A vacuum brazing furnace is a specialized type of vacuum furnace designed for the process of vacuum brazing, which involves joining metal components using a filler metal in a vacuum environment. This process eliminates the need for fluxes, prevents oxidation, and ensures high-quality, clean joints. The furnace operates by creating a vacuum state, heating the components to the brazing temperature, and then cooling them to achieve the desired material properties. Key components include the vacuum system, heating elements, cooling systems, and control systems, all of which work together to provide precise temperature and pressure control. Vacuum brazing furnaces are widely used in industries requiring high-precision and contamination-free joining processes, such as aerospace, automotive, and electronics.
Key Points Explained:
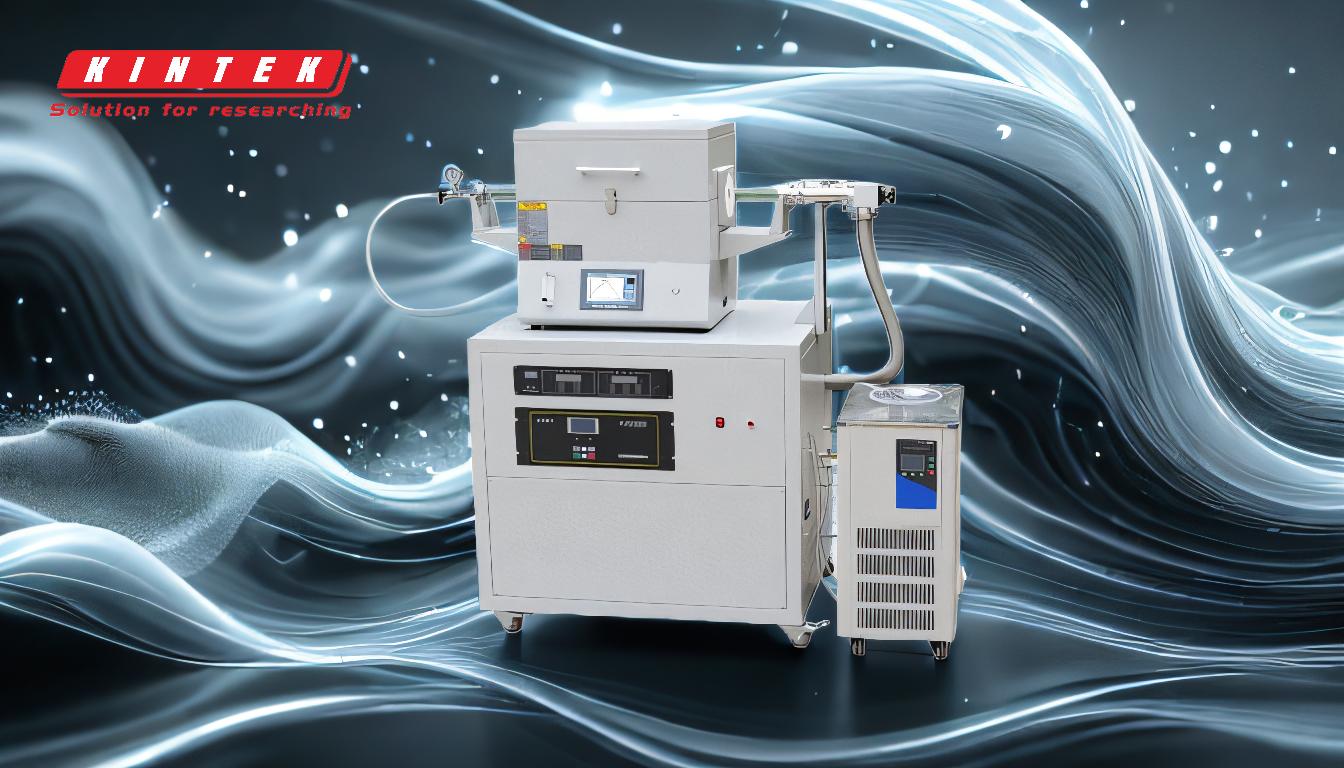
-
Definition and Purpose of a Vacuum Brazing Furnace:
- A vacuum brazing furnace is a specialized equipment used for joining metal components through the process of vacuum brazing. This method involves melting a filler metal in a vacuum environment to create strong, clean, and oxidation-free joints. The absence of oxygen prevents surface oxidation and decarburization, making it ideal for high-precision applications.
-
Key Components of a Vacuum Brazing Furnace:
- Vacuum System: Reduces the pressure inside the furnace chamber to create a vacuum state, ensuring a contamination-free environment.
- Heating System: Provides precise temperature control to heat the components to the brazing temperature, typically using resistance or induction heating elements.
- Cooling System: Facilitates controlled cooling or quenching of the components after brazing to achieve the desired material properties.
- Control System: Manages the entire process, including temperature, pressure, and cooling rates, ensuring repeatability and accuracy.
- Sealing System: Maintains the vacuum integrity of the furnace chamber during operation.
-
How Vacuum Brazing Works:
- The process begins by placing the metal components and filler metal inside the furnace chamber.
- The vacuum system removes air and other gases, creating a low-pressure environment.
- The heating system raises the temperature to the brazing point, causing the filler metal to melt and flow into the joint.
- After brazing, the cooling system gradually lowers the temperature, solidifying the filler metal and forming a strong bond.
-
Advantages of Vacuum Brazing:
- No Oxidation: The vacuum environment prevents oxidation, ensuring clean and high-quality joints.
- No Flux Required: The absence of oxygen eliminates the need for fluxes, reducing post-processing steps.
- Precision and Consistency: The controlled environment and precise temperature regulation result in repeatable and reliable brazing outcomes.
- Contamination-Free: The vacuum prevents contamination from external elements, making it suitable for sensitive applications.
-
Applications of Vacuum Brazing Furnaces:
- Aerospace: Used for joining critical components in aircraft engines and structures, where strength and reliability are paramount.
- Automotive: Employed in the production of high-performance parts, such as heat exchangers and transmission components.
- Electronics: Ideal for brazing delicate electronic components that require contamination-free processing.
- Medical Devices: Used in the manufacture of surgical instruments and implants, where precision and cleanliness are essential.
-
Comparison with Other Brazing Methods:
- Unlike traditional brazing methods that use fluxes and operate in atmospheric conditions, vacuum brazing eliminates the risk of oxidation and contamination. This results in stronger, cleaner, and more reliable joints, making it the preferred method for high-performance applications.
-
Maintenance and Repair:
- Regular maintenance of a vacuum brazing furnace is crucial to ensure optimal performance. Key components such as the vacuum pumps, heating elements, and sealing systems should be inspected and serviced periodically. Degraded parts can often be cleaned, repaired, or replaced to extend the furnace's lifespan.
By understanding the principles, components, and advantages of vacuum brazing furnaces, purchasers can make informed decisions when selecting equipment for their specific applications. This knowledge ensures that the chosen furnace meets the required standards for precision, reliability, and performance.
Summary Table:
Aspect | Details |
---|---|
Definition | Specialized furnace for joining metals in a vacuum environment. |
Key Components | Vacuum system, heating elements, cooling system, control system, sealing. |
Advantages | No oxidation, no flux required, precise temperature control, contamination-free. |
Applications | Aerospace, automotive, electronics, medical devices. |
Maintenance | Regular inspection of vacuum pumps, heating elements, and sealing systems. |
Ready to enhance your manufacturing process with a vacuum brazing furnace? Contact us today for expert guidance!