Vapor phase deposition techniques, such as chemical vapor deposition (CVD), are advanced manufacturing processes used to deposit thin films or coatings onto substrates in a controlled environment. These techniques involve the use of gaseous precursors that chemically react or decompose on the substrate surface, forming a solid material layer. CVD, in particular, is widely used in industries like semiconductor manufacturing due to its ability to produce high-purity, uniform, and scalable coatings. Other vapor phase methods, such as sputtering and thermal vapor deposition, also play significant roles in material deposition, each with unique mechanisms and applications. These techniques are essential for creating durable, high-performance materials used in electronics, optics, and other high-tech fields.
Key Points Explained:
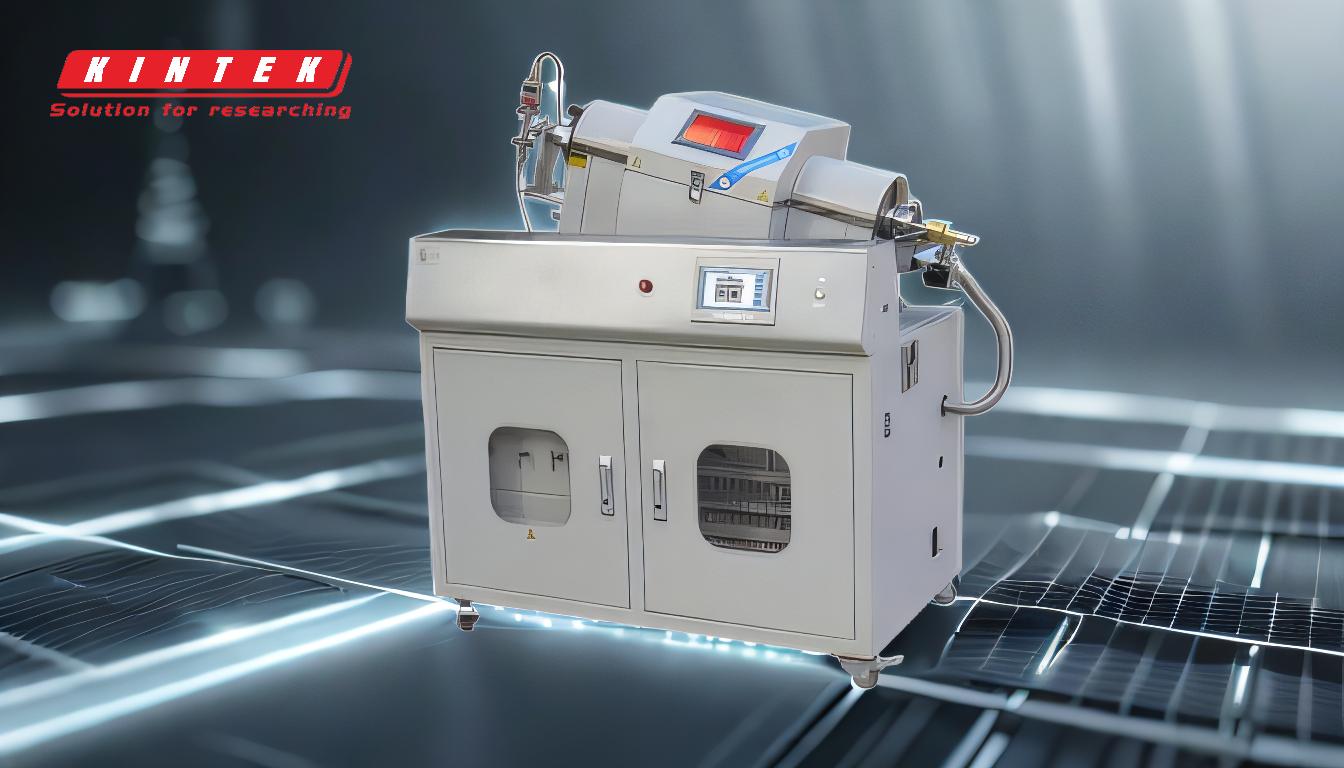
-
What is Vapor Phase Deposition?
