Vacuum tempering is a specialized heat treatment process conducted in a vacuum environment to enhance the mechanical properties of metals, particularly steel. This process involves heating the metal to a specific temperature below its critical point, holding it at that temperature for a predetermined time, and then cooling it in a controlled manner. The vacuum environment eliminates oxidation, decarburization, and contamination, ensuring a clean and precise treatment. This results in improved material properties such as increased toughness, ductility, and resistance to corrosion. Vacuum tempering is widely used in industries requiring high precision and quality, such as aerospace, automotive, and tool manufacturing.
Key Points Explained:
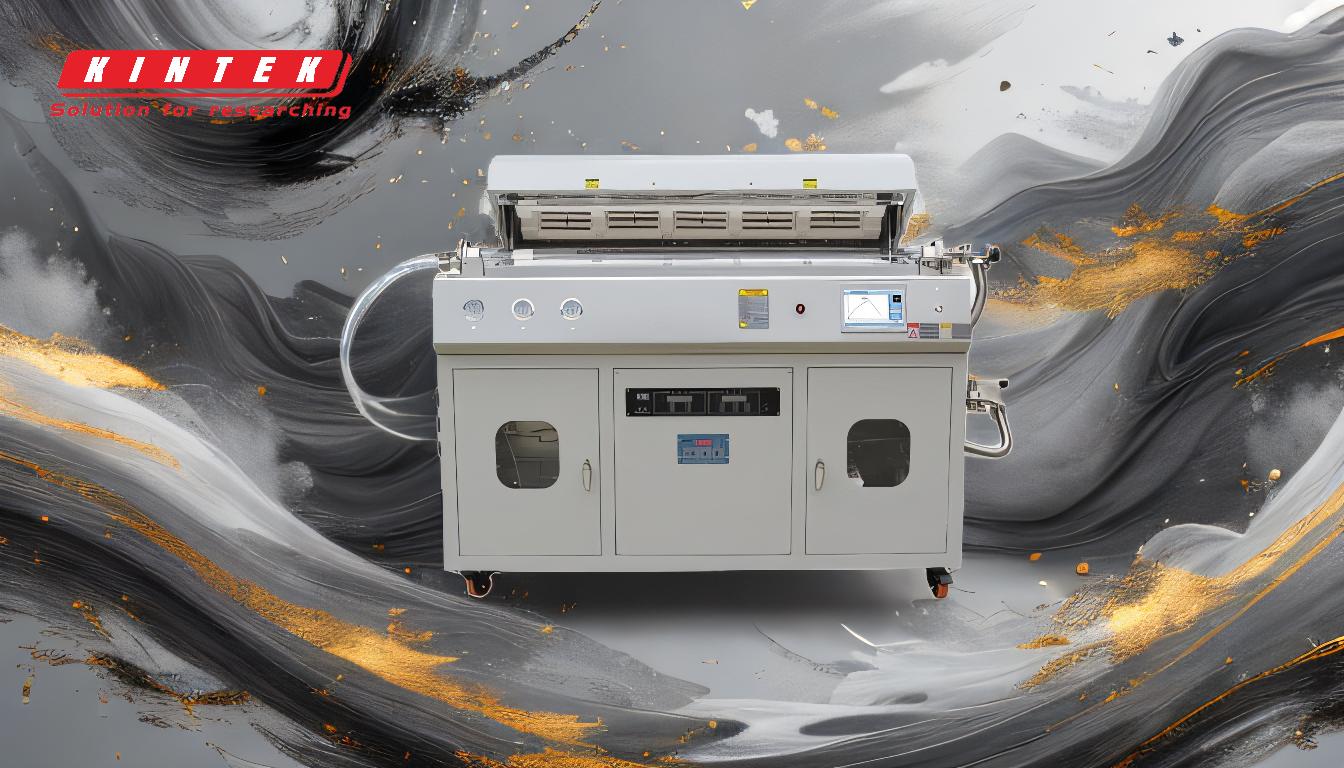
-
Definition and Process of Vacuum Tempering:
- Vacuum tempering is a heat treatment process performed in a vacuum environment to improve the mechanical properties of metals.
- The process involves heating the metal to a specific temperature, holding it for a set duration, and then cooling it in a controlled manner.
- The vacuum environment prevents oxidation, decarburization, and contamination, ensuring a clean and precise treatment.
-
Benefits of Vacuum Tempering:
- Eco-Friendly: Saves energy and reduces environmental impact.
- Faster Processing Times: Enhances productivity by reducing cycle times.
- Avoids Discoloration: Maintains the aesthetic quality of materials.
- Prevents Corrosion: Imparts anti-corrosive qualities to the steel, extending its service life.
-
Advantages of Using a Vacuum Furnace:
- High Thermal Efficiency: Ensures efficient use of energy.
- Rapid Temperature Control: Allows for quick heating and cooling, improving process efficiency.
- No Oxidation or Decarburization: Maintains the integrity and surface quality of the material.
- Surface Purification: Achieves a bright, clean surface finish.
- Reduced Thermal Stress and Deformation: Minimizes material distortion, leading to higher product pass rates.
- Improved Mechanical Properties: Enhances strength, toughness, and durability of the treated materials.
- Safe and Pollution-Free Environment: Provides a clean and safe working environment, free from harmful emissions.
-
Applications of Vacuum Tempering:
- Aerospace Industry: Used for critical components requiring high strength and corrosion resistance.
- Automotive Industry: Enhances the performance and longevity of engine parts and tools.
- Tool Manufacturing: Improves the wear resistance and toughness of cutting tools and dies.
- 3D Printing: Essential for the production of high-quality powdered metals used in additive manufacturing.
-
Importance of Vacuum Environment in Heat Treatment:
- Controlled Atmosphere: Provides precise control over the heat treatment process, ensuring consistent results.
- Prevention of Impurities: Reduces the risk of contamination during melting and casting of alloys.
- Lower Temperature Processes: Enables processes like carburization to be performed at lower temperatures, reducing the risk of oxygen contamination.
-
Historical and Industry Relevance:
- Decades of Use: Vacuum heating processes have been utilized in the industry for decades due to their numerous benefits.
- Special Applications: Particularly valuable in applications requiring high precision and quality, such as in the production of medical devices and high-performance alloys.
By understanding these key points, it becomes clear why vacuum heat treatment is a preferred method for achieving superior material properties and ensuring high-quality production in various industries.
Summary Table:
Key Aspect | Details |
---|---|
Definition | Heat treatment in a vacuum to enhance metal properties. |
Benefits | Eco-friendly, faster processing, avoids discoloration, prevents corrosion. |
**Advantages of Vacuum Furnace | High thermal efficiency, rapid temperature control, no oxidation, safe. |
Applications | Aerospace, automotive, tool manufacturing, 3D printing. |
Importance of Vacuum | Controlled atmosphere, prevents impurities, enables lower temperature processes. |
Discover how vacuum tempering can elevate your material quality—contact us today for expert advice!