A two-roll differential speed mill is a specialized machine used primarily for processing high-viscosity materials, such as pastes, polymers, and rubber compounds. It consists of two rotating rollers that operate at different speeds, creating a shear force that helps in mixing, dispersing, and refining materials. The differential speed between the rollers is expressed as a ratio (e.g., 1.5:1), where one roller turns faster than the other. This design ensures efficient temperature control, uniform material processing, and consistent results. The rollers are typically made of corrosion-resistant steel, making them durable and suitable for high-temperature applications. This type of laboratory mill is widely used in industries requiring precise temperature regulation and high-quality dispersion.
Key Points Explained:
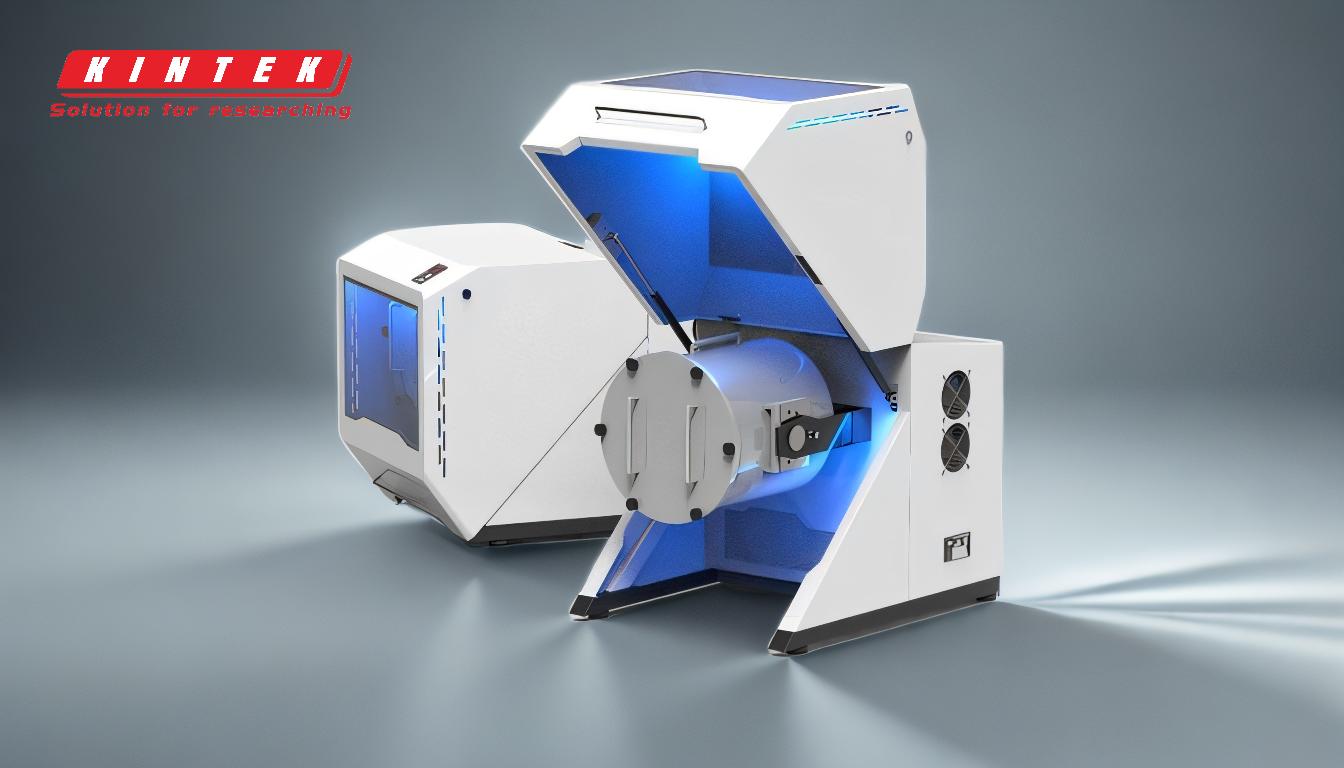
-
Definition and Functionality of a Two-Roll Differential Speed Mill:
- A two-roll differential speed mill is a machine designed for processing high-viscosity materials.
- It consists of two rollers rotating at different speeds, creating shear forces that aid in mixing, dispersing, and refining materials.
- The differential speed is expressed as a ratio (e.g., 1.5:1), where one roller turns faster than the other.
-
Differential Speed Mechanism:
- The speed difference between the rollers is crucial for generating shear forces, which are essential for material processing.
- For example, if the fast roller operates at 1,000 RPM with a 1.5:1 differential, the slow roller will turn at 667 RPM.
- This speed differential ensures efficient mixing and dispersion of materials.
-
Temperature Control and Cooling:
- The rollers are designed to maintain uniform temperatures, even during high-intensity dispersion work.
- Cooled rollers help in maintaining low temperatures, which is critical for processing heat-sensitive materials.
- This feature ensures consistent results and prevents material degradation due to overheating.
-
Material Suitability:
- Two-roll mills are ideal for processing high-viscosity pastes, polymers, and rubber compounds.
- The machine's design allows for the handling of materials that require precise temperature regulation and high shear forces.
-
Durability and Customization:
- The rollers are typically made of corrosion-resistant steel, making them durable and suitable for high-temperature applications.
- The machine is customizable to meet specific production needs, ensuring flexibility in various industrial applications.
-
Cost Efficiency and Maintenance:
- Two-roll mills are designed to reduce production costs by ensuring minimal maintenance requirements.
- The durable construction and efficient cooling mechanisms contribute to lower operational costs over time.
-
Applications in Industry:
- Two-roll differential speed mills are widely used in industries such as rubber manufacturing, polymer processing, and chemical production.
- They are particularly valued for their ability to produce consistent, high-quality results in applications requiring precise temperature control and material dispersion.
By understanding these key points, equipment and consumable purchasers can make informed decisions about the suitability of a two-roll differential speed mill for their specific needs, ensuring optimal performance and cost efficiency in their production processes.
Summary Table:
Feature | Description |
---|---|
Functionality | Processes high-viscosity materials like pastes, polymers, and rubber compounds. |
Differential Speed | Rollers operate at different speeds (e.g., 1.5:1 ratio) for efficient mixing. |
Temperature Control | Cooled rollers maintain uniform temperatures, ideal for heat-sensitive materials. |
Material Suitability | Ideal for high-viscosity materials requiring precise temperature regulation. |
Durability | Rollers made of corrosion-resistant steel for high-temperature applications. |
Applications | Used in rubber manufacturing, polymer processing, and chemical production. |
Enhance your material processing with a two-roll differential speed mill—contact us today to learn more!