- Vapor phase deposition refers to a group of techniques where materials are deposited onto a substrate in a gaseous or vapor state. These methods are performed in controlled environments, often under vacuum, to ensure precision and quality.
- The most common types of vapor phase deposition include chemical vapor deposition (CVD), sputtering, and thermal vapor deposition.
-
Chemical Vapor Deposition (CVD)
- Chemical vapor deposition (CVD) is a process where gaseous reactants are introduced into a chamber containing a substrate. These gases chemically react or decompose on the substrate surface, forming a solid material layer.
- CVD is widely used in the semiconductor industry to deposit thin films of materials like silicon, silicon dioxide, and various metals. It is valued for its ability to produce high-purity, uniform, and scalable coatings.
- Advantages of CVD include:
- High film purity and uniformity.
- Ability to deposit complex materials and alloys.
- Scalability for industrial production.
-
Sputtering Deposition
- Sputtering is another vapor phase deposition technique where atoms from a solid target material are ejected into a gas phase due to bombardment by high-energy ions. These atoms then deposit onto the substrate.
- This method is commonly used for depositing metals and alloys, as well as insulating materials like oxides and nitrides.
- Sputtering is particularly useful for applications requiring precise control over film thickness and composition.
-
Thermal Vapor Deposition
- Thermal vapor deposition involves heating a solid material in a high vacuum chamber to produce vapor pressure. The material transitions from a solid to a vapor state, which then condenses onto the substrate as a thin film.
- This technique is often used for depositing materials like metals, polymers, and organic compounds.
- It is particularly effective for creating coatings with specific thermal, optical, or mechanical properties.
-
Applications of Vapor Phase Deposition
- Semiconductor Manufacturing: CVD is extensively used to deposit thin films of silicon, silicon dioxide, and other materials essential for integrated circuits and microelectronics.
- Optics and Photonics: Vapor phase deposition techniques are used to create anti-reflective coatings, mirrors, and optical filters.
- Diamond Synthesis: Techniques like microwave plasma chemical vapor deposition (MPCVD) are used to produce high-quality synthetic diamonds for industrial and scientific applications.
- Protective Coatings: CVD and other methods are used to apply durable coatings that enhance substrate durability, reduce friction, and improve thermal properties.
-
Comparison of Vapor Phase Deposition Techniques
- CVD vs. Sputtering: CVD relies on chemical reactions, while sputtering involves physical ejection of atoms. CVD is better for producing complex materials, whereas sputtering offers better control over film thickness.
- CVD vs. Thermal Vapor Deposition: CVD is more versatile for depositing a wide range of materials, while thermal vapor deposition is simpler and more cost-effective for specific applications.
-
Future Trends and Innovations
- Advances in vapor phase deposition techniques are focused on improving efficiency, reducing costs, and expanding the range of materials that can be deposited.
- Emerging technologies like atomic layer deposition (ALD) and hybrid deposition methods are gaining traction for their ability to produce ultra-thin, highly uniform films.
By understanding these key points, equipment and consumable purchasers can make informed decisions about which vapor phase deposition techniques and chemical vapor deposition machines best suit their specific needs and applications.
Summary Table:
Technique | Mechanism | Applications |
---|---|---|
Chemical Vapor Deposition (CVD) | Gaseous reactants chemically react on the substrate surface. | Semiconductor manufacturing, high-purity coatings, complex material deposition. |
Sputtering | High-energy ions eject atoms from a target, depositing them onto the substrate. | Metals, alloys, insulating materials, precise film thickness control. |
Thermal Vapor Deposition | Solid material is heated to vaporize and condense onto the substrate. | Metals, polymers, organic compounds, thermal/optical coatings. |
Need help choosing the right vapor phase deposition technique? Contact our experts today!