VIM, or Vacuum Induction Melting, is a specialized process used in steelmaking and the production of high-performance alloys. It involves melting metals under a vacuum environment using induction heating. This method is particularly valued for its ability to produce high-purity metals with precise chemical compositions, making it essential for industries requiring materials with exceptional mechanical properties, such as aerospace, medical, and energy sectors. The vacuum environment prevents contamination from atmospheric gases, while the induction heating ensures uniform melting and precise temperature control. VIM is often followed by secondary refining processes like Vacuum Arc Remelting (VAR) to further enhance material quality.
Key Points Explained:
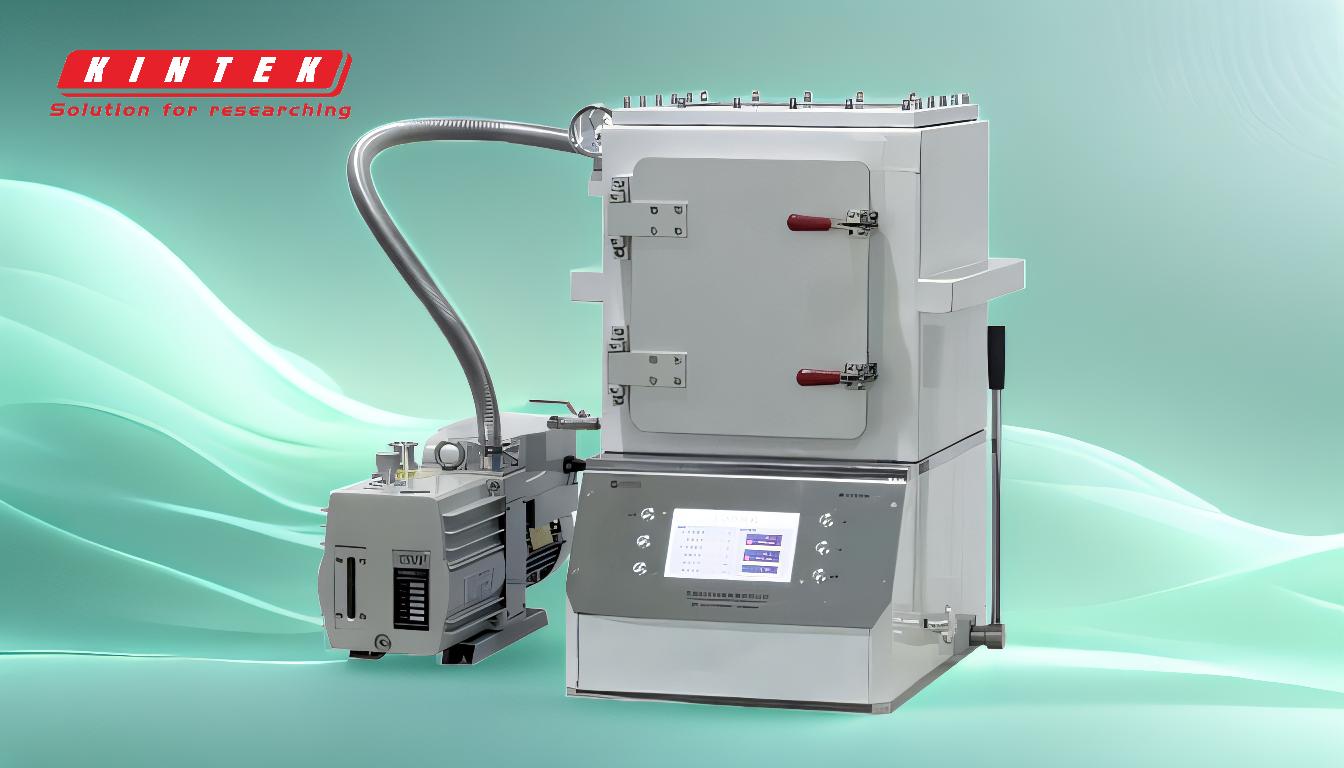
-
Definition and Purpose of VIM:
- VIM stands for Vacuum Induction Melting, a process used to melt and refine metals in a vacuum environment.
- The primary purpose of VIM is to produce high-purity metals and alloys with precise chemical compositions, free from contamination by atmospheric gases like oxygen and nitrogen.
- This process is critical for manufacturing materials used in demanding applications such as aerospace, medical implants, and power generation.
-
How VIM Works:
- The process begins by placing raw materials (e.g., scrap metal, virgin alloys) into a crucible inside a vacuum chamber.
- Induction heating is used to melt the materials. An alternating current passes through a coil, generating a magnetic field that induces eddy currents in the metal, causing it to heat up and melt.
- The vacuum environment ensures that no atmospheric gases can react with the molten metal, preventing the formation of oxides, nitrides, or other impurities.
-
Advantages of VIM:
- High Purity: The vacuum environment eliminates contamination, resulting in metals with superior purity.
- Precision Control: Induction heating allows for precise temperature control, ensuring uniform melting and consistent alloy composition.
- Versatility: VIM can be used for a wide range of metals and alloys, including nickel-based superalloys, titanium, and specialty steels.
- Improved Mechanical Properties: The absence of impurities enhances the mechanical properties of the final product, such as strength, fatigue resistance, and corrosion resistance.
-
Applications of VIM:
- Aerospace: VIM is used to produce components for jet engines, turbines, and other critical parts that require high strength and resistance to extreme temperatures.
- Medical: The process is employed to create biocompatible alloys for implants and surgical instruments.
- Energy: VIM-produced materials are used in nuclear reactors, gas turbines, and other high-performance energy systems.
- Electronics: High-purity metals from VIM are essential for semiconductor manufacturing and other advanced electronic applications.
-
Combination with Other Processes:
- VIM is often followed by secondary refining processes like Vacuum Arc Remelting (VAR) or Electro-Slag Remelting (ESR) to further improve the homogeneity and quality of the material.
- These additional steps help eliminate any remaining impurities and refine the microstructure, enhancing the material's performance in critical applications.
-
Challenges and Limitations:
- Cost: VIM is an expensive process due to the need for specialized equipment and the high energy consumption of induction heating.
- Complexity: The process requires precise control of temperature, vacuum levels, and alloy composition, making it technically challenging.
- Scale: VIM is typically used for smaller-scale production of high-value materials, as scaling up the process can be difficult and costly.
-
Future Trends:
- Advances in induction heating technology and vacuum systems are expected to make VIM more efficient and cost-effective.
- Increasing demand for high-performance materials in emerging industries, such as renewable energy and advanced electronics, is likely to drive further adoption of VIM.
- Research is ongoing to develop new alloys and optimize the VIM process for specific applications, ensuring its continued relevance in modern manufacturing.
In summary, VIM is a critical process in steelmaking and alloy production, offering unparalleled purity and precision. Its ability to produce high-performance materials makes it indispensable for industries that demand exceptional mechanical properties and reliability. While the process is complex and costly, its advantages far outweigh the challenges, ensuring its continued use in advanced manufacturing.
Summary Table:
Aspect | Details |
---|---|
Definition | Vacuum Induction Melting (VIM) melts metals in a vacuum using induction heating. |
Purpose | Produces high-purity metals with precise chemical compositions. |
Key Advantages | High purity, precise temperature control, versatility, improved mechanical properties. |
Applications | Aerospace, medical implants, energy systems, electronics. |
Challenges | High cost, technical complexity, limited scalability. |
Future Trends | Advances in efficiency, growing demand in renewable energy and electronics. |
Unlock the potential of high-purity metals for your industry—contact our experts today to learn more about VIM solutions!