Vacuum coating technology is a sophisticated process used to apply thin, protective, or functional layers to various substrates such as glass, metal, and plastics. This technology leverages a vacuum environment to deposit materials like metals or ceramics onto surfaces, enhancing properties such as durability, hardness, wear resistance, and aesthetic appeal. It is widely employed across industries including electronics, automotive, aerospace, and consumer goods, with applications ranging from low-emissivity glass and solar cells to decorative coatings and corrosion-resistant layers. The process typically involves physical vapor deposition (PVD), where materials are vaporized or ionized in a vacuum chamber and then deposited onto the substrate, creating nanoscale coatings with tailored properties.
Key Points Explained:
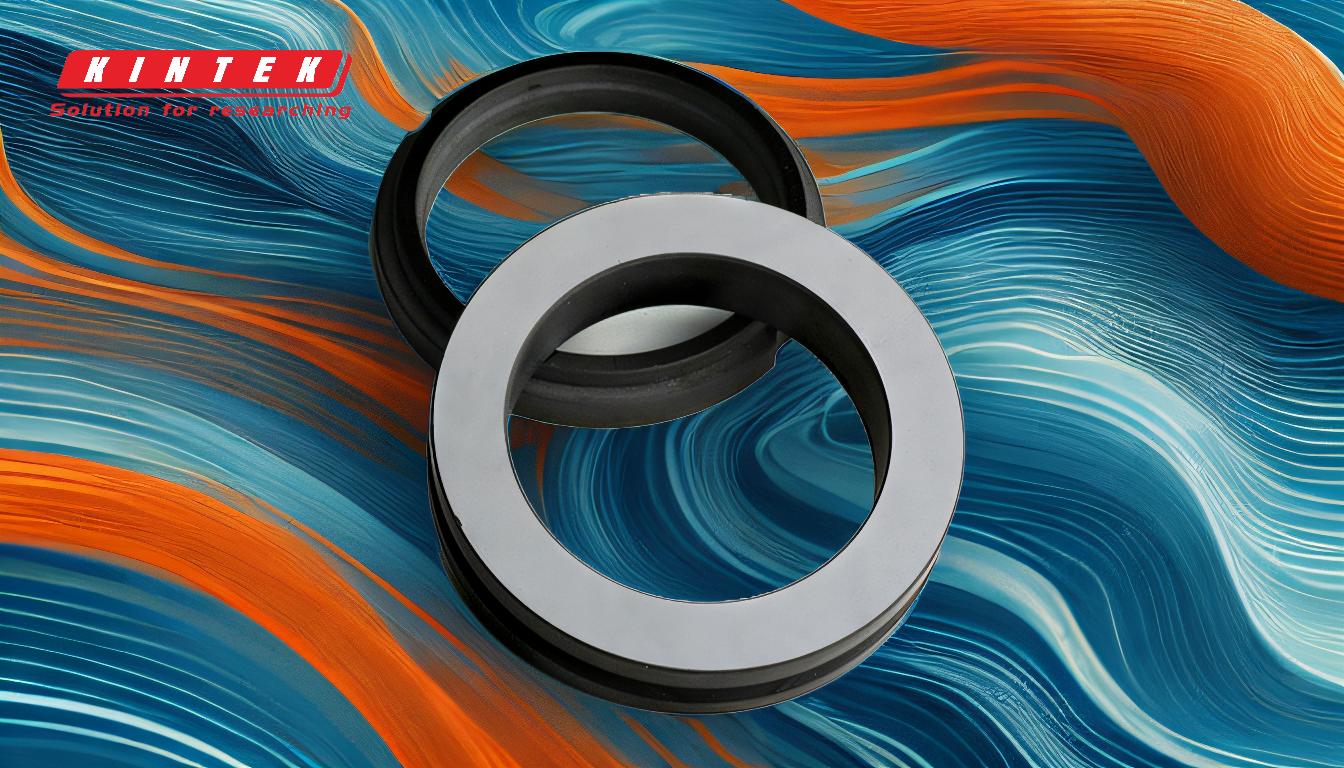
-
Definition and Process of Vacuum Coating Technology:
- Vacuum coating is a form of physical vapor deposition (PVD) conducted in a vacuum chamber.
- Materials such as metals or ceramics are vaporized or ionized using thermal energy or plasma.
- The vaporized material is then deposited onto substrates, forming extremely thin (nanoscale) layers.
- This process ensures precise control over coating thickness and uniformity.
-
Applications of Vacuum Coating:
- Decorative and Functional Coatings: Used on glass, metal, and plastics for both aesthetic and durability purposes. Examples include low-emissivity glass, decorative finishes, and wear-resistant coatings.
- Energy Efficiency: Applied in solar cells and energy-saving glass to enhance conductivity and light harvesting properties.
- Industrial and Automotive: Used for hard coatings on engine components, corrosion protection, and coatings on carbon fiber composites.
- Electronics and Semiconductors: Essential for manufacturing microchips, LEDs, thin-film transistors, and flexible displays.
- Medical and Aerospace: Provides protective and functional coatings for specialized equipment and components.
-
Benefits of Vacuum Coating:
- Enhanced Durability: Improves hardness, wear resistance, and corrosion protection.
- Improved Performance: Enhances electrical conductivity, optical properties, and energy efficiency.
- Aesthetic Appeal: Adds decorative finishes to products.
- Precision and Uniformity: Ensures consistent, high-quality coatings at the nanoscale level.
-
Industries Utilizing Vacuum Coating:
- Consumer Goods: Tableware, home furnishings, and packaging materials.
- Building and Construction: Energy-efficient glass and durable building materials.
- Electronics: Solar cells, microchips, and flexible displays.
- Automotive and Aerospace: Engine components, carbon fiber composites, and specialized coatings.
- Medical: Coatings for medical devices and equipment.
-
Future Trends and Innovations:
- Continued advancements in materials and deposition techniques to improve coating performance.
- Expansion into emerging fields such as flexible electronics and renewable energy.
- Increased adoption in industries seeking lightweight, durable, and high-performance materials.
Vacuum coating technology is a versatile and transformative process that plays a critical role in modern manufacturing and innovation. Its ability to enhance material properties and enable new applications makes it indispensable across a wide range of industries.
Summary Table:
Aspect | Details |
---|---|
Process | Physical vapor deposition (PVD) in a vacuum chamber. |
Applications | Decorative coatings, solar cells, automotive parts, electronics, aerospace. |
Benefits | Enhanced durability, improved performance, aesthetic appeal, precision. |
Industries | Consumer goods, construction, electronics, automotive, medical, aerospace. |
Future Trends | Advanced materials, flexible electronics, renewable energy applications. |
Unlock the potential of vacuum coating for your industry—contact our experts today!