Vacuum annealing is a heat treatment process performed in a vacuum environment to alter the physical and sometimes chemical properties of a material. This process involves heating the material above its recrystallization temperature in a vacuum furnace, which prevents oxidation and contamination by gases like carbon and oxygen. The key benefits include uniform temperature distribution, precise temperature control, low contamination, rapid cooling, and computer-controlled processes for repeatability. Vacuum annealing is particularly useful for materials that require high purity and specific metallurgical properties.
Key Points Explained:
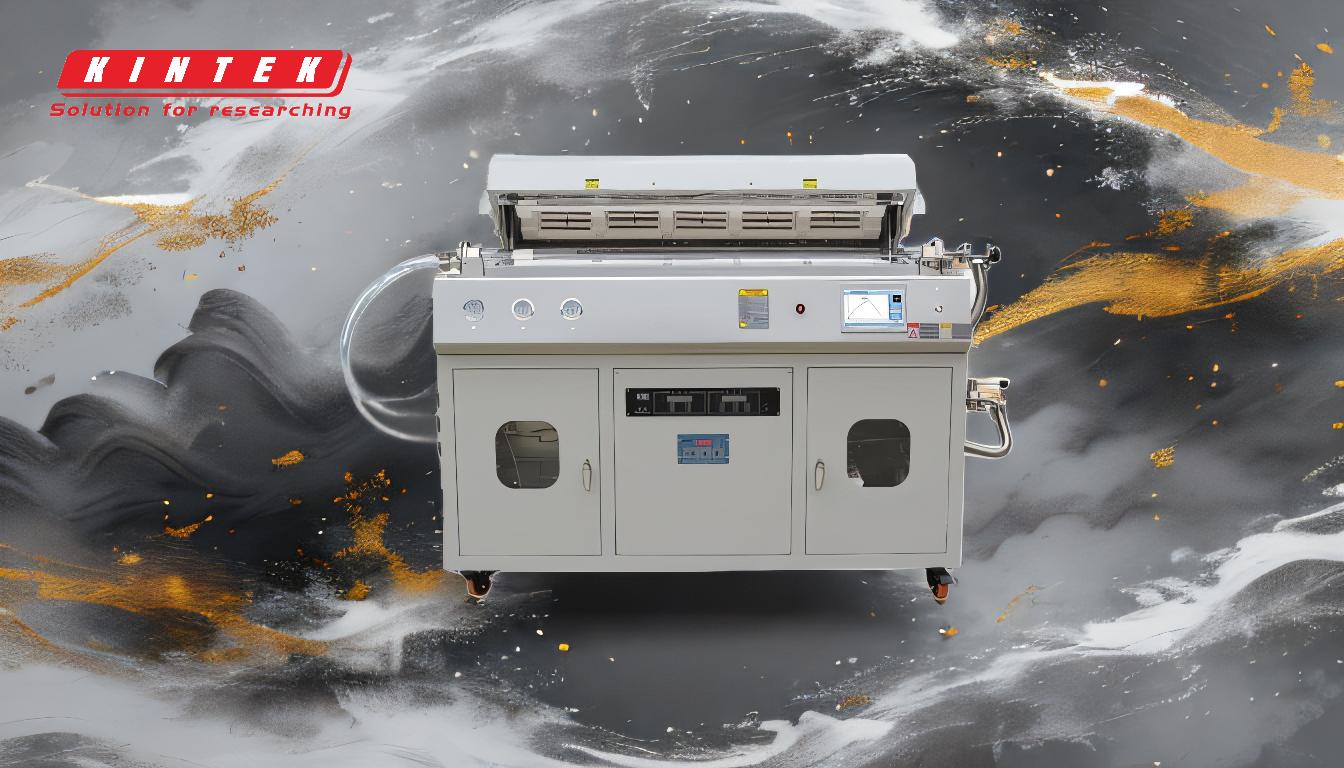
-
Definition of Vacuum Annealing:
- Vacuum annealing is a heat treatment process that involves heating materials in a vacuum environment to achieve specific properties such as increased ductility, reduced internal stresses, and improved strength.
- The process is carried out in a vacuum annealing furnace, which ensures that the material is not exposed to contaminants like oxygen or carbon.
-
How Vacuum Annealing Works:
- The material is heated above its recrystallization temperature in a vacuum furnace. This high-temperature environment allows the material to become more ductile and ready for further processing.
- The vacuum environment prevents oxidation and contamination, ensuring that the material retains its desired properties.
-
Benefits of Using a Vacuum Furnace:
- Uniform Temperature Distribution: Vacuum furnaces provide uniform temperatures over a wide range (800-3,000 °C or 1,500-5,400 °F), ensuring consistent heat treatment.
- Precise Temperature Control: The heating zone in a vacuum furnace allows for precise temperature control, which is crucial for achieving the desired metallurgical properties.
- Low Contamination: The vacuum environment minimizes contamination by carbon, oxygen, and other gases, resulting in higher purity materials.
- Rapid Cooling (Quenching): Vacuum furnaces can rapidly cool materials, which is essential for certain heat treatment processes and helps to shorten the overall cycle time.
- Computer-Controlled Processes: The ability to computer-control the process ensures repeatability and consistency in the heat treatment process.
-
Applications of Vacuum Annealing:
- Metallurgy: Vacuum annealing is widely used in metallurgy to improve the properties of metals such as steel, titanium, and nickel alloys.
- Electronics: In the electronics industry, vacuum annealing is used to treat semiconductor materials, ensuring they have the necessary electrical properties.
- Aerospace: The aerospace industry relies on vacuum annealing to produce high-strength, lightweight components that can withstand extreme conditions.
-
Environmental and Operational Advantages:
- Low Environmental Impact: Vacuum furnaces produce little to no pollution, making them environmentally friendly compared to traditional furnaces.
- Clean Processing: The vacuum environment ensures that the material surfaces remain clean and free from contaminants, which is particularly important for applications requiring high precision.
-
Comparison with Other Annealing Methods:
- Traditional Annealing: Unlike traditional annealing, which is performed in air or protective gas environments, vacuum annealing eliminates the risk of oxidation and contamination.
- Induction Annealing: While induction annealing uses electromagnetic induction to heat materials, vacuum annealing provides a cleaner and more controlled environment, making it suitable for high-purity applications.
In summary, vacuum annealing is a critical process in various industries, offering numerous advantages over traditional methods. The use of a vacuum annealing furnace ensures that materials are treated in a controlled, contamination-free environment, resulting in high-quality products with consistent properties.
Summary Table:
Aspect | Details |
---|---|
Definition | Heat treatment in a vacuum to improve ductility, reduce stress, and enhance strength. |
Key Benefits | - Uniform temperature distribution |
- Precise temperature control
- Low contamination
- Rapid cooling
- Computer-controlled processes | | Applications | - Metallurgy (steel, titanium, nickel alloys)
- Electronics (semiconductors)
- Aerospace (high-strength components) | | Environmental Impact | Low pollution, clean processing, and minimal contamination. | | Comparison | Superior to traditional and induction annealing for high-purity applications. |
Ready to enhance your material properties with vacuum annealing? Contact us today to learn more!