Uniaxial pressing is a widely used manufacturing process in which a powder material is compacted into a desired shape by applying pressure along a single axis. This method is commonly employed in the production of ceramic components, metal parts, and other materials where high density and precise shapes are required. The process involves filling a die with powder, applying pressure through a punch, and then ejecting the compacted part. Uniaxial pressing is favored for its simplicity, cost-effectiveness, and ability to produce parts with consistent dimensions and properties. It is particularly useful in industries such as electronics, automotive, and aerospace, where precision and reliability are critical.
Key Points Explained:
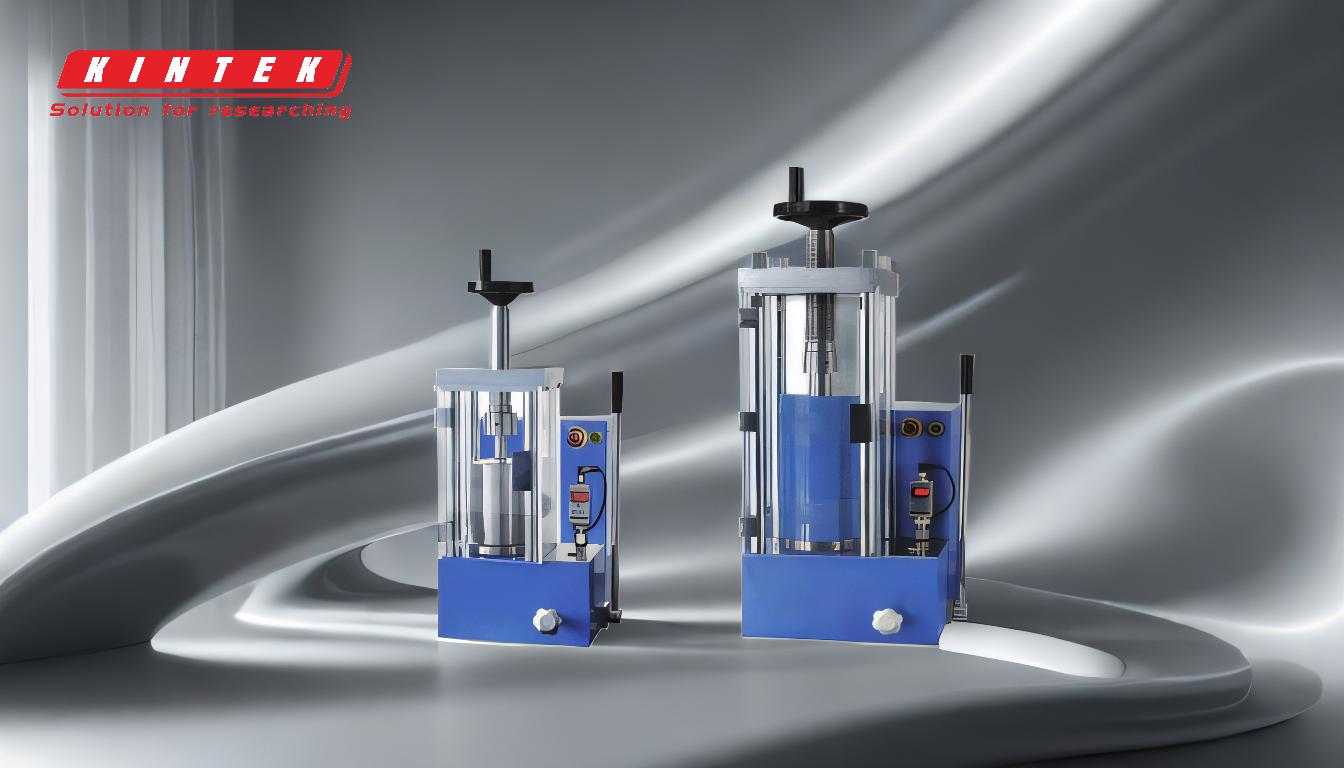
-
Definition and Process of Uniaxial Pressing:
- Uniaxial pressing is a powder compaction technique where pressure is applied along a single axis to form a solid part from powdered material.
- The process typically involves the following steps:
- Filling a die cavity with the powder material.
- Applying pressure using a punch to compact the powder.
- Ejecting the compacted part from the die.
- This method is often used for producing simple shapes such as cylinders, rectangles, or discs.
-
Advantages of Uniaxial Pressing:
- Cost-Effectiveness: Uniaxial pressing is relatively inexpensive compared to other compaction methods like isostatic pressing.
- Simplicity: The process is straightforward and requires minimal equipment, making it accessible for small-scale and large-scale production.
- Consistency: It produces parts with uniform density and dimensions, which is crucial for applications requiring precision.
- High Production Rates: The process can be automated, allowing for the rapid production of parts.
-
Applications of Uniaxial Pressing:
- Ceramics: Used to manufacture ceramic components such as insulators, substrates, and cutting tools.
- Metals: Applied in the production of metal parts like gears, bearings, and structural components.
- Advanced Materials: Utilized for creating components from advanced materials such as composites and nanomaterials.
- Electronics: Commonly used to produce components like capacitors, resistors, and magnetic cores.
-
Limitations of Uniaxial Pressing:
- Shape Complexity: The method is limited to relatively simple shapes due to the unidirectional application of pressure.
- Density Variations: Parts may have density gradients, especially in complex geometries, which can affect mechanical properties.
- Tooling Wear: The dies and punches are subject to wear and tear, requiring regular maintenance or replacement.
-
Comparison with Other Compaction Methods:
- Isostatic Pressing: Unlike uniaxial pressing, isostatic pressing applies pressure uniformly from all directions, allowing for more complex shapes and uniform density. However, it is more expensive and time-consuming.
- Injection Molding: This method is better suited for producing highly complex shapes but involves higher costs and longer cycle times compared to uniaxial pressing.
-
Key Considerations for Equipment and Consumables:
- Die Design: The die must be designed to withstand high pressures and ensure consistent compaction.
- Punch Material: Punches should be made from durable materials to minimize wear and maintain precision.
- Powder Characteristics: The particle size, distribution, and flowability of the powder are critical for achieving uniform compaction.
- Lubrication: Proper lubrication of the die and punch is essential to reduce friction and prevent sticking.
By understanding these key points, purchasers of equipment and consumables can make informed decisions when selecting tools and materials for uniaxial pressing processes. This ensures optimal performance, cost-efficiency, and high-quality output in their manufacturing operations.
Summary Table:
Aspect | Details |
---|---|
Process | Pressure applied along a single axis to compact powder into a solid shape. |
Advantages | Cost-effective, simple, consistent dimensions, high production rates. |
Applications | Ceramics, metals, advanced materials, electronics. |
Limitations | Limited to simple shapes, density variations, tooling wear. |
Key Considerations | Die design, punch material, powder characteristics, lubrication. |
Discover how uniaxial pressing can optimize your manufacturing process—contact our experts today!