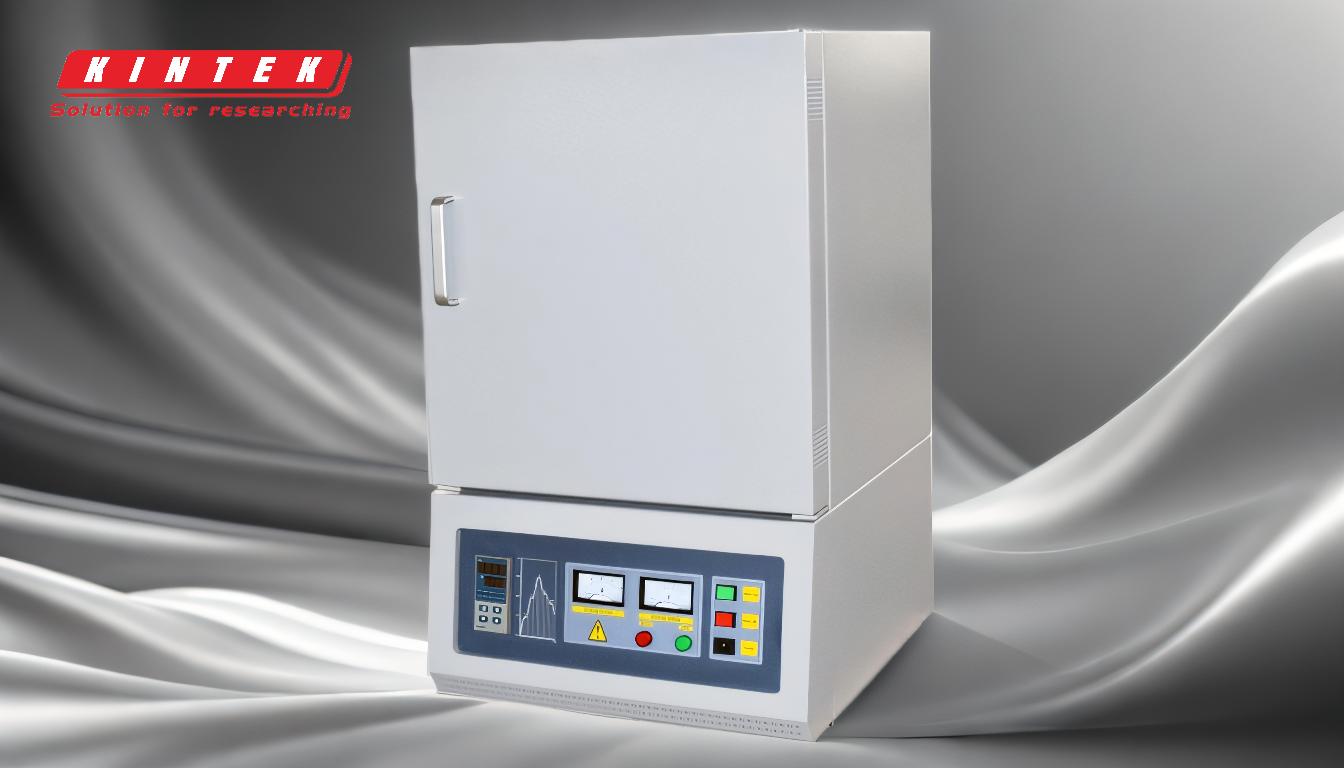
-
Soil Organic Matter Determination
- Muffle furnaces are used to measure the organic matter content in soil.
- The process involves heating soil samples to high temperatures (typically between 350°C and 550°C) to burn off organic components, leaving behind inorganic residues.
- This method is critical for understanding soil fertility, carbon sequestration, and environmental health.
-
Water Content Analysis
- Muffle furnaces help determine the moisture content in soil samples.
- By heating the sample to a specific temperature, water evaporates, and the weight loss is measured to calculate the water content.
- Accurate water content analysis is essential for soil classification, agricultural planning, and environmental monitoring.
-
Sample Preparation for Trace Metal Analysis
- Muffle furnaces are used to prepare soil samples for trace metal analysis by ashing organic materials.
- This process ensures that only inorganic components remain, which can then be analyzed for trace metals like lead, cadmium, and arsenic.
- Trace metal analysis is vital for assessing soil contamination and ensuring environmental safety.
-
Contamination-Free Heating
- A key advantage of muffle furnaces is their ability to heat materials without contamination from combustion gases or ash.
- This is achieved by isolating the sample in a sealed chamber, ensuring that only the sample is exposed to high temperatures.
- This feature is crucial for obtaining accurate and reproducible results in soil and environmental analysis.
-
Versatility in Applications
- Beyond soil analysis, muffle furnaces are used in various scientific and industrial applications, including:
- Ash determination in coal and other materials.
- Heat treatment processes like annealing, quenching, and sintering.
- Sample preparation for water quality analysis, environmental studies, and petroleum analysis.
- Their ability to provide precise and controlled heating makes them indispensable in research and industrial settings.
- Beyond soil analysis, muffle furnaces are used in various scientific and industrial applications, including:
-
High-Temperature Capabilities
- Muffle furnaces can reach temperatures up to 1,800°C, making them suitable for advanced applications like metallurgical testing and ceramic sintering.
- This high-temperature capability ensures that even the most demanding soil and environmental analyses can be performed effectively.
-
Role in Environmental and Industrial Research
- Muffle furnaces are widely used in environmental research to study soil properties, contamination levels, and ecosystem health.
- They are also employed in industrial settings for quality control, material testing, and process optimization.
- Their ability to handle a wide range of materials and applications underscores their importance in both scientific and commercial contexts.
In summary, muffle furnaces are indispensable tools in soil and environmental analysis, offering precise, contamination-free heating for a variety of applications. Their ability to determine soil organic matter, analyze water content, and prepare samples for trace metal analysis makes them essential for understanding soil health and environmental safety. Additionally, their versatility and high-temperature capabilities extend their use to industrial and research applications, ensuring accurate and reliable results across diverse fields.
Summary Table:
Application | Key Details |
---|---|
Soil Organic Matter Determination | Burns organic components at 350°C-550°C, leaving inorganic residues. |
Water Content Analysis | Measures weight loss after heating to determine moisture content. |
Trace Metal Analysis Preparation | Ashes organic materials, leaving inorganic components for metal analysis. |
Contamination-Free Heating | Sealed chamber prevents contamination from gases, ash, or residue. |
Versatility | Used for ash determination, heat treatment, and sample preparation. |
High-Temperature Capabilities | Reaches up to 1,800°C for advanced applications like metallurgical testing. |
Environmental & Industrial Research | Essential for soil health, contamination assessment, and quality control. |
Unlock the full potential of muffle furnaces for your research—contact our experts today to learn more!