The vacuum arc remelting (VAR) process is a specialized technique used to refine and improve the quality of metals and alloys, particularly those used in critical applications like aerospace, medical implants, and power generation. This process involves melting a consumable electrode under vacuum conditions using an electric arc, which allows for precise control over the material's composition and microstructure. The result is a high-purity, homogeneous ingot with fewer defects and superior mechanical properties. Below, we explore the key aspects of the VAR process, its steps, and its significance in advanced metallurgy.
Key Points Explained:
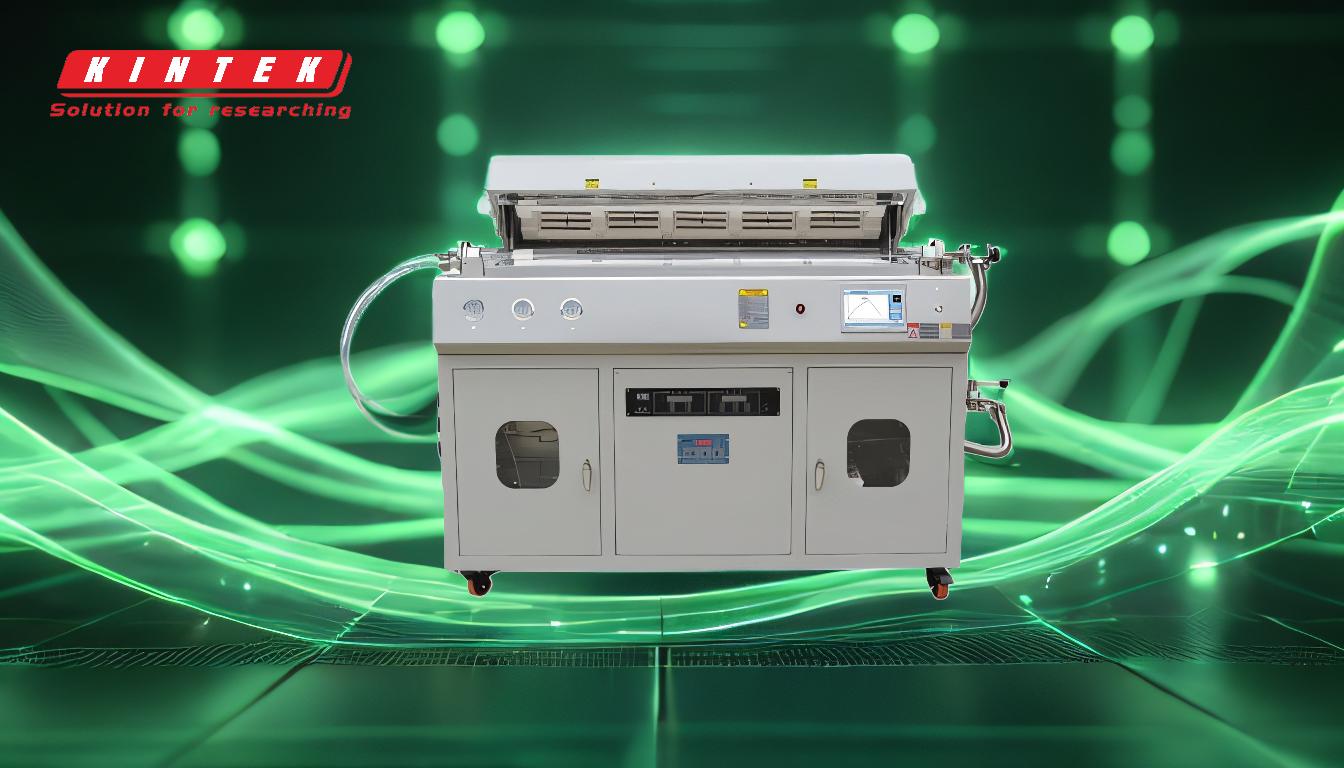
-
Purpose of Vacuum Arc Remelting:
- The primary goal of the VAR process is to produce high-quality metal ingots with minimal impurities and a uniform microstructure. This is achieved by melting and solidifying the metal under controlled vacuum conditions, which prevents contamination from atmospheric gases like oxygen and nitrogen.
-
Key Components of the Process:
- Vacuum Arc Furnace: The core equipment used in the VAR process. It consists of a vacuum chamber, a consumable electrode, a water-cooled copper mold, and an electric arc system. The vacuum environment ensures that the metal is melted and solidified without exposure to air.
- Consumable Electrode: The starting material, typically a pre-melted alloy, is shaped into an electrode. This electrode is gradually melted during the process.
- Water-Cooled Copper Mold: The molten metal solidifies in this mold, forming a high-quality ingot with a fine-grained structure.
-
Steps in the Vacuum Arc Remelting Process:
- Loading the Furnace: The consumable electrode is loaded into the vacuum chamber, and the chamber is sealed to create an airtight environment.
- Creating a Vacuum: A vacuum pump removes all air and gases from the chamber, ensuring that the melting process occurs in a contamination-free environment.
- Generating the Electric Arc: An electric arc is struck between the consumable electrode and the base of the copper mold. The intense heat of the arc melts the electrode, and the molten metal drips into the mold.
- Controlled Solidification: The molten metal solidifies in the water-cooled mold, forming a dense, homogeneous ingot. The process allows for precise control over the cooling rate, which influences the final microstructure of the metal.
- Cooling and Finishing: After solidification, the ingot is cooled further, often using inert gases like argon to prevent oxidation. The furnace is then opened, and the ingot is removed for further processing.
-
Advantages of the VAR Process:
- High Purity: The vacuum environment eliminates contamination from atmospheric gases, resulting in a metal with fewer inclusions and impurities.
- Improved Microstructure: The controlled melting and solidification process produces a fine-grained, homogeneous structure, enhancing the material's mechanical properties.
- Versatility: The VAR process is suitable for a wide range of metals and alloys, including titanium, nickel-based superalloys, and specialty steels.
-
Applications of Vacuum Arc Remelting:
- Aerospace: VAR-processed alloys are used in critical components like turbine blades and engine parts, where high strength and resistance to fatigue are essential.
- Medical Implants: The high purity and biocompatibility of VAR-processed metals make them ideal for surgical implants and prosthetics.
- Power Generation: Alloys produced through VAR are used in nuclear reactors and other high-temperature applications due to their superior performance under extreme conditions.
-
Maintenance and Cleaning:
- After each cycle, the vacuum arc furnace is thoroughly cleaned to remove any residual soot, grit, or splash metal. The copper mold is cleaned and reinstalled, and the furnace is prepared for the next operation. This ensures consistent performance and prolongs the lifespan of the equipment.
By leveraging the vacuum arc remelting process, manufacturers can produce metals and alloys with exceptional quality and performance, meeting the stringent demands of modern industries. The use of a vacuum arc furnace is central to this process, enabling precise control over the melting and solidification stages to achieve the desired material properties.
Summary Table:
Aspect | Details |
---|---|
Purpose | Produces high-quality metal ingots with minimal impurities and uniform microstructure. |
Key Components | Vacuum arc furnace, consumable electrode, water-cooled copper mold. |
Steps | Loading, vacuum creation, electric arc generation, controlled solidification, cooling. |
Advantages | High purity, improved microstructure, versatility for various metals. |
Applications | Aerospace, medical implants, power generation. |
Maintenance | Thorough cleaning after each cycle to ensure consistent performance. |
Interested in enhancing your metal production? Contact us today to learn more about the VAR process!