Vacuum deposition is a sophisticated technique used to deposit thin layers of material onto a substrate in a controlled vacuum environment. This process is essential in industries requiring precise, high-quality coatings, such as electronics, optics, and renewable energy. It involves depositing materials atom-by-atom or molecule-by-molecule, enabling the creation of ultra-thin films with specific properties like conductivity, corrosion resistance, or optical enhancement. The technique is versatile, environmentally friendly, and continually evolving to meet the demands of advanced applications, including flexible displays, solar cells, and wear-resistant coatings.
Key Points Explained:
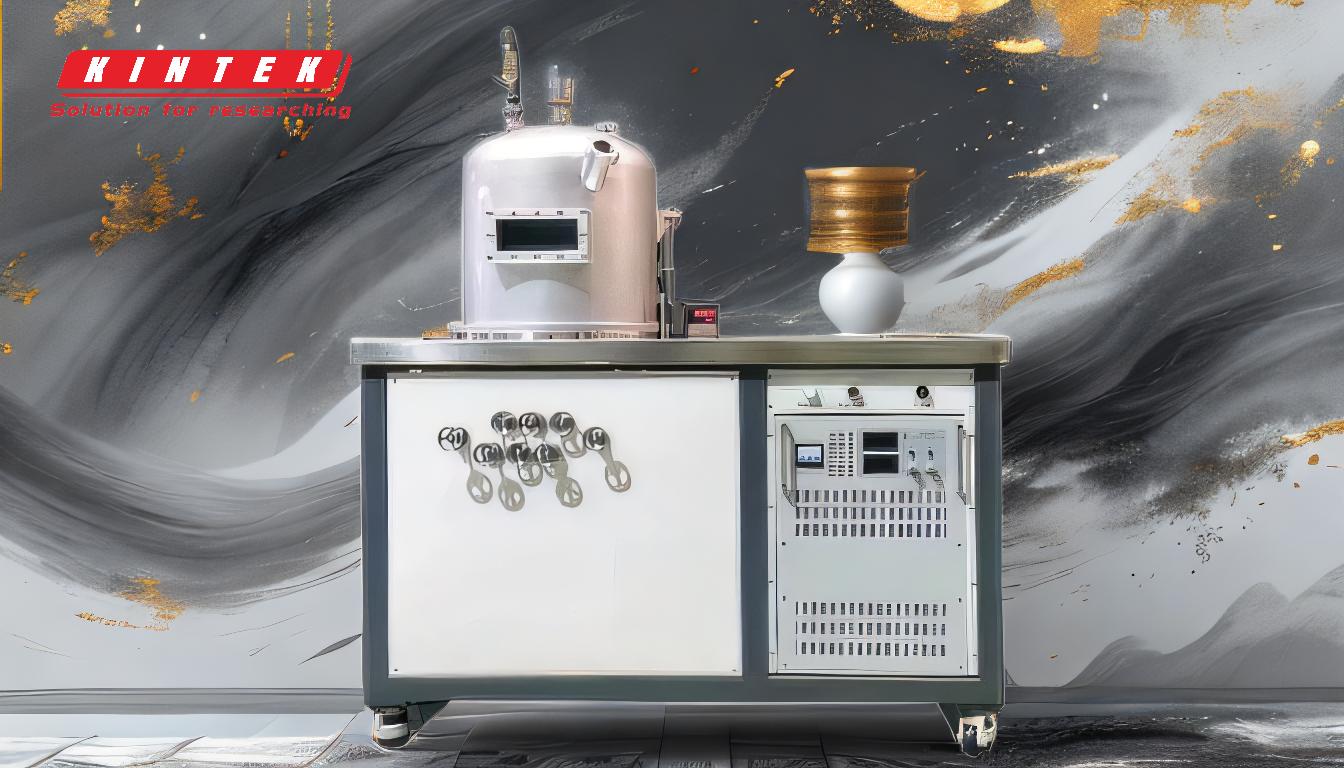
-
Definition and Process of Vacuum Deposition:
- Vacuum deposition refers to a group of processes where materials are deposited onto a substrate in a vacuum or low-pressure environment. This ensures minimal interference from gas molecules, allowing for precise control over the coating's thickness and properties.
- The process involves depositing materials atom-by-atom or molecule-by-molecule, enabling the creation of ultra-thin films, often in the nanometer range.
-
Types of Vacuum Deposition Techniques:
- Physical Vapor Deposition (PVD): A common method where the material is vaporized in a vacuum and then condensed onto the substrate. Examples include sputtering and evaporation.
- Low-Pressure Chemical Vapor Deposition (LPCVD): Involves chemical reactions at low pressures to deposit thin films. This method is often used in semiconductor manufacturing.
-
Applications of Vacuum Deposition:
- Electronics: Used in the production of microchips, LEDs, and thin-film transistors for flexible displays and sensors.
- Optics: Forms optical interference coatings, mirror coatings, and decorative coatings.
- Renewable Energy: Enhances the efficiency and durability of thin-film solar cells by improving conductivity and light harvesting properties.
- Corrosion Protection: Provides wear-resistant and corrosion-resistant coatings, often replacing traditional methods like electroplating.
-
Advantages of Vacuum Deposition:
- Precision: Allows for the deposition of extremely thin and uniform layers, often at the atomic or molecular level.
- Versatility: Suitable for a wide range of materials and applications, from electronics to automotive coatings.
- Environmental Benefits: Considered a "dry process," it reduces the need for hazardous chemicals and is more environmentally friendly compared to traditional coating methods.
-
Emerging Trends and Future Applications:
- Flexible Packaging: Development of clear permeation barrier layers for polymer webs and three-dimensional containers.
- Advanced Coatings: Creation of coatings to replace electroplated chromium and cadmium, driven by environmental concerns.
- Innovative Materials: Continued evolution of processes and equipment to meet the demands of new markets and applications, such as flexible electronics and advanced energy systems.
-
Key Considerations for Equipment and Consumable Purchasers:
- Process Compatibility: Ensure the vacuum deposition equipment is compatible with the specific materials and substrates used in your application.
- Environmental Impact: Consider the environmental benefits of vacuum deposition processes, especially when replacing traditional methods.
- Cost Efficiency: Evaluate the long-term cost savings from reduced material waste and improved product performance.
- Innovation and Upgradability: Look for systems that can be upgraded or adapted to new technologies and materials as they emerge.
By understanding these key points, purchasers can make informed decisions about vacuum deposition equipment and consumables, ensuring they meet the specific needs of their applications while staying ahead of industry trends.
Summary Table:
Aspect | Details |
---|---|
Definition | Depositing thin layers of material in a vacuum environment. |
Techniques | PVD (sputtering, evaporation), LPCVD. |
Applications | Electronics (microchips, LEDs), optics (mirrors), renewable energy (solar). |
Advantages | Precision, versatility, environmental benefits. |
Future Trends | Flexible packaging, advanced coatings, innovative materials. |
Purchasing Tips | Process compatibility, environmental impact, cost efficiency, upgradability. |
Ready to enhance your applications with vacuum deposition? Contact our experts today for tailored solutions!