Vacuum brazing is a specialized welding technique performed in a vacuum environment, utilizing high temperatures and low air pressure to join metal components. This method ensures a clean, oxidation-free environment, which is crucial for achieving strong, high-quality bonds. The process involves melting a filler material that flows into the joint through capillary action, bonding the base materials without the need for additional fluxes. Vacuum brazing is widely used in industries requiring precision and reliability, such as aerospace, medical devices, and thermal management systems. The key equipment for this process is the vacuum brazing furnace, which provides the controlled environment and heating necessary for successful brazing.
Key Points Explained:
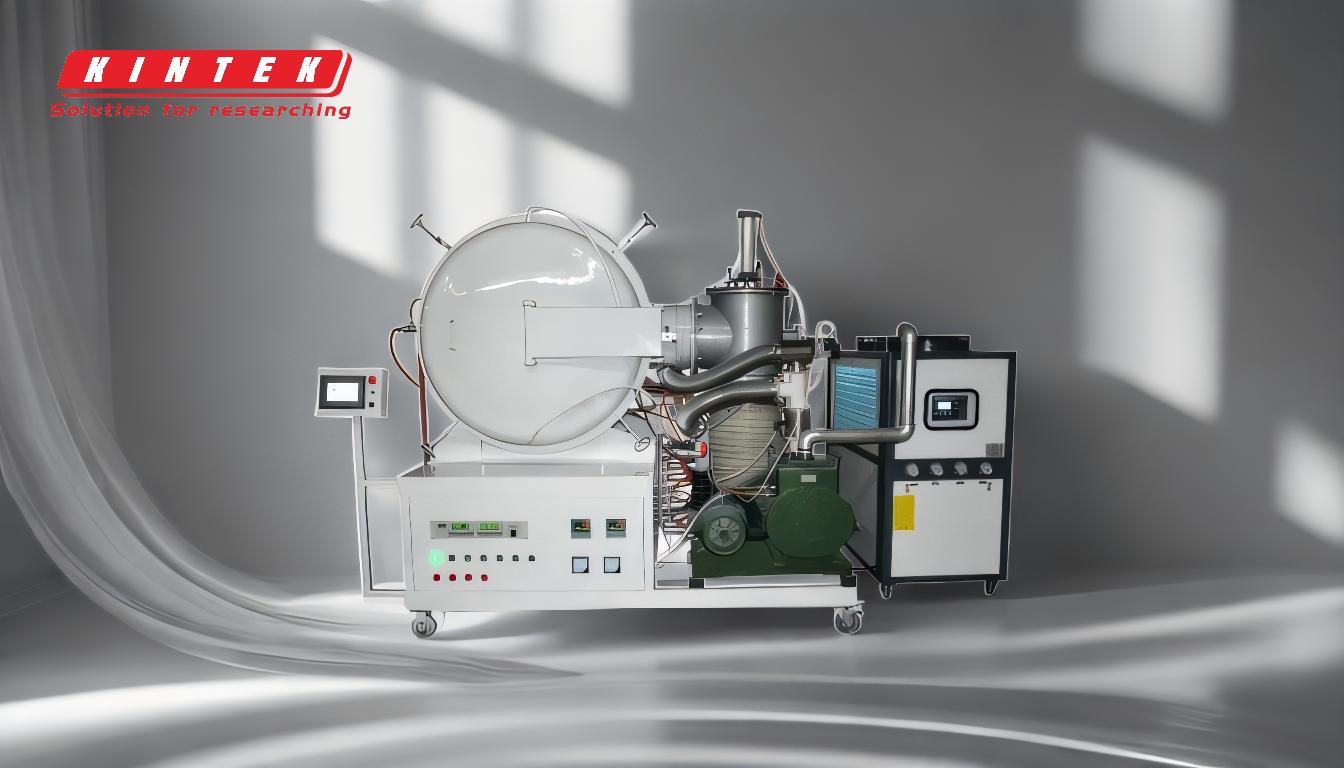
-
Definition and Principle of Vacuum Brazing:
- Vacuum brazing is a welding technique that joins metal components in a vacuum environment using high temperatures and a filler material.
