Vacuum inerting is a process used to create an inert environment by removing reactive gases, such as oxygen and moisture, and replacing them with non-reactive inert gases like nitrogen or argon. This technique is commonly employed in industries where sensitive materials or processes require protection from oxidation, hydrolysis, or other chemical reactions. By first evacuating the air (creating a vacuum) and then introducing an inert gas, the system ensures a stable, non-reactive atmosphere. This method is particularly useful in applications like chemical storage, food preservation, and semiconductor manufacturing, where maintaining purity and preventing contamination are critical.
Key Points Explained:
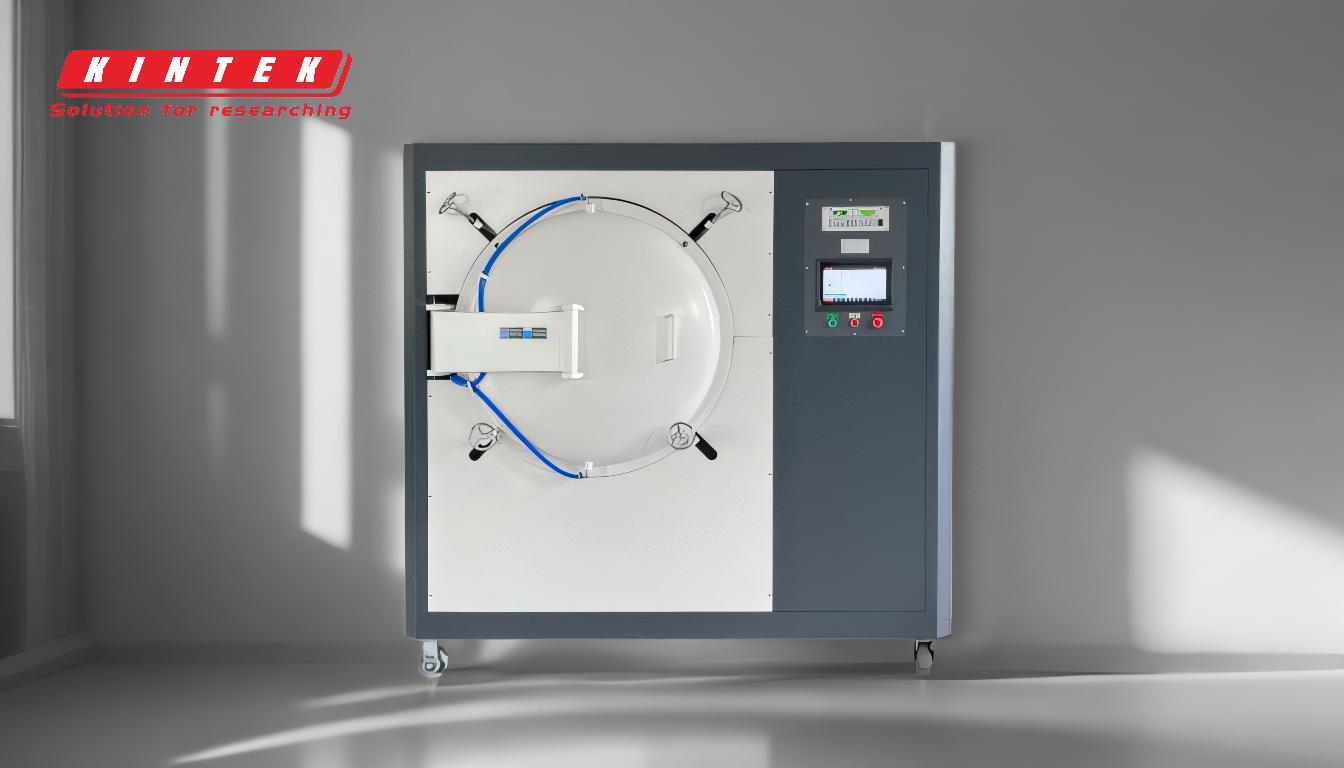
-
Definition of Vacuum Inerting
- Vacuum inerting involves two main steps:
- Evacuation: Removing air (and thus oxygen and moisture) from a system by creating a vacuum.
- Inert Gas Introduction: Replacing the evacuated air with an inert gas, such as nitrogen or argon, to create a non-reactive environment.
- This process ensures that sensitive materials or processes are protected from oxidation, hydrolysis, or other undesirable chemical reactions.
- Vacuum inerting involves two main steps:
-
Purpose of Vacuum Inerting
- Preventing Oxidation: Oxygen in the air can react with materials, leading to degradation. Vacuum inerting eliminates oxygen, preventing such reactions.
- Avoiding Hydrolysis: Moisture in the air can cause hydrolysis, which breaks down certain materials. Removing moisture through vacuum inerting mitigates this risk.
- Enhancing Safety: Inerting reduces the risk of fire or explosion in environments where flammable gases or powders are present.
-
Applications of Vacuum Inerting
- Chemical Storage: Storing reactive chemicals in an inert environment prevents degradation and ensures stability.
- Food Preservation: Inerting is used in packaging to extend the shelf life of food products by preventing oxidation.
- Semiconductor Manufacturing: Maintaining a pure, inert atmosphere is critical for producing high-quality semiconductors.
- Pharmaceuticals: Protecting sensitive drugs and compounds from contamination during production and storage.
-
Advantages of Vacuum Inerting
- Improved Material Integrity: By preventing chemical reactions, vacuum inerting preserves the quality and functionality of materials.
- Cost-Effectiveness: Reducing waste and spoilage leads to lower operational costs.
- Versatility: The process can be adapted to various industries and applications.
-
Inert Gases Used in Vacuum Inerting
- Nitrogen: Widely used due to its availability, low cost, and effectiveness in displacing oxygen.
- Argon: Preferred in applications requiring a higher level of inertness, such as welding or semiconductor production.
- Helium: Used in specialized applications, though less common due to its higher cost.
-
Process Steps in Vacuum Inerting
- Initial Evacuation: The system is evacuated to remove air and create a vacuum.
- Inert Gas Introduction: An inert gas is introduced to replace the evacuated air.
- Cycle Repetition: The process may be repeated multiple times to achieve the desired level of inertness.
- Monitoring and Control: Sensors and control systems ensure the environment remains inert throughout the process.
-
Considerations for Implementing Vacuum Inerting
- System Design: The equipment must be designed to withstand vacuum conditions and handle inert gases safely.
- Gas Purity: The quality of the inert gas used is critical to achieving the desired level of protection.
- Cost and Efficiency: Balancing the cost of inert gases and the efficiency of the process is essential for economic viability.
By understanding and applying vacuum inerting, industries can effectively protect sensitive materials and processes from degradation, ensuring safety, quality, and cost-effectiveness.
Summary Table:
Key Aspect | Details |
---|---|
Definition | Process of removing air and replacing it with inert gases like nitrogen. |
Purpose | Prevents oxidation, hydrolysis, and enhances safety. |
Applications | Chemical storage, food preservation, semiconductor manufacturing. |
Advantages | Improved material integrity, cost-effectiveness, versatility. |
Inert Gases Used | Nitrogen, argon, helium. |
Process Steps | Evacuation, inert gas introduction, cycle repetition, monitoring. |
Implementation Considerations | System design, gas purity, cost and efficiency. |
Discover how vacuum inerting can safeguard your processes—contact us today!