RF sputtering is a widely used technique in thin film deposition, particularly for insulating materials, where DC sputtering is not feasible. The voltage required for RF sputtering is significantly higher than that of DC sputtering, typically starting at 1,012 volts or more, due to the nature of the process. RF sputtering operates at a frequency of 13.56 MHz, which is standard for industrial applications. The process involves using kinetic energy to remove electrons from gas atoms, creating a plasma that sputters target material onto a substrate. The voltage and frequency are critical parameters that influence the sputtering yield, deposition rate, and overall quality of the deposited film.
Key Points Explained:
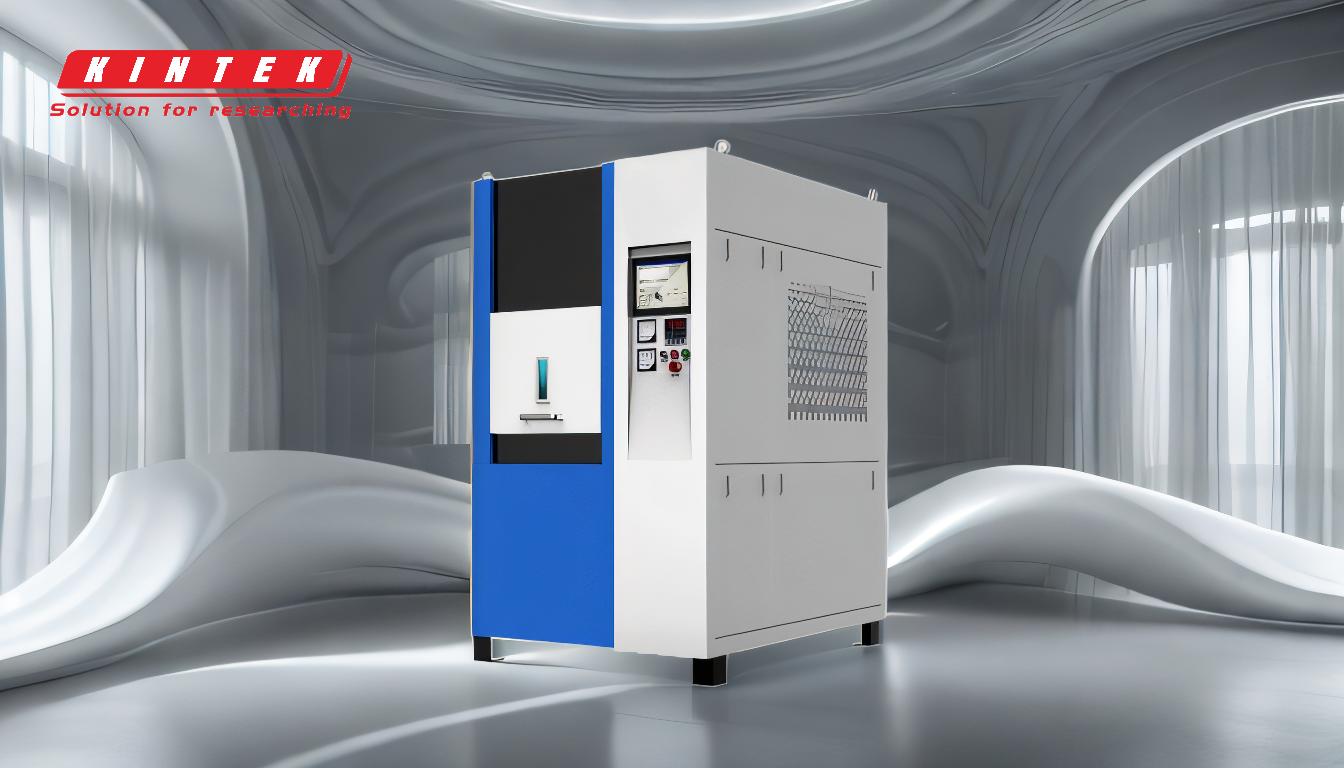
-
Voltage Requirements in RF Sputtering:
- RF sputtering requires a higher voltage compared to DC sputtering, typically starting at 1,012 volts or more. This is because RF sputtering relies on the kinetic energy of electrons to ionize gas atoms, rather than direct ion bombardment as in DC sputtering.
- The higher voltage is necessary to sustain the plasma and achieve a comparable deposition rate to DC sputtering.
-
Frequency of RF Sputtering:
- RF sputtering operates at a frequency of 13.56 MHz, which is a standard frequency allocated for industrial applications. This frequency is chosen because it effectively ionizes the gas and maintains a stable plasma.
- The use of 13.56 MHz ensures that the process is efficient and compatible with a wide range of materials, including insulators.
-
Factors Influencing Sputtering:
- The sputtering process is influenced by several factors, including the incident ion energy, the mass of the ions and target atoms, and the angle of incidence. These factors determine the sputtering yield, which is the number of target atoms ejected per incident ion.
- The sputtering yield varies depending on the target material and the specific sputtering conditions, such as chamber pressure and power applied to the target.
-
Role of Chamber Pressure and Kinetic Energy:
- Chamber pressure plays a significant role in the sputtering process, as it affects the coverage and uniformity of the deposited film. Higher pressure can improve coverage by increasing the number of collisions between particles.
- The kinetic energy of emitted particles determines their direction and deposition on the substrate. Precise control of this energy is crucial for achieving high-quality thin films.
-
Comparison with DC Sputtering:
- DC sputtering involves direct ion bombardment of the gas plasma by electrons, which allows for lower voltage requirements compared to RF sputtering. However, DC sputtering is limited to conductive materials.
- RF sputtering, on the other hand, can be used for both conductive and insulating materials, making it more versatile but requiring higher voltages to achieve similar deposition rates.
-
Impact of Power Source on Deposition:
- The type of power source (DC or RF) affects the deposition rate, material compatibility, and cost. RF sputtering is generally more expensive due to the higher voltage and frequency requirements.
- The excess energy of metal ions in RF sputtering can increase surface mobility, which can improve the quality of the deposited film by allowing atoms to find more stable positions on the substrate.
In summary, RF sputtering is a complex process that requires careful control of voltage, frequency, and other parameters to achieve high-quality thin film deposition. The higher voltage and specific frequency of 13.56 MHz are essential for maintaining the plasma and ensuring efficient sputtering of target materials, particularly insulators. Understanding the factors that influence the sputtering process is crucial for optimizing the deposition rate and film quality.
Summary Table:
Parameter | Details |
---|---|
Voltage | Starts at 1,012 volts or higher |
Frequency | 13.56 MHz (standard for industrial applications) |
Material Compatibility | Suitable for both conductive and insulating materials |
Key Advantages | High-quality thin films, uniform deposition, and versatility for insulators |
Comparison to DC Sputtering | Higher voltage but works with insulators; DC limited to conductors |
Ready to optimize your thin film deposition process? Contact us today to learn more about RF sputtering solutions!