The VAR (Vacuum Arc Remelting) process is a specialized metallurgical technique used to refine steel and other alloys, particularly for high-performance applications like aerospace, medical implants, and power generation. It involves melting a consumable electrode under vacuum conditions using an electric arc, which helps remove impurities, control the microstructure, and improve the material's homogeneity and mechanical properties. The process is critical for producing high-purity metals with superior strength, fatigue resistance, and consistency. VAR is often used in conjunction with other refining methods, such as ESR (Electroslag Remelting), to achieve the desired material properties for demanding applications.
Key Points Explained:
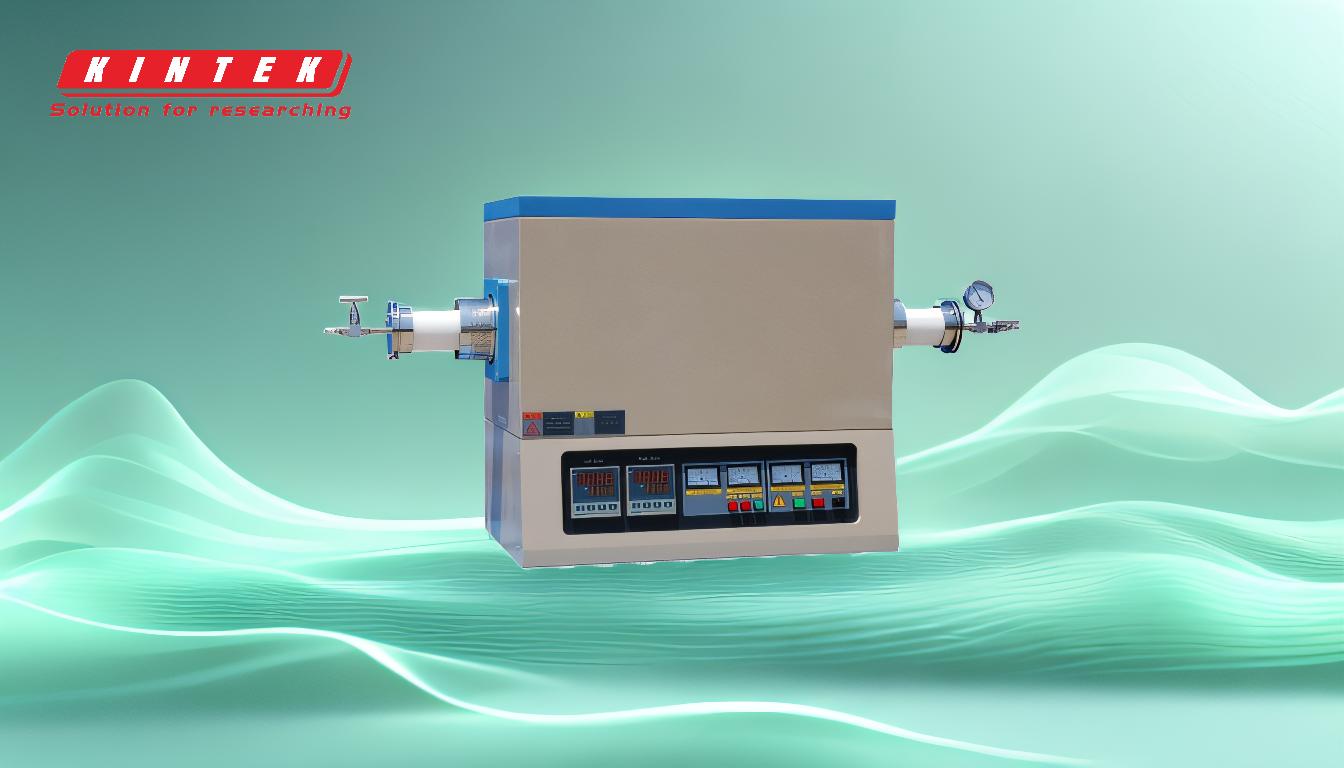
-
Purpose of the VAR Process:
- The VAR process is primarily used to refine steel and other alloys to achieve high levels of purity, homogeneity, and mechanical performance.
- It is especially important for applications where material integrity is critical, such as aerospace components, medical devices, and power generation equipment.
- The process helps eliminate impurities like gases (hydrogen, oxygen, nitrogen) and non-metallic inclusions, which can weaken the material.
-
How the VAR Process Works:
- Vacuum Environment: The process takes place in a vacuum chamber to prevent contamination and facilitate the removal of volatile impurities.
- Electric Arc Melting: A consumable electrode made of the alloy to be refined is melted using an electric arc. The arc generates intense heat, causing the electrode to melt drop by drop.
- Solidification: The molten metal solidifies in a water-cooled copper mold, forming a refined ingot. The controlled solidification process ensures a uniform microstructure and minimizes defects like segregation.
-
Key Advantages of VAR:
- Improved Purity: The vacuum environment and controlled melting process significantly reduce impurities, resulting in cleaner metal.
- Enhanced Mechanical Properties: VAR-refined steel exhibits superior strength, fatigue resistance, and toughness due to its refined microstructure.
- Consistency: The process ensures a high degree of homogeneity, which is crucial for critical applications.
-
Applications of VAR-Refined Steel:
- Aerospace: Components like turbine blades, landing gear, and engine parts require materials with exceptional strength and fatigue resistance.
- Medical Implants: VAR-refined alloys are used in surgical instruments and implants due to their biocompatibility and corrosion resistance.
- Power Generation: High-performance alloys for nuclear reactors and gas turbines benefit from the enhanced properties achieved through VAR.
-
Comparison with Other Refining Methods:
- Electroslag Remelting (ESR): While ESR also refines metals, it does so under a slag layer rather than a vacuum. ESR is often used before VAR to further improve material quality.
- Vacuum Induction Melting (VIM): VIM is another vacuum-based process, but it uses induction heating instead of an electric arc. VIM is typically used for initial melting before VAR.
-
Challenges and Considerations:
- Cost: The VAR process is expensive due to the specialized equipment and energy requirements.
- Complexity: Precise control of parameters like arc stability, vacuum level, and cooling rates is essential to achieve the desired material properties.
- Material Limitations: While VAR is highly effective for certain alloys, it may not be suitable for all materials.
In summary, the VAR process is a critical step in producing high-performance steel and alloys for demanding applications. Its ability to refine materials under vacuum conditions ensures superior purity, mechanical properties, and consistency, making it indispensable in industries where material performance is paramount.
Summary Table:
Aspect | Details |
---|---|
Purpose | Refines steel and alloys for high-purity, homogeneous, and strong materials. |
Process | Melts a consumable electrode under vacuum using an electric arc. |
Key Advantages | Improved purity, enhanced mechanical properties, and consistent quality. |
Applications | Aerospace, medical implants, and power generation. |
Comparison with ESR | ESR refines under slag; VAR uses vacuum for higher purity. |
Challenges | High cost, complexity, and material-specific limitations. |
Discover how the VAR process can elevate your material performance—contact our experts today!