Vacuum evaporation in thin film deposition is a Physical Vapor Deposition (PVD) process where a material is vaporized in a high vacuum environment and then deposited onto a substrate to form a thin film. The process involves heating the source material until it evaporates, and the vapor travels through the vacuum to condense on the substrate. This method ensures high-purity films due to the absence of gas molecule collisions and contamination. It is widely used in industries requiring precise and uniform thin films, such as electronics, optics, and coatings.
Key Points Explained:
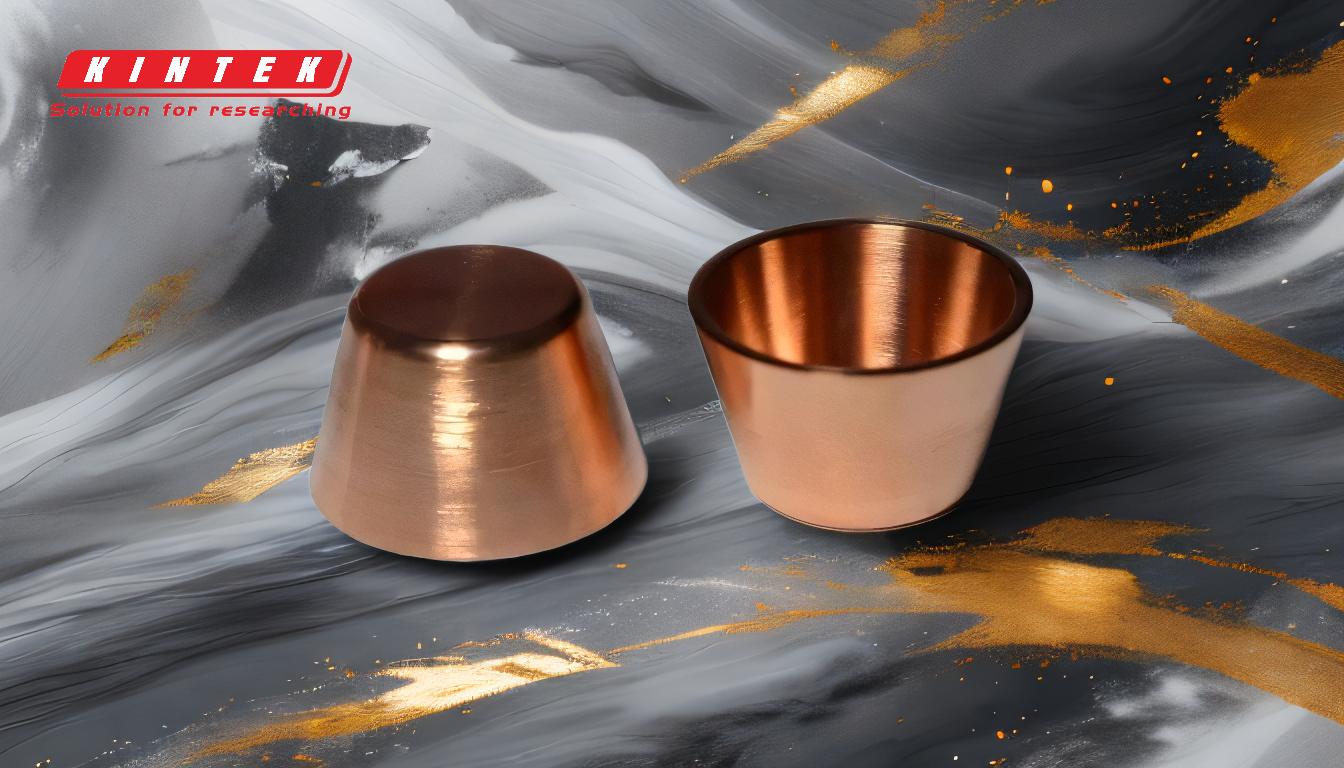
-
Definition and Overview of Vacuum Evaporation:
- Vacuum evaporation is a PVD technique used to deposit thin films on substrates.
- It operates in a high vacuum environment (10^-5 to 10^-9 Torr) to minimize gas molecule collisions and contamination.
- The process is line-of-sight, meaning the vaporized material travels directly from the source to the substrate.
-
Process Steps:
- Evaporation: The source material is heated until it evaporates. This can be achieved using resistively heated wires, boats, crucibles, or electron beams.
- Transport: The vaporized material travels through the vacuum chamber to the substrate.
- Condensation: The vapor condenses on the substrate, forming a solid thin film.
-
Heat Sources for Evaporation:
- Resistive Heating: Uses electrically heated wires or crucibles to vaporize the material.
- Electron Beam Evaporation: Focuses a high-energy electron beam on the source material to achieve evaporation.
- These heat sources must withstand high temperatures and have a significantly higher melting point than the material being evaporated.
-
Advantages of Vacuum Evaporation:
- High Purity: The vacuum environment prevents contamination, resulting in high-purity films.
- Uniform Deposition: The line-of-sight nature ensures uniform film thickness.
- Versatility: Suitable for a wide range of materials, including metals, semiconductors, and insulators.
-
Applications:
- Electronics: Used in the fabrication of semiconductors, solar cells, and displays.
- Optics: Deposits anti-reflective coatings, mirrors, and optical filters.
- Coatings: Provides protective and decorative coatings for various materials.
-
Challenges and Considerations:
- Material Limitations: Some materials may decompose or react at high temperatures.
- Equipment Cost: High vacuum systems and specialized heat sources can be expensive.
- Substrate Compatibility: The substrate must withstand the vacuum environment and deposition conditions.
-
Comparison with Other PVD Techniques:
- Sputtering: Uses energetic ions to dislodge atoms from a target material, offering better adhesion and step coverage.
- Chemical Vapor Deposition (CVD): Involves chemical reactions to deposit films, suitable for complex geometries but may introduce impurities.
- Vacuum evaporation is simpler and more cost-effective for certain applications but may not provide the same level of adhesion or step coverage as sputtering.
By understanding these key points, one can appreciate the role of vacuum evaporation in thin film deposition and its significance in various industrial applications.
Summary Table:
Aspect | Details |
---|---|
Definition | A PVD process where material is vaporized in a vacuum and deposited on a substrate. |
Process Steps | Evaporation → Transport → Condensation |
Heat Sources | Resistive heating, electron beam evaporation |
Advantages | High purity, uniform deposition, versatility |
Applications | Electronics, optics, coatings |
Challenges | Material limitations, high equipment cost, substrate compatibility |
Comparison with PVD | Simpler and cost-effective but less adhesion/step coverage than sputtering |
Discover how vacuum evaporation can enhance your thin film processes—contact our experts today!