Vacuum hardening is a specialized heat treatment process where materials are heated to high temperatures in a vacuum environment, followed by controlled cooling to achieve desired mechanical properties. This process is particularly useful for metals that are sensitive to oxidation or require precise control over the heating and cooling phases. The vacuum environment eliminates the presence of air, preventing oxidation and decarburization, and allows for the introduction of specific gases if needed. The process involves determining the heating system (temperature, time, and mode), setting the vacuum degree, and selecting the cooling medium. Vacuum hardening is widely used in industries requiring high precision and quality, such as aerospace, automotive, and tool manufacturing.
Key Points Explained:
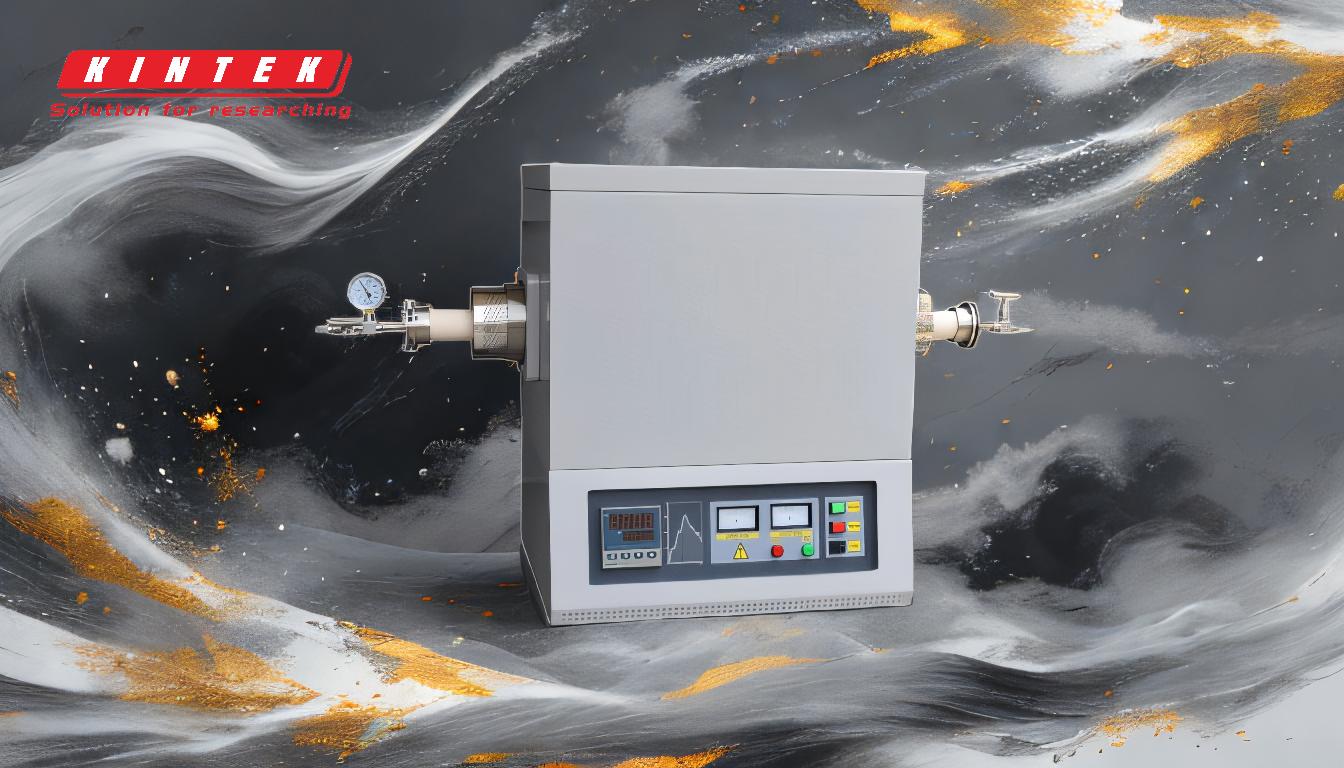
-
Definition and Purpose of Vacuum Hardening:
- Vacuum hardening is a heat treatment process performed in a vacuum or protective gas environment to prevent oxidation and decarburization.
- It is used to enhance the mechanical properties of materials, such as hardness, strength, and wear resistance, while maintaining surface integrity.
-
Components of the Vacuum Hardening Process:
- Heating System: The material is heated to a specific temperature using resistance or induction heating. The temperature and duration are carefully controlled to achieve the desired microstructure.
- Vacuum Environment: The process occurs in a vacuum hardening furnace, where air is removed to create a controlled atmosphere. This prevents oxidation and allows for the introduction of specific gases if required.
- Cooling Mode and Medium: After heating, the material is cooled at controlled rates using various media, such as gas, oil, or water, to achieve the desired hardness and microstructure.
-
Advantages of Vacuum Hardening:
- Oxidation Prevention: The absence of air in the vacuum environment prevents oxidation, ensuring a clean and bright surface finish.
- Precision Control: The process allows for precise control over temperature, heating rate, and cooling rate, leading to consistent and high-quality results.
- Improved Material Properties: Vacuum hardening enhances hardness, strength, and wear resistance while minimizing distortion and residual stresses.
-
Applications of Vacuum Hardening:
- Tool and Die Manufacturing: Used to harden cutting tools, molds, and dies, ensuring long-lasting performance and precision.
- Aerospace and Automotive Industries: Applied to critical components that require high strength, durability, and resistance to wear and fatigue.
- Medical Devices: Used for surgical instruments and implants that demand high precision and biocompatibility.
-
Comparison with Other Heat Treatment Processes:
- Vacuum Hardening vs. Conventional Hardening: Unlike conventional hardening, vacuum hardening eliminates the risk of oxidation and decarburization, resulting in a cleaner and more precise finish.
- Vacuum Hardening vs. Case Hardening: While case hardening focuses on surface hardening, vacuum hardening can achieve uniform hardening throughout the material.
-
Process Variations:
- Vacuum Quenching: A rapid cooling process performed in a vacuum environment to achieve high hardness.
- Vacuum Tempering: A follow-up process to reduce brittleness and improve toughness after quenching.
- Vacuum Annealing: Used to soften materials and relieve internal stresses, often as a preparatory step before further processing.
-
Equipment Used in Vacuum Hardening:
- Vacuum Hardening Furnace: The primary equipment used for heating and cooling materials in a controlled vacuum environment. It includes features like temperature control, gas injection systems, and cooling mechanisms.
-
Considerations for Purchasing a Vacuum Hardening Furnace:
- Temperature Range: Ensure the furnace can achieve the required temperatures for your specific materials.
- Cooling Options: Look for furnaces with versatile cooling systems to accommodate different materials and desired outcomes.
- Vacuum Level: Consider the vacuum level the furnace can achieve, as this impacts the quality of the hardening process.
- Automation and Control: Advanced control systems can improve process consistency and reduce operator error.
By understanding these key points, purchasers and engineers can make informed decisions about implementing vacuum hardening processes and selecting the appropriate equipment for their needs.
Summary Table:
Aspect | Details |
---|---|
Purpose | Enhances hardness, strength, and wear resistance while preventing oxidation. |
Key Components | Heating system, vacuum environment, and cooling medium. |
Advantages | Oxidation prevention, precise control, and improved material properties. |
Applications | Aerospace, automotive, tool manufacturing, and medical devices. |
Equipment | Vacuum hardening furnace with temperature control and cooling systems. |
Interested in vacuum hardening for your industry? Contact us today to learn more!