Sintering temperature is a critical parameter in the sintering process, and determining what is "too high" depends on the material being sintered, the desired properties of the final product, and the specific sintering technique used. Excessive sintering temperatures can lead to issues such as increased costs, excessive shrinkage, material defects, and challenges in controlling the process. The optimal temperature must balance achieving the desired density and mechanical properties while avoiding these drawbacks. Key factors influencing sintering include material composition, particle size, heating rate, and atmospheric conditions. High temperatures can enhance properties like tensile strength and impact energy but must be carefully managed to prevent negative outcomes.
Key Points Explained:
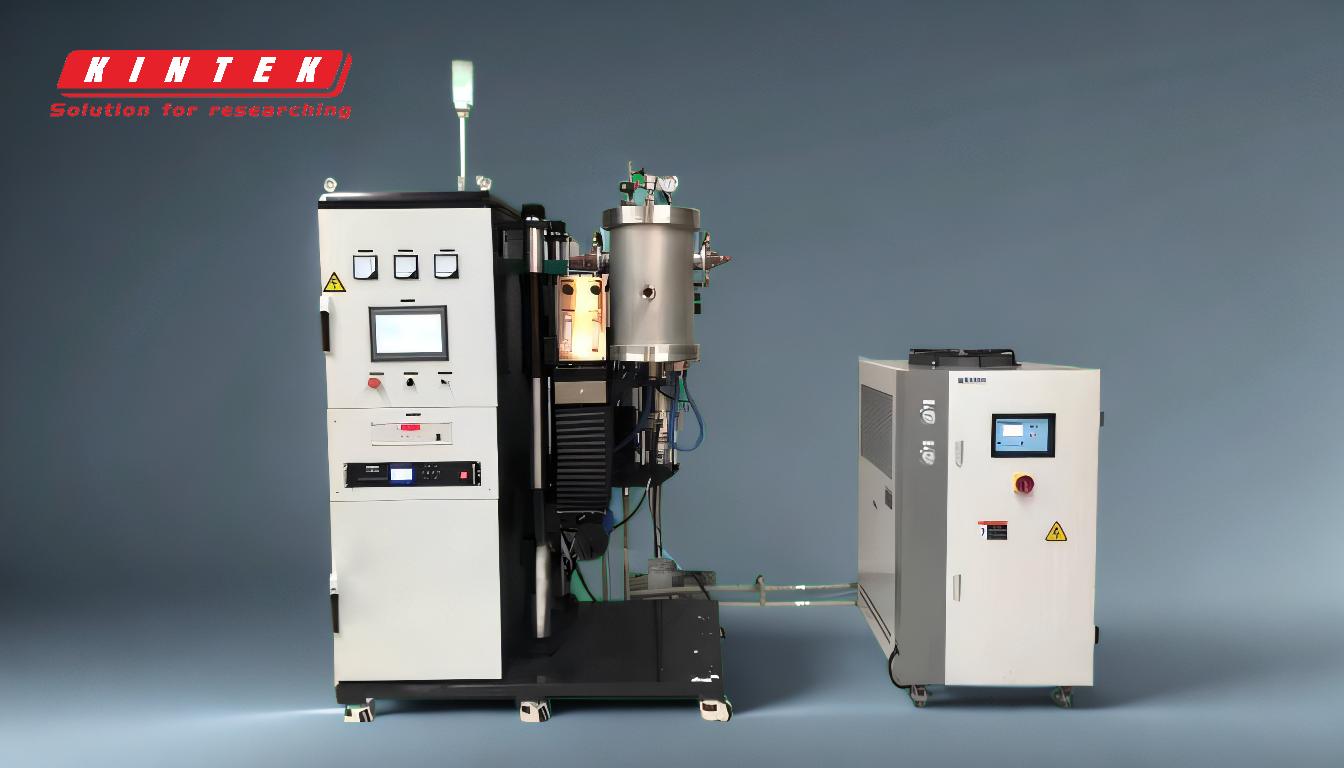
-
Material-Specific Sintering Temperatures:
- The sintering temperature must align with the material being processed. For example, metals, ceramics, and polymers each have distinct temperature ranges for effective sintering.
- Exceeding the material-specific optimal temperature can lead to undesirable outcomes such as excessive grain growth, melting, or phase transformations, which compromise the structural integrity of the final product.
-
Impact of High Temperatures on Costs:
- Higher sintering temperatures often require more advanced and expensive furnaces capable of withstanding extreme heat and maintaining precise atmospheric conditions.
- These increased costs are typically passed on to the customer, making high-temperature sintering less economically viable for some applications.
-
Shrinkage and Dimensional Control:
- High sintering temperatures can cause greater shrinkage in the final product, necessitating careful design adjustments to account for this during production.
- Excessive shrinkage can lead to dimensional inaccuracies, requiring additional post-sintering machining or rendering the part unusable.
-
Control of Liquid Phase and Densification:
- While finer powders and higher temperatures can enhance compaction and densification, the amount of liquid phase must be carefully controlled.
- Too much liquid phase can lead to uneven densification, warping, or other defects in the final product.
-
Atmospheric and Environmental Considerations:
- The sintering atmosphere (e.g., air, vacuum, or inert gases like argon or nitrogen) plays a crucial role in determining the optimal temperature.
- High temperatures in reactive atmospheres can lead to oxidation or other chemical reactions that degrade the material.
-
Mechanical Properties and Trade-Offs:
- High-temperature sintering can improve mechanical properties such as tensile strength, bending fatigue strength, and impact energy.
- However, these benefits must be weighed against the risks of material degradation, increased costs, and process complexity.
-
Process Control and Risks:
- Maintaining consistent sintering results at high temperatures requires precise control of parameters such as heating rate, cooling rate, and layer thickness.
- Risks include material defects, inconsistent sintering outcomes, and challenges in achieving the desired endpoint.
-
Alternative Techniques and Parameters:
- Different sintering techniques (e.g., pressure-assisted sintering, spark plasma sintering) may have varying temperature limits and requirements.
- Factors such as particle size, composition, and applied pressure can influence the optimal sintering temperature and mitigate the need for excessively high temperatures.
In summary, what constitutes "too high" for sintering temperature depends on a balance between achieving desired material properties and avoiding negative consequences such as increased costs, excessive shrinkage, and process control challenges. Careful consideration of material properties, sintering technique, and process parameters is essential to determine the optimal temperature range for a given application.
Summary Table:
Key Factor | Impact of High Sintering Temperatures |
---|---|
Material-Specific Temperatures | Excessive grain growth, melting, or phase transformations can compromise structural integrity. |
Costs | Advanced furnaces and precise atmospheric control increase expenses. |
Shrinkage | Greater shrinkage leads to dimensional inaccuracies, requiring post-sintering adjustments. |
Liquid Phase Control | Uneven densification and warping occur if liquid phase is not managed properly. |
Atmospheric Conditions | High temperatures in reactive atmospheres can cause oxidation or chemical degradation. |
Mechanical Properties | Improves tensile strength and impact energy but risks material degradation and process complexity. |
Process Control | Precise control of heating/cooling rates and layer thickness is essential to avoid defects. |
Alternative Techniques | Techniques like pressure-assisted sintering can reduce the need for excessively high temperatures. |
Need help determining the optimal sintering temperature for your materials? Contact our experts today for tailored solutions!