Chemical Vapor Deposition (CVD) is a technique used to produce high-quality, high-performance solid materials, typically in thin films. The process involves the deposition of a material onto a substrate through chemical reactions in the vapor phase. CVD is widely used in the semiconductor industry, as well as in the production of coatings, fibers, and composite materials. The process can be broken down into several key steps: precursor delivery, chemical reaction, and deposition. The working of CVD involves the use of volatile precursors that are introduced into a reaction chamber, where they decompose or react on a heated substrate to form the desired material. The process is highly controllable, allowing for precise thickness and composition of the deposited material.
Key Points Explained:
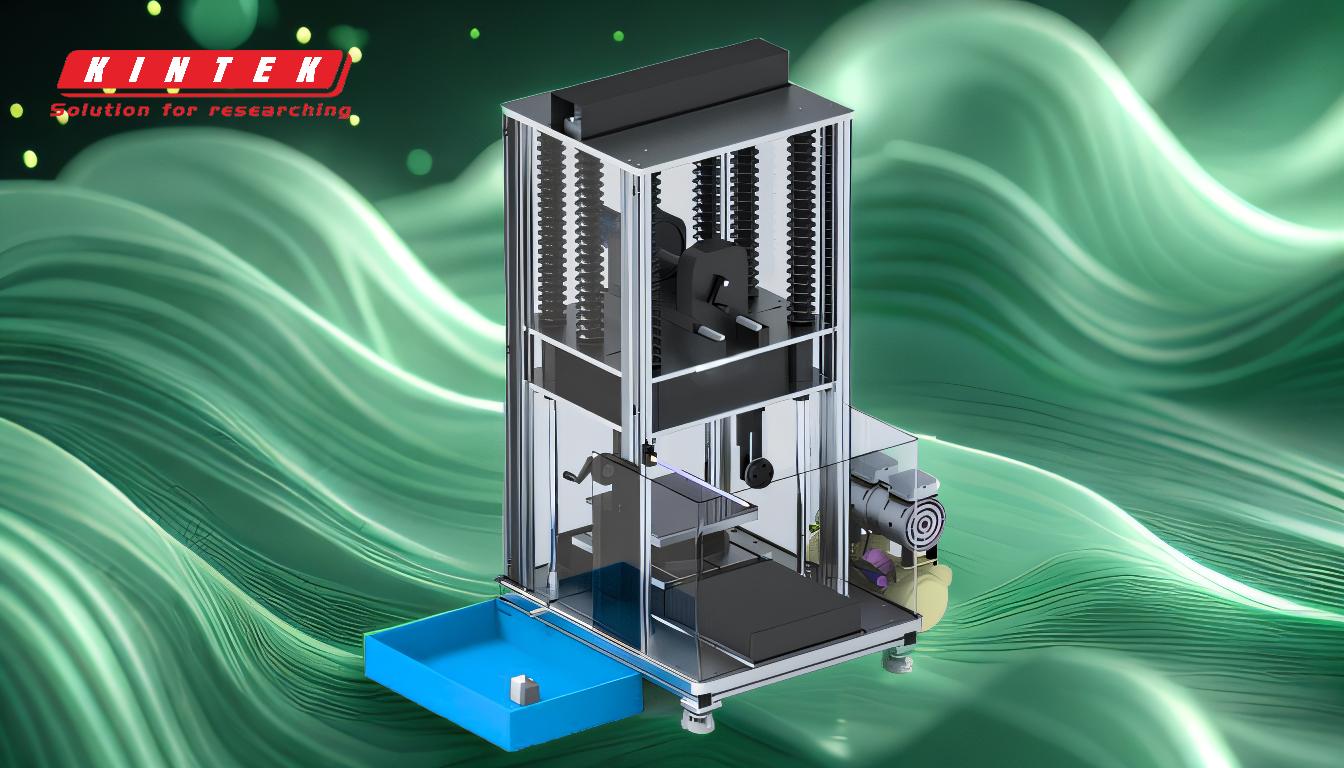
-
Precursor Delivery:
- In CVD, the process begins with the delivery of volatile precursors into the reaction chamber. These precursors are typically gases or vapors that contain the elements needed to form the desired material. The precursors are often mixed with carrier gases to facilitate their transport into the chamber.
- The choice of precursor is crucial, as it determines the chemical composition of the deposited material. Common precursors include metal halides, hydrides, and organometallic compounds.
-
Chemical Reaction:
- Once inside the reaction chamber, the precursors undergo chemical reactions. These reactions can be thermal, plasma-enhanced, or photo-induced, depending on the specific CVD technique being used.
- The reactions occur on the surface of a heated substrate, which is typically maintained at a temperature that promotes the decomposition or reaction of the precursors. The heat energy provided by the substrate drives the chemical reactions, leading to the formation of the desired material.
-
Deposition:
- The final step in the CVD process is the deposition of the material onto the substrate. As the precursors react, they form a solid material that adheres to the substrate surface. The deposition process is highly controlled, allowing for the formation of thin films with precise thickness and composition.
- The deposited material can be a single layer or multiple layers, depending on the desired properties of the final product. The process can also be used to create complex structures, such as nanowires or nanotubes, by controlling the reaction conditions.
-
Vacuum and Pressure Control:
- The CVD process often operates under reduced pressure or vacuum conditions. This is particularly important for processes like short path vacuum distillation, where the pressure is reduced to lower the boiling point of the materials being processed.
- In CVD, the vacuum helps to reduce contamination by removing unwanted gases and impurities from the reaction chamber. It also allows for better control over the deposition process, as the reduced pressure can influence the rate of chemical reactions and the uniformity of the deposited material.
-
Applications of CVD:
- CVD is used in a wide range of applications, from the production of semiconductor devices to the creation of protective coatings. In the semiconductor industry, CVD is used to deposit thin films of silicon, silicon dioxide, and other materials onto silicon wafers.
- The technique is also used in the production of optical fibers, where it is used to deposit layers of glass with different refractive indices. Additionally, CVD is used in the production of carbon nanotubes, graphene, and other advanced materials.
-
Advantages of CVD:
- One of the main advantages of CVD is its ability to produce high-quality, high-purity materials. The process allows for precise control over the composition and thickness of the deposited material, making it ideal for applications where these properties are critical.
- CVD is also a versatile technique, capable of depositing a wide range of materials, including metals, ceramics, and polymers. The process can be adapted to different substrates and can be used to create complex structures with high precision.
In summary, the working of the CVD technique involves the controlled delivery of volatile precursors into a reaction chamber, where they undergo chemical reactions on a heated substrate to form a solid material. The process is highly controllable and versatile, making it suitable for a wide range of applications in materials science and engineering.
Summary Table:
Key Aspect | Details |
---|---|
Precursor Delivery | Volatile precursors are delivered into the reaction chamber for deposition. |
Chemical Reaction | Precursors react on a heated substrate to form the desired material. |
Deposition | Solid material adheres to the substrate, forming precise thin films. |
Vacuum Control | Reduced pressure ensures purity and uniformity in the deposition process. |
Applications | Used in semiconductors, optical fibers, and advanced materials like graphene. |
Advantages | High-quality, high-purity materials with precise control over properties. |
Interested in leveraging CVD for your projects? Contact our experts today to learn more!