Vacuum sintering is a specialized process used in industrial metallurgy and materials science to create high-density, high-performance materials. It involves heating materials in a vacuum environment to near-melting temperatures, allowing atomic diffusion to occur without oxidation or contamination. This process is particularly useful for materials with high melting points, such as ceramics, metals, and alloys. The vacuum environment ensures that the materials remain free from impurities, resulting in superior mechanical and thermal properties. Vacuum sintering is widely used in industries like aerospace, electronics, and manufacturing for producing components with precise specifications and enhanced durability.
Key Points Explained:
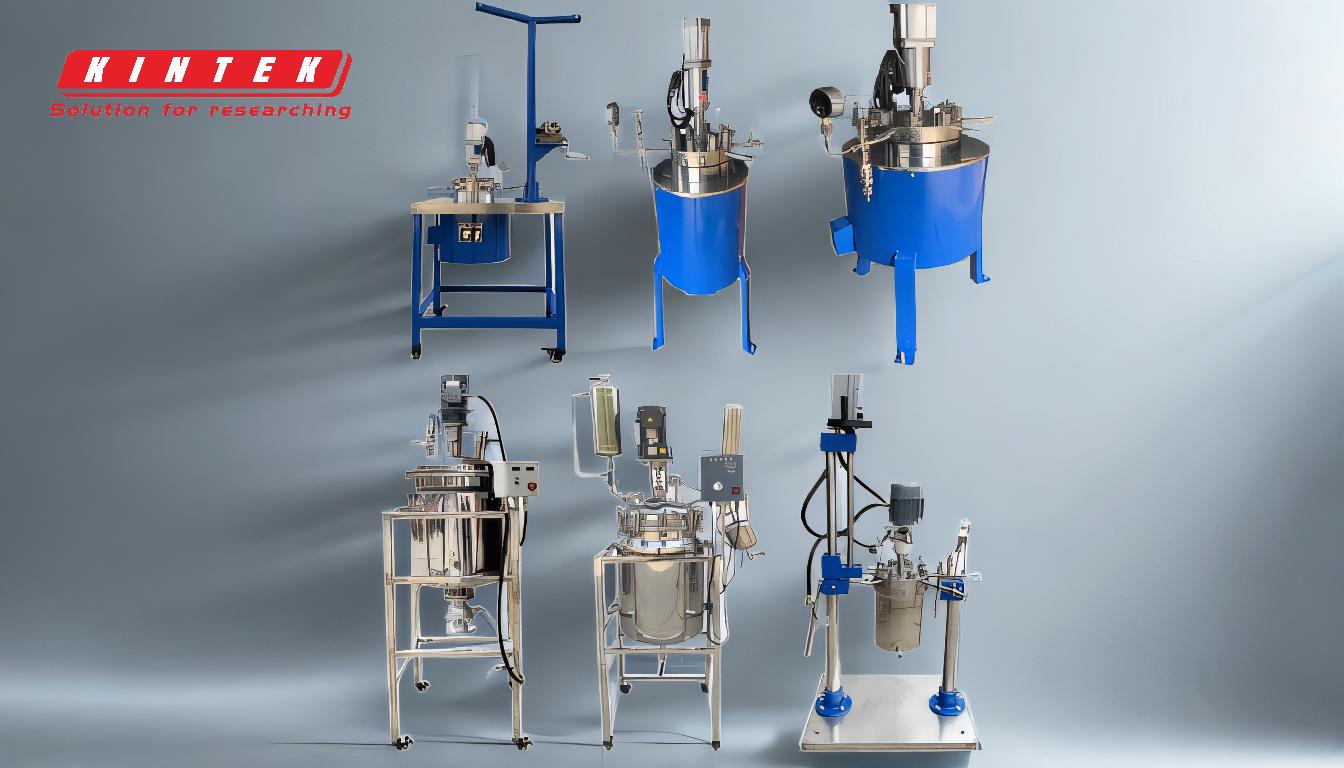
-
Definition of Vacuum Sintering:
- Vacuum sintering is a process where materials are heated in a vacuum environment to near-melting temperatures. This allows atomic diffusion to occur, compacting the material into a dense, solid form without melting it completely. The absence of air prevents oxidation and contamination, ensuring high-quality results.
-
Working Principle of a Vacuum Sintering Furnace:
- A vacuum sintering furnace operates by creating a vacuum state inside the chamber, removing all atmospheric gases. The material is then heated to high temperatures, enabling atomic diffusion and grain boundary movement. This results in a dense, strong product with improved mechanical properties.
-
Steps in the Vacuum Sintering Process:
- Charging: The material is placed inside the furnace.
- Vacuum Creation: Air is evacuated to create a vacuum environment.
- Heating: The temperature is gradually increased to the sintering point.
- Insulation: The material is held at the sintering temperature for a specific duration.
- Cooling: The material is cooled under controlled conditions to prevent oxidation.
-
Advantages of Vacuum Sintering:
- Oxidation Prevention: The vacuum environment eliminates the risk of oxidation, ensuring purity.
- Enhanced Material Properties: The process improves density, strength, and thermal stability.
- Versatility: Suitable for a wide range of materials, including ceramics, metals, and alloys.
-
Applications of Vacuum Sintering:
- Ceramics and Hard Alloys: Used for producing high-performance ceramics and hard alloy materials.
- Optical and Electrical Components: Ideal for manufacturing optical and electrical molding materials.
- Graphite Purification: Used in the purification and sintering of graphite materials.
-
Comparison with Other Sintering Methods:
- Unlike atmosphere sintering, which relies on controlled gas environments, vacuum sintering eliminates all gases, offering superior purity and material properties. It is also more effective than traditional sintering methods for materials with high melting points.
-
Industrial Significance:
- Vacuum sintering is critical in industries requiring high-precision components, such as aerospace, electronics, and advanced manufacturing. The process ensures that materials meet stringent quality standards and perform reliably under extreme conditions.
By understanding these key points, a purchaser of vacuum sintering equipment can make informed decisions about the suitability of this process for their specific applications and material requirements.
Summary Table:
Aspect | Details |
---|---|
Definition | Heating materials in a vacuum to near-melting temperatures for atomic diffusion. |
Working Principle | Uses a vacuum sintering furnace to remove gases, enabling atomic diffusion. |
Steps | Charging, vacuum creation, heating, insulation, and controlled cooling. |
Advantages | Prevents oxidation, enhances material properties, and offers versatility. |
Applications | Ceramics, hard alloys, optical/electrical components, and graphite purification. |
Industrial Significance | Critical for aerospace, electronics, and manufacturing industries. |
Ready to enhance your material performance? Contact us today for expert advice on vacuum sintering solutions!