- The process relies on capillary action, where the melted filler material flows into the joint, bonding the base materials without oxidation or contamination.
- The vacuum environment eliminates the need for fluxes, ensuring a clean and strong bond.
-
Applications of Vacuum Brazing:
- This technique is widely used in industries requiring high precision and reliability, such as:
- Aerospace: Joining aircraft components and structural parts.
- Medical Devices: Creating sensors and implants with high integrity.
- Thermal Management: Producing micro-channel heat exchangers and heating/cooling assemblies.
- The ability to join dissimilar metals and complex geometries makes it ideal for advanced engineering applications.
- This technique is widely used in industries requiring high precision and reliability, such as:
-
Working Principle of Vacuum Brazing:
- The process begins by placing the assembled workpiece into the vacuum brazing furnace.
- A vacuum system evacuates the chamber to a high vacuum level (typically 10^-3 Pa or lower).
- The heating system raises the temperature to melt the filler material, which then flows into the joint.
- After brazing, the workpiece is cooled in a controlled manner to prevent oxidation and ensure a high-quality joint.
-
Components of a Vacuum Brazing Furnace:
- Vacuum System: Includes mechanical pumps, diffusion pumps, and vacuum valves to achieve and maintain the required vacuum level.
- Heating System: Provides the high temperatures needed to melt the filler material.
- Control System: Automates the process, ensuring precise temperature and vacuum control for consistent results.
-
Advantages of Vacuum Brazing:
- Clean Joints: The absence of oxygen prevents oxidation, resulting in clean and strong bonds.
- Versatility: Suitable for joining dissimilar metals and complex geometries.
- High Precision: Ideal for applications requiring tight tolerances and high reliability.
- No Flux Required: Eliminates the need for post-brazing cleaning, reducing time and cost.
-
Comparison with Other Techniques:
- Vacuum Brazing vs. Vacuum Welding: While both processes occur in a vacuum, vacuum welding joins materials without filler metals, whereas vacuum brazing uses a filler material.
- Vacuum Brazing vs. Vacuum Sintering: Vacuum sintering compacts materials at high temperatures, creating new materials, while vacuum brazing joins existing materials.
- Vacuum Brazing vs. Vacuum Drying: Vacuum drying removes moisture under low pressure, whereas vacuum brazing focuses on joining metals.
-
Process Steps in Vacuum Brazing:
- Assembly: Place the workpiece and filler material in the furnace.
- Evacuation: Use the vacuum system to remove air from the chamber.
- Heating: Raise the temperature to melt the filler material.
- Brazing: Allow the filler material to flow into the joint.
- Cooling: Gradually cool the workpiece to prevent oxidation.
-
Industries Benefiting from Vacuum Brazing:
- Aerospace: Joining lightweight and durable components.
- Medical: Creating biocompatible and corrosion-resistant devices.
- Thermal Management: Producing efficient heat exchangers and cooling systems.
- Automotive: Developing high-performance engine and exhaust components.
In conclusion, vacuum brazing is a highly effective technique for joining metals in a clean, controlled environment. The vacuum brazing furnace plays a critical role in ensuring the success of this process, making it indispensable in industries where precision and reliability are paramount.
Summary Table:
Aspect | Details |
---|---|
Definition | Joins metal components in a vacuum using high temperatures and filler material. |
Key Principle | Capillary action ensures clean, oxidation-free bonds without fluxes. |
Applications | Aerospace, medical devices, thermal management, automotive. |
Advantages | Clean joints, versatility, high precision, no flux required. |
Equipment | Vacuum brazing furnace with vacuum, heating, and control systems. |
Process Steps | Assembly, evacuation, heating, brazing, cooling. |
Ready to enhance your metal joining process? Contact us today to learn more about vacuum brazing solutions!