A vacuum heat treatment furnace is a specialized piece of equipment used to heat treat metals and other materials in a vacuum environment. This process involves removing air from a sealed chamber using a vacuum pump, ensuring no oxidation or contamination occurs during heating. The furnace is designed to achieve high thermal efficiency, rapid temperature changes, and precise control over the heat treatment process. It is widely used in industries such as aerospace, automotive, and tool manufacturing, where material properties like hardness, strength, and durability are critical. The vacuum environment also allows for surface purification, degassing, and prevention of defects like hydrogen embrittlement, making it a versatile and essential tool for advanced material processing.
Key Points Explained:
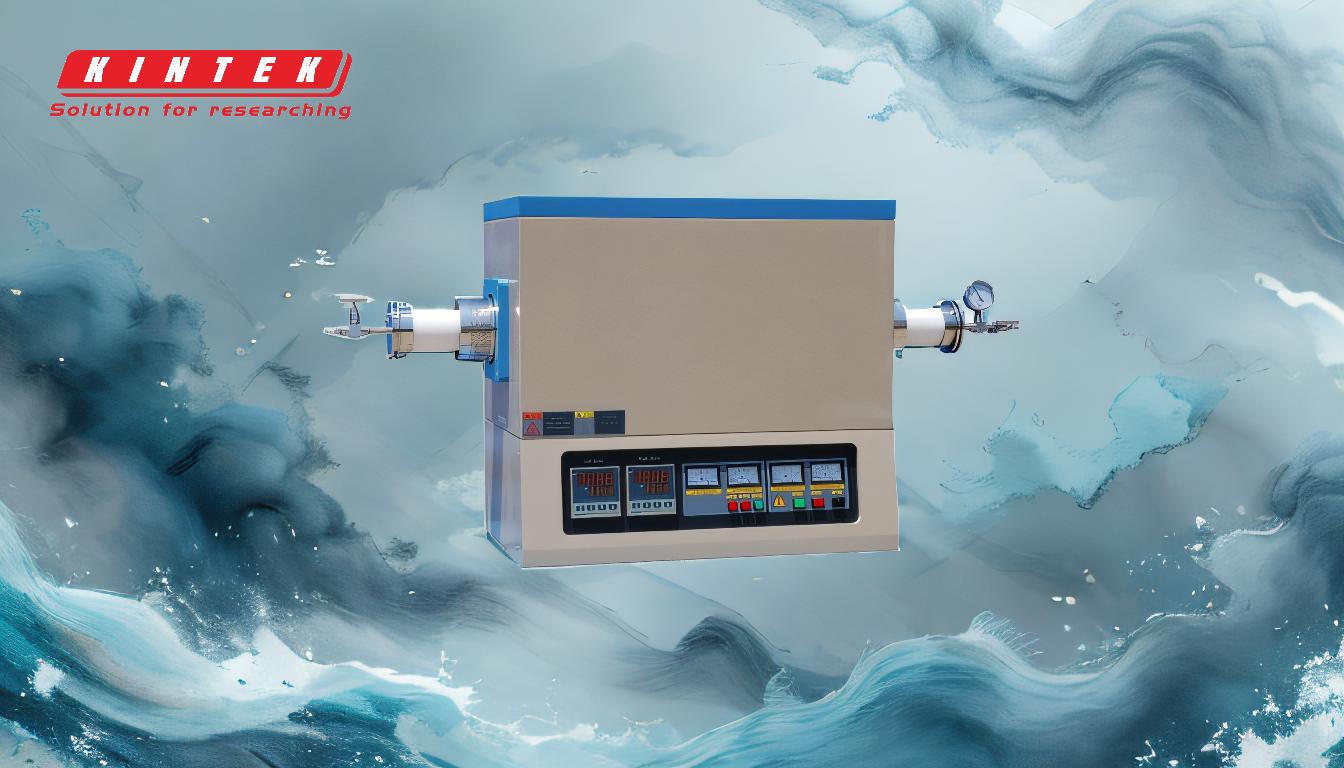
-
Definition and Purpose of a Vacuum Heat Treatment Furnace
A vacuum heat treatment furnace is a device that combines vacuum technology with heat treatment processes. It is used to heat treat metals and other materials in a vacuum environment, ensuring no oxidation, decarburization, or contamination occurs. This method is ideal for achieving precise material properties such as hardness, strength, and durability. Learn more about vacuum heat treat furnace and its applications. -
Key Components and Working Mechanism
- Vacuum Chamber: A sealed environment where air is removed using a vacuum pump to create a controlled atmosphere.
- Heating Elements: Typically made of materials like silicon carbide or graphite, these elements provide uniform heating.
- Cooling System: Inert gases like nitrogen or argon are used to rapidly cool the materials after heat treatment, ensuring minimal thermal stress and deformation.
- Temperature Control System: Advanced systems with multi-segment programming allow precise control over heating and cooling cycles.
-
Advantages of Vacuum Heat Treatment
- No Oxidation or Contamination: The vacuum environment prevents oxidation, decarburization, and carburization, resulting in a bright, clean surface.
- Improved Material Properties: Enhances mechanical properties like hardness, strength, and service life.
- Energy Efficiency: High thermal efficiency and rapid temperature changes reduce energy consumption.
- Environmental Safety: No harmful emissions or pollution, ensuring a safe working environment.
- Versatility: Suitable for a wide range of materials, including metals, ceramics, and composites.
-
Applications in Various Industries
- Aerospace: Used for heat treating critical components like turbine blades and engine parts.
- Automotive: Enhances the durability and performance of gears, shafts, and other components.
- Tool Manufacturing: Improves the hardness and wear resistance of cutting tools and dies.
- Powder Metallurgy: Enables sintering and densification of metal powders.
- Ceramics and Composites: Facilitates high-temperature pressing and solid-phase reactions for advanced materials.
-
Types of Vacuum Heat Treatment Furnaces
- Vacuum Chamber Furnace: Used for heat treatment under low vacuum and controlled atmospheres.
- Vacuum Hot Press Furnace: Designed for pressing and sintering materials like cemented carbide and ceramics.
- Vacuum Brazing Furnace: Used for joining metal parts with high precision and minimal distortion.
- Vacuum Annealing Furnace: Ideal for softening metals and relieving internal stresses.
-
Operational Considerations
- Maintenance: Regular maintenance of vacuum pumps, heating elements, and cooling systems is essential for optimal performance.
- Safety: Proper handling of inert gases and adherence to safety protocols are critical to prevent accidents.
- Cost-Effectiveness: While the initial investment is high, the long-term benefits of improved product quality and reduced waste make it cost-effective.
By understanding the principles, advantages, and applications of vacuum heat treatment furnaces, industries can leverage this technology to achieve superior material properties and enhance product performance.
Summary Table:
Aspect | Details |
---|---|
Purpose | Heat treatment of metals and materials in a vacuum environment to prevent oxidation. |
Key Components | Vacuum chamber, heating elements, cooling system, temperature control system. |
Advantages | No oxidation, improved material properties, energy efficiency, environmental safety. |
Applications | Aerospace, automotive, tool manufacturing, powder metallurgy, ceramics, and composites. |
Types | Vacuum chamber furnace, vacuum hot press furnace, vacuum brazing furnace, vacuum annealing furnace. |
Operational Considerations | Regular maintenance, safety protocols, and cost-effectiveness. |
Ready to enhance your material processing? Contact us today to learn more about vacuum heat treatment furnaces!