Vim, in the context of metallurgy, refers to Vacuum Induction Melting, a specialized process used to produce high-quality metals and alloys. This method involves melting metals under a vacuum environment using electromagnetic induction heating. The vacuum environment eliminates impurities and gases, ensuring the production of clean, high-purity metals with precise chemical compositions. VIM is particularly crucial in industries requiring materials with exceptional mechanical properties, such as aerospace, medical implants, and advanced engineering applications. The process is highly controlled, allowing for the creation of alloys with specific characteristics, making it indispensable in modern metallurgy.
Key Points Explained:
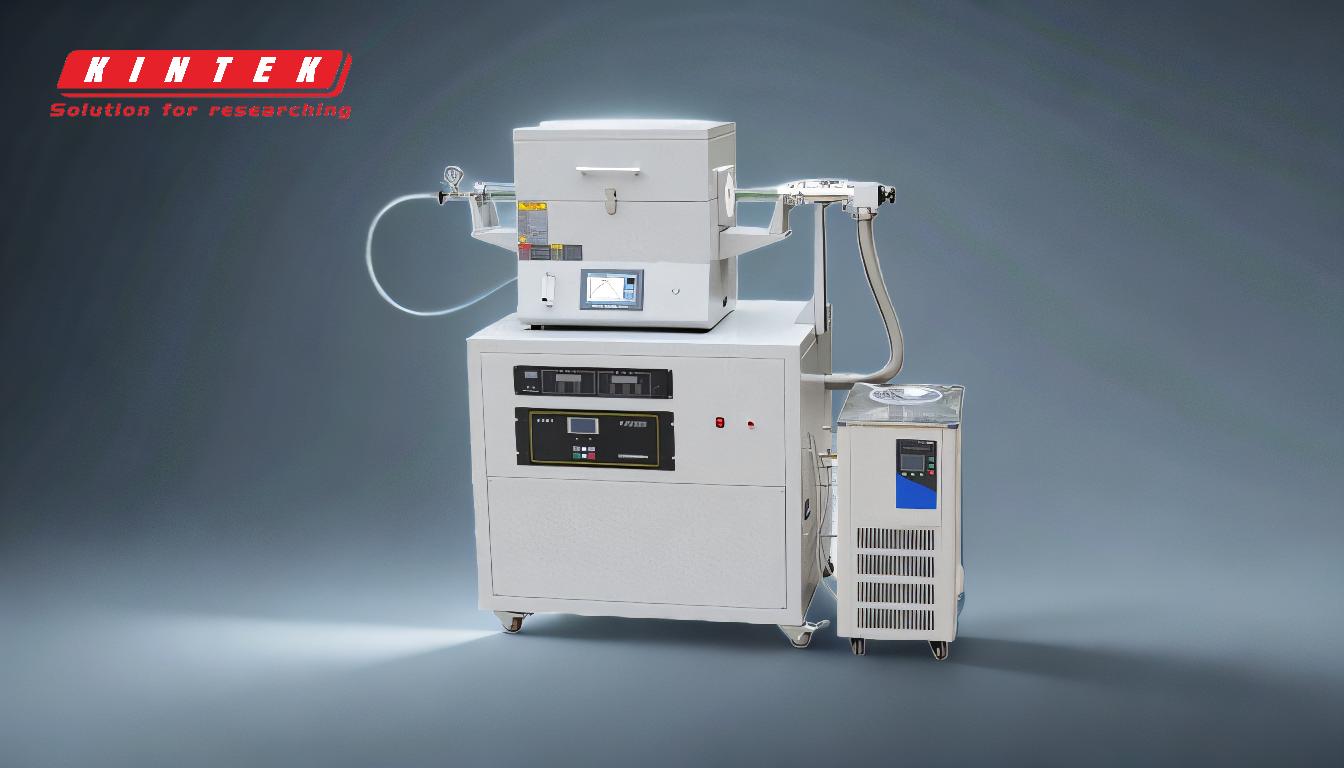
-
Definition of Vacuum Induction Melting (VIM):
- VIM is a metallurgical process where metals are melted under a vacuum using induction heating. The vacuum environment prevents contamination from atmospheric gases like oxygen and nitrogen, which can degrade the quality of the metal.
- This process is particularly useful for producing high-purity metals and alloys with precise chemical compositions.
-
How VIM Works:
- Induction Heating: An alternating current passes through a coil, generating a magnetic field that induces eddy currents in the metal, causing it to heat up and melt.
- Vacuum Environment: The melting occurs in a vacuum chamber, which removes impurities and gases from the molten metal, ensuring a clean and homogeneous melt.
- Pouring and Solidification: Once the metal is molten, it is poured into molds or further processed, depending on the desired final product.
-
Advantages of VIM:
- High Purity: The vacuum environment ensures minimal contamination, resulting in metals with superior purity.
- Precision Alloying: VIM allows for precise control over the chemical composition of the alloy, enabling the production of materials with specific properties.
- Improved Mechanical Properties: The absence of impurities and gases enhances the mechanical properties of the metal, such as strength, ductility, and fatigue resistance.
- Versatility: VIM can be used for a wide range of metals and alloys, including nickel, cobalt, titanium, and specialty steels.
-
Applications of VIM:
- Aerospace Industry: VIM is used to produce superalloys for jet engines and other critical aerospace components that require high strength and resistance to extreme temperatures.
- Medical Implants: The process is ideal for creating biocompatible alloys used in medical implants, such as titanium and cobalt-chromium alloys.
- Advanced Engineering: VIM is employed in the production of materials for high-performance applications, such as turbine blades, nuclear reactors, and precision instruments.
-
Comparison with Other Melting Techniques:
- VIM vs. Arc Melting: While arc melting is also used for high-purity metals, VIM offers better control over the melting process and is more suitable for complex alloys.
- VIM vs. Electroslag Remelting (ESR): ESR is often used as a secondary refining process after VIM to further improve the quality of the metal, but VIM is the primary method for achieving high purity and precise alloying.
-
Challenges and Limitations:
- Cost: VIM is an expensive process due to the need for specialized equipment and vacuum systems.
- Complexity: The process requires precise control and expertise, making it less accessible for small-scale operations.
- Material Limitations: While VIM is versatile, some materials may not be suitable for induction heating or may require additional processing steps.
-
Future Trends in VIM:
- Automation and Digitalization: Advances in automation and digital control systems are making VIM more efficient and accessible.
- Sustainability: Efforts are being made to reduce the environmental impact of VIM by optimizing energy use and recycling materials.
- New Alloys: Ongoing research is expanding the range of alloys that can be produced using VIM, opening up new possibilities in material science.
In conclusion, Vacuum Induction Melting (VIM) is a critical process in metallurgy, enabling the production of high-purity metals and alloys with exceptional properties. Its applications in aerospace, medical, and advanced engineering industries underscore its importance in modern manufacturing. Despite its challenges, VIM continues to evolve, driven by technological advancements and the demand for innovative materials.
Summary Table:
Aspect | Details |
---|---|
Definition | Melting metals under vacuum using induction heating for high purity. |
How It Works | Induction heating + vacuum environment = clean, homogeneous melt. |
Advantages | High purity, precise alloying, improved mechanical properties, versatility. |
Applications | Aerospace, medical implants, advanced engineering. |
Challenges | High cost, complexity, material limitations. |
Future Trends | Automation, sustainability, new alloy development. |
Interested in how VIM can elevate your material production? Contact our experts today to learn more!