A two-roll mill is a versatile piece of equipment widely used across various industries for mixing, kneading, and refining materials. It is particularly effective for processing polymers, rubber, plastics, and other materials into uniform and consistent mixtures. The machine is designed to handle a wide range of applications, including material development, quality control, and production processes. It is known for its durability, precision, and ability to maintain optimal temperature control, making it a cost-effective solution for industries requiring high-quality mixing and processing. Additionally, two-roll mills are used in educational settings for material testing and formulation experiments.
Key Points Explained:
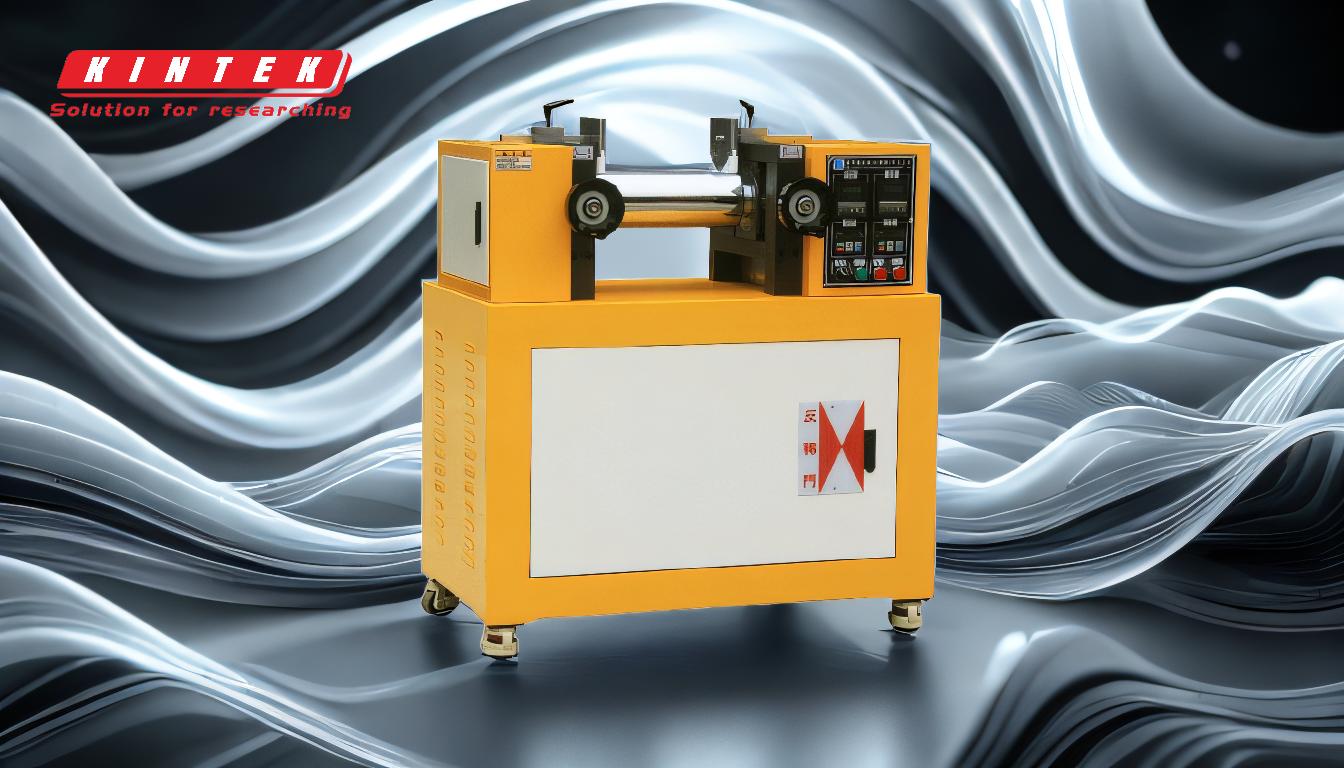
-
Primary Function: Mixing and Kneading
- The two-roll mill is primarily used for mixing and kneading raw materials such as rubber, synthetic rubber, thermoplastics, and EVA with chemicals.
- It ensures even distribution of additives, pigments, and other components, resulting in a homogeneous mixture.
- This process is critical in industries like polymer manufacturing, where consistency and uniformity are essential for product quality.
-
Wide Range of Applications
- Polymers and Plastics: Used for processing materials like LDPE, HDPE, PP, PVC, PS, ABS, HIPS, and natural rubber.
- Food and Cosmetics: Suitable for mixing food products, cosmetics, and other consumable goods.
- Chemicals and Pharmaceuticals: Utilized in the production of chemicals, pharmaceuticals, and adhesives.
- Paints and Pigments: Effective for mixing paints, pigments, and coatings.
- Advanced Materials: Used in the production of high-performance ceramics, electronic inks, and cable covers.
-
Temperature Control and Cooling
- The two-roll mill is designed to maintain optimal temperature control during the mixing process, which is crucial for heat-sensitive materials.
- Cooling effects ensure that materials do not degrade or lose their properties during processing.
- This feature makes it suitable for applications requiring precise thermal management.
-
Cost-Effectiveness and Durability
- The equipment is built to reduce production costs by minimizing maintenance requirements and ensuring long-term durability.
- Its customizable design allows it to adapt to specific industry needs, further enhancing its cost-effectiveness.
-
Material Development and Testing
- Two-roll mills are extensively used in material development, testing, and quality control processes.
- They enable researchers and manufacturers to experiment with formulations, test material properties, and ensure compliance with quality standards.
- Educational institutions also use these mills for teaching and research purposes.
-
Versatility Across Industries
- The two-roll mill is a multi-industry tool, serving sectors such as polymer manufacturing, food processing, pharmaceuticals, electronics, and more.
- Its ability to handle diverse materials and applications makes it an indispensable asset in modern industrial operations.
-
Precision and Consistency
- The machine is designed to deliver precision and consistency in mixing, ensuring high-quality end products.
- This reliability helps businesses improve their operations, meet industry standards, and achieve their production goals.
In summary, the two-roll mill is a highly efficient and adaptable piece of equipment that plays a critical role in material processing across various industries. Its ability to mix, knead, and refine materials with precision and consistency makes it a valuable tool for production, testing, and research purposes.
Summary Table:
Key Feature | Description |
---|---|
Primary Function | Mixing and kneading raw materials like rubber, plastics, and polymers. |
Applications | Polymers, food, cosmetics, chemicals, paints, and advanced materials. |
Temperature Control | Ensures optimal thermal management for heat-sensitive materials. |
Durability | Built for long-term use with minimal maintenance. |
Versatility | Suitable for multiple industries, including polymer manufacturing and research. |
Precision | Delivers consistent and high-quality mixing results. |
Ready to enhance your material processing? Contact us today to learn more about our laboratory mill and rubber calender solutions!