Thermal regeneration is a widely used method for restoring the adsorption capacity of granular activated carbon (GAC) that has become saturated with organic substances. This process involves heating the spent carbon to high temperatures (typically between 800-1000 °C) in a furnace, which oxidizes and removes the adsorbed organic compounds. The regenerated GAC can then be reused, making this method both cost-effective and environmentally sustainable. Below, we delve into the key aspects of thermal regeneration, its process, benefits, and considerations for equipment and consumables purchasers.
Key Points Explained:
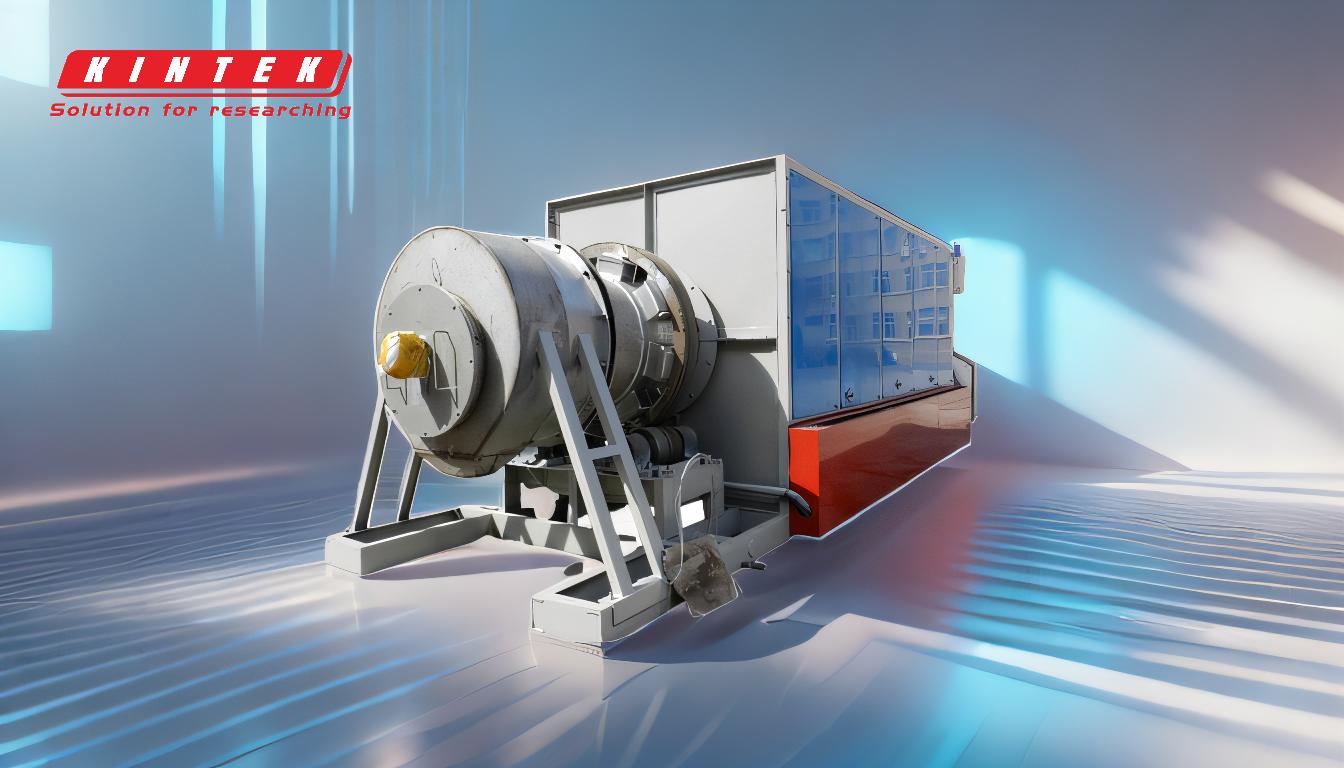
-
Definition and Purpose of Thermal Regeneration
- Thermal regeneration is a process designed to restore the adsorption capacity of granular activated carbon (GAC) by removing organic substances that have accumulated on its surface.
- The primary goal is to extend the lifespan of GAC, reducing the need for frequent replacement and lowering operational costs.
-
Process Overview
- Heating in a Furnace: Spent GAC is heated to temperatures between 800-1000 °C in a controlled environment, typically a rotary kiln or a multiple hearth furnace.
- Oxidation of Organic Substances: At these high temperatures, the organic compounds adsorbed onto the GAC are oxidized, breaking them down into simpler molecules such as carbon dioxide and water vapor.
- Reactivation of GAC: The heat also restores the porous structure of the carbon, ensuring its adsorption capacity is fully regained.
-
Equipment Required for Thermal Regeneration
- Furnaces: High-temperature furnaces, such as rotary kilns or multiple hearth furnaces, are essential for achieving the required temperatures.
- Gas Handling Systems: Systems to manage the off-gases produced during oxidation, including scrubbers and filters, are necessary to comply with environmental regulations.
- Cooling and Screening Equipment: After regeneration, the GAC must be cooled and screened to remove any fines or impurities before reuse.
-
Benefits of Thermal Regeneration
- Cost-Effectiveness: Reusing GAC reduces the need for purchasing new carbon, lowering material costs.
- Sustainability: By extending the life of GAC, thermal regeneration minimizes waste and supports environmental goals.
- Efficiency: Regenerated GAC often performs comparably to virgin carbon, ensuring consistent adsorption performance.
-
Considerations for Equipment and Consumables Purchasers
- Furnace Selection: Choose furnaces that can consistently achieve and maintain the required temperatures while ensuring energy efficiency.
- Compliance with Regulations: Ensure that gas handling systems are capable of meeting local emissions standards.
- Quality of Regenerated GAC: Verify that the regeneration process restores the GAC's adsorption capacity without damaging its structure.
- Operational Costs: Evaluate the energy consumption and maintenance requirements of the regeneration equipment to ensure long-term cost-effectiveness.
-
Challenges and Limitations
- Energy Consumption: The high temperatures required for thermal regeneration can lead to significant energy use, impacting operational costs.
- Carbon Loss: Some GAC may be lost during the regeneration process due to oxidation or mechanical degradation.
- Handling of Off-Gases: Proper treatment of off-gases is critical to prevent environmental contamination and ensure regulatory compliance.
By understanding the principles and practical aspects of thermal regeneration, equipment and consumables purchasers can make informed decisions that balance cost, performance, and sustainability. This method not only enhances the efficiency of GAC usage but also aligns with broader environmental and economic goals.
Summary Table:
Aspect | Details |
---|---|
Purpose | Restores adsorption capacity of GAC by removing organic substances. |
Process | Heating spent GAC to 800-1000 °C in furnaces to oxidize organics. |
Equipment | Rotary kilns, gas handling systems, cooling, and screening equipment. |
Benefits | Cost-effective, sustainable, and efficient regeneration of GAC. |
Challenges | High energy consumption, carbon loss, and off-gas handling requirements. |
Ready to optimize your GAC usage with thermal regeneration? Contact our experts today for tailored solutions!