Full annealing is a heat treatment process primarily applied to metals and alloys to enhance their ductility, reduce hardness, and improve machinability. This process involves heating the material to a specific temperature, holding it there for a sufficient period, and then allowing it to cool slowly. The goal is to reduce internal stresses, refine the grain structure, and improve the material's overall mechanical properties. Full annealing is commonly used for steels, but it is also beneficial for other metals such as copper, aluminium, and brass. The process can be carried out in various types of furnaces, including chamber furnaces, atmosphere furnaces, and vacuum furnaces, depending on the material and desired outcome.
Key Points Explained:
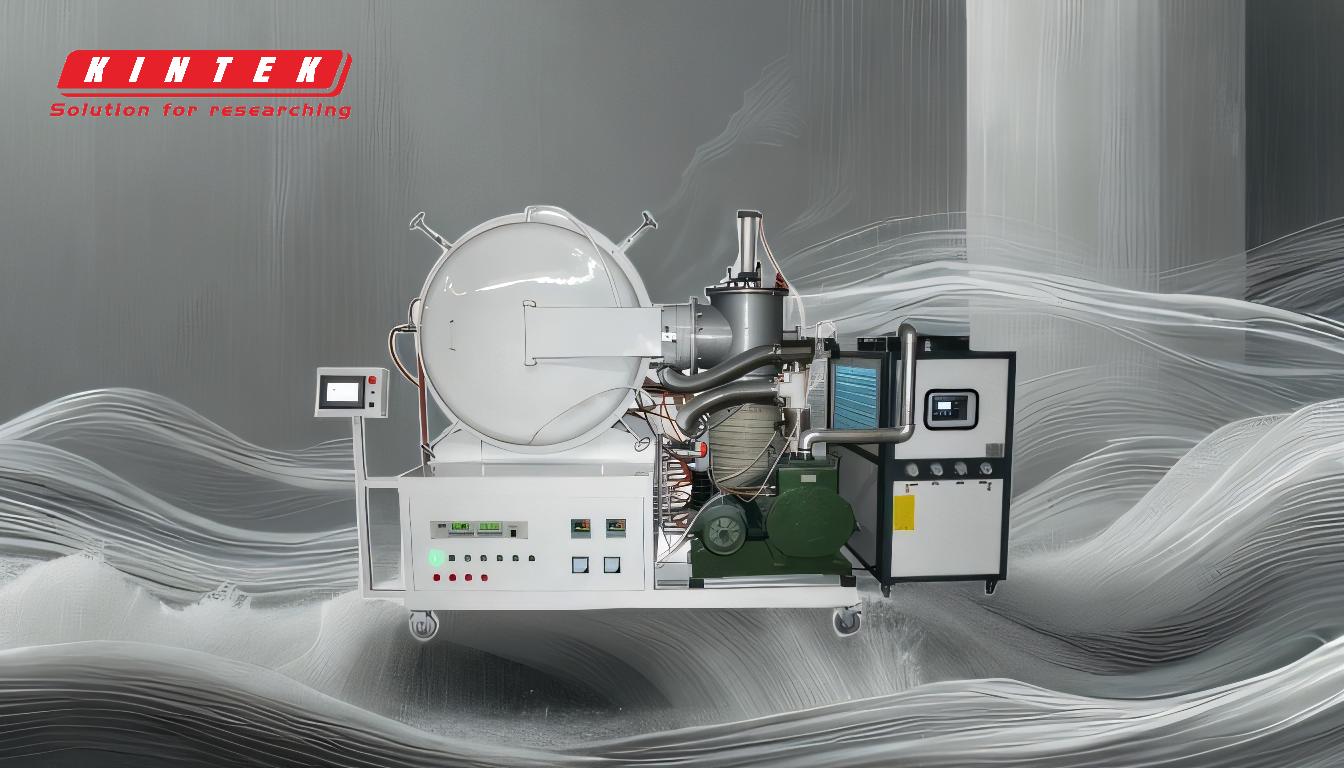
-
Purpose of Full Annealing:
- Full annealing is used to increase the ductility and reduce the hardness of materials. This is achieved by reducing dislocations in the crystal structure, which in turn improves the material's machinability and overall mechanical properties.
-
Materials Suitable for Full Annealing:
- Steels: Full annealing is most commonly applied to steels. It helps in refining the grain structure, reducing internal stresses, and improving ductility.
- Copper: Annealing copper can enhance its ductility, making it easier to work with in various applications.
- Aluminium: Annealing aluminium can improve its formability and reduce hardness, making it more suitable for shaping and forming processes.
- Brass: Annealing brass can increase its ductility and reduce internal stresses, which is particularly useful in manufacturing processes that require extensive shaping.
-
Equipment Used for Full Annealing:
- Chamber Furnaces: These are commonly used for annealing metals. They provide a controlled environment where the material can be heated uniformly to the desired temperature.
- Atmosphere Furnaces: These furnaces allow for annealing in a controlled atmosphere, which can be crucial for preventing oxidation or other chemical reactions that might affect the material's properties.
- Vacuum Furnaces: These are used for annealing in a vacuum environment, which is essential for materials that are sensitive to oxidation or contamination.
-
Process Details:
- Heating: The material is heated to a specific temperature, typically above its recrystallization temperature but below its melting point. The exact temperature depends on the material being annealed.
- Holding: The material is held at this temperature for a sufficient period to allow the dislocations in the crystal structure to rearrange, reducing internal stresses and refining the grain structure.
- Cooling: The material is then allowed to cool slowly, usually in the furnace itself, to prevent the formation of new stresses and to ensure the desired properties are achieved.
-
Benefits of Full Annealing:
- Improved Ductility: The material becomes more pliable and easier to shape or form.
- Reduced Hardness: The material becomes softer, which can be beneficial for machining or other manufacturing processes.
- Stress Relief: Internal stresses are reduced, which can prevent cracking or warping during subsequent processing or use.
- Grain Refinement: The grain structure is refined, leading to improved mechanical properties such as toughness and fatigue resistance.
In summary, full annealing is a versatile heat treatment process that can be applied to a variety of metals and alloys to improve their mechanical properties. The choice of equipment and specific process parameters will depend on the material being annealed and the desired outcome.
Summary Table:
Material | Benefits of Full Annealing |
---|---|
Steels | Refines grain structure, reduces internal stresses, improves ductility |
Copper | Enhances ductility, making it easier to work with |
Aluminium | Improves formability, reduces hardness |
Brass | Increases ductility, reduces internal stresses |
Learn more about how full annealing can benefit your materials—contact our experts today!