Vacuum-based deposition is a sophisticated technique used to deposit thin layers of material onto a surface at the atomic or molecular level, typically in a high-vacuum environment. This process ensures minimal contamination and allows for precise control over film thickness, ranging from nanometers to millimeters. Key methods include physical vapor deposition (PVD), low-pressure chemical vapor deposition (LPCVD), and low-pressure plasma spraying (LPPS). These methods utilize high-energy ions or plasma to deposit atoms or molecules one at a time, enabling the creation of protective or functional coatings with specific properties. Vacuum deposition is widely used in industries such as electronics, optics, and manufacturing to enhance material performance and durability.
Key Points Explained:
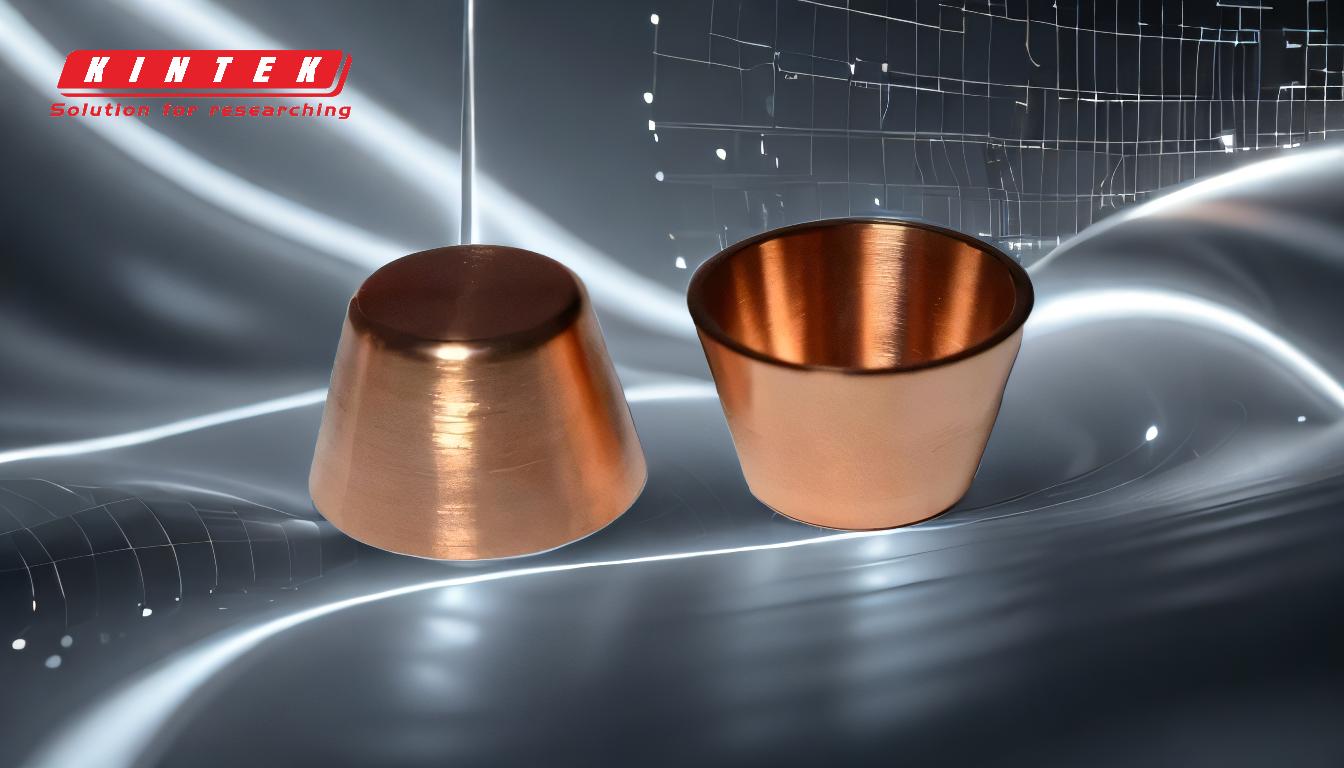
-
Definition and Purpose of Vacuum-Based Deposition:
- Vacuum-based deposition refers to processes that deposit thin layers of material onto a surface in a high-vacuum environment.
- The primary purpose is to create precise, contamination-free coatings with controlled thickness, ranging from atomic layers to millimeters.
-
High-Vacuum Environment:
- The process occurs in a high-vacuum environment to minimize the presence of gas molecules, ensuring a clean and controlled deposition process.
- This environment reduces contamination and allows for the deposition of high-purity materials.
-
Atomic or Molecular Deposition:
- Material is deposited atom-by-atom or molecule-by-molecule, enabling extremely thin and uniform coatings.
- This precision is crucial for applications requiring nanometer-scale accuracy, such as in semiconductor manufacturing.
-
Key Processes in Vacuum Deposition:
- Physical Vapor Deposition (PVD): Involves the physical transfer of material from a source to the substrate, often using techniques like sputtering or evaporation.
- Low-Pressure Chemical Vapor Deposition (LPCVD): Uses chemical reactions at low pressures to deposit thin films, often for creating semiconductor layers.
- Low-Pressure Plasma Spraying (LPPS): Utilizes plasma to deposit materials, often for creating protective coatings on metal parts.
-
Applications of Vacuum Deposition:
- Electronics: Used to deposit thin films in semiconductor devices, integrated circuits, and displays.
- Optics: Applied in the creation of anti-reflective coatings, mirrors, and optical filters.
- Manufacturing: Enhances the durability and performance of tools, molds, and components through protective coatings.
-
Advantages of Vacuum Deposition:
- Precision: Allows for the deposition of extremely thin and uniform layers.
- Purity: High-vacuum environment ensures minimal contamination.
- Versatility: Can be used with a wide range of materials and substrates.
- Control: Enables precise control over film thickness and properties.
-
Challenges and Considerations:
- Cost: High-vacuum equipment and processes can be expensive.
- Complexity: Requires specialized knowledge and equipment.
- Scalability: May be challenging to scale for large-scale production.
-
Future Trends:
- Nanotechnology: Increasing use in nanofabrication for advanced materials and devices.
- Sustainability: Development of more environmentally friendly processes and materials.
- Automation: Integration of automation and AI for improved precision and efficiency.
By understanding these key points, equipment and consumable purchasers can make informed decisions about the use of vacuum-based deposition in their applications, ensuring optimal performance and cost-effectiveness.
Summary Table:
Aspect | Details |
---|---|
Definition | Deposits thin layers of material at atomic/molecular levels in a vacuum. |
Key Methods | PVD, LPCVD, LPPS. |
Applications | Electronics, optics, manufacturing. |
Advantages | Precision, purity, versatility, control. |
Challenges | High cost, complexity, scalability issues. |
Future Trends | Nanotechnology, sustainability, automation. |
Discover how vacuum-based deposition can enhance your project—contact us today for expert guidance!