Pyrolysis is a thermal decomposition process that converts organic materials into valuable products like bio-oils, syngas, and biochar. The choice of reactor is critical as it determines the efficiency, yield, and quality of the end products. Various types of reactors are used, each suited for specific pyrolysis processes and feedstock types. The most common reactors include fluidized bed, fixed bed, rotary kiln, and drum reactors, each offering unique advantages in terms of heat transfer, scalability, and product yield. Below, we explore the key types of pyrolysis reactors, their mechanisms, and their applications.
Key Points Explained:
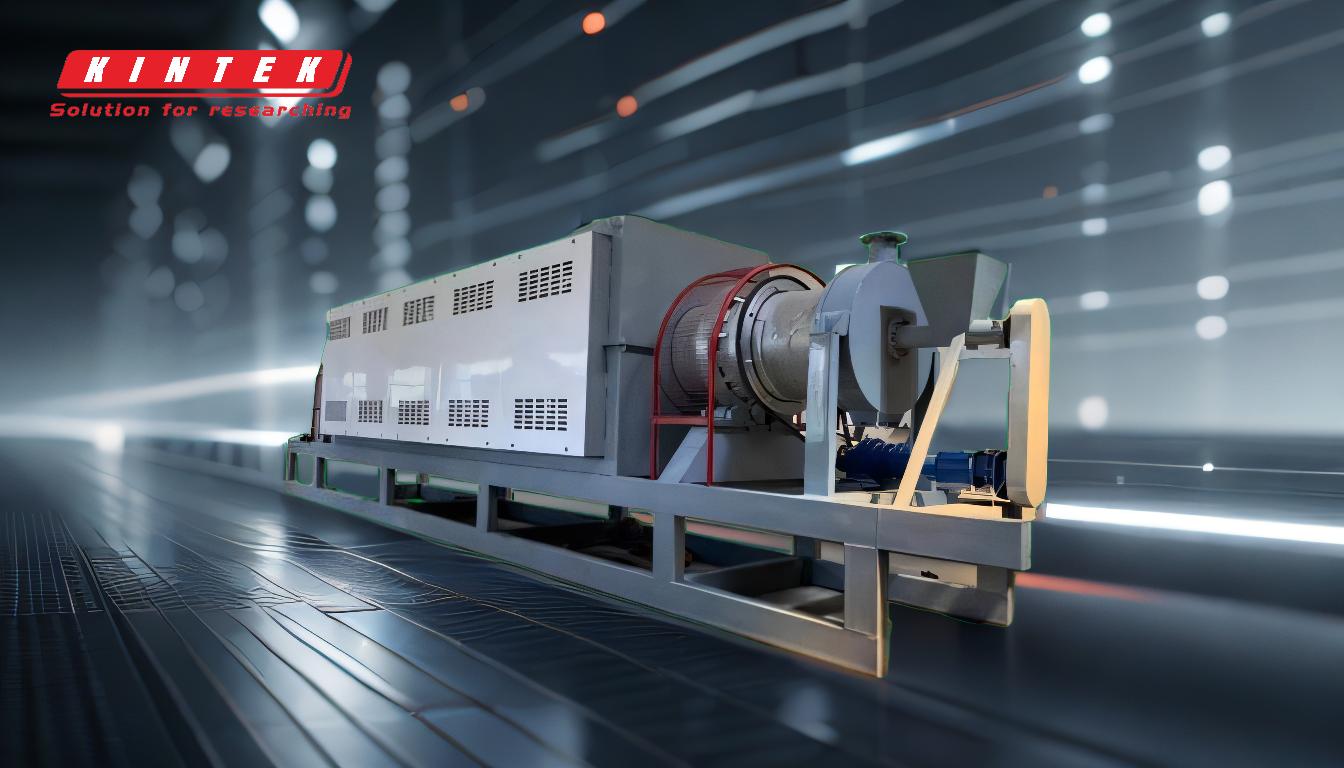
-
Types of Pyrolysis Reactors
-
Fluidized Bed Reactor:
- This reactor uses a bed material (e.g., sand) and a flowing fluid (often nitrogen) to create an inert atmosphere and ensure efficient heat transfer.
- It is ideal for fast pyrolysis due to its excellent heat transfer capabilities and uniform temperature distribution.
- The fluidized bed reactor is commonly used for producing bio-oils and syngas.
-
Fixed Bed Reactor:
- A simple and cost-effective design where the feedstock remains stationary while heat is applied.
- Suitable for slow pyrolysis, producing biochar and syngas.
- Limited scalability compared to other reactors.
-
Rotary Kiln Reactor:
- Operates in a horizontal 360-degree rotation mode, ensuring even heating of the feedstock.
- Suitable for semi-continuous and small-scale pyrolysis, improving oil yield and reducing processing time.
-
Drum Reactor (Rotating Drum Reactor):
- A drum-shaped vessel that rotates continuously, ensuring uniform heat distribution.
- Ideal for slow pyrolysis of biomass, yielding biochar and syngas.
- Commonly used in applications requiring moderate heat and long residence times.
-
Fluidized Bed Reactor:
-
Key Features of Pyrolysis Reactors
-
Heat Transfer Efficiency:
- Fluidized bed reactors excel in heat transfer due to the fluidized particles, while rotary kilns ensure even heating through rotation.
-
Scalability:
- Fluidized bed and rotary kiln reactors are more scalable compared to fixed bed reactors, making them suitable for industrial applications.
-
Product Yield and Quality:
- The design and operation of the reactor directly influence the yield and quality of products like bio-oil, biochar, and syngas.
-
Heat Transfer Efficiency:
-
Applications of Pyrolysis Reactors
-
Bio-Oil Production:
- Fluidized bed and rotary kiln reactors are commonly used for producing bio-oils due to their high efficiency and scalability.
-
Biochar Production:
- Fixed bed and drum reactors are preferred for biochar production, especially in slow pyrolysis processes.
-
Syngas Generation:
- Fluidized bed and drum reactors are effective for generating syngas, which can be used for heat and electricity production.
-
Bio-Oil Production:
-
Factors Influencing Reactor Choice
-
Feedstock Type:
- The nature of the feedstock (e.g., biomass, plastic, rubber) determines the most suitable reactor type.
-
Process Requirements:
- Fast pyrolysis requires reactors with high heat transfer rates, while slow pyrolysis can use simpler designs like fixed bed reactors.
-
End Product Goals:
- The desired end products (bio-oil, biochar, or syngas) influence the choice of reactor and operational parameters.
-
Feedstock Type:
-
Advantages of Modern Pyrolysis Reactors
-
Energy Efficiency:
- Modern reactors are designed to maximize energy efficiency, reducing operational costs.
-
Environmental Benefits:
- Pyrolysis reactors help convert waste materials into valuable products, reducing landfill use and greenhouse gas emissions.
-
Versatility:
- Reactors like the pyrolysis reactor can handle a wide range of feedstocks, making them versatile for various industries.
-
Energy Efficiency:
By understanding the different types of reactors and their applications, purchasers can make informed decisions based on their specific needs, whether for small-scale biochar production or large-scale bio-oil generation.
Summary Table:
Reactor Type | Key Features | Applications |
---|---|---|
Fluidized Bed | Excellent heat transfer, uniform temperature, scalable | Bio-oil and syngas production |
Fixed Bed | Simple design, cost-effective, limited scalability | Biochar and syngas production |
Rotary Kiln | Even heating, semi-continuous operation, improved oil yield | Bio-oil production |
Drum Reactor | Uniform heat distribution, moderate heat, long residence times | Biochar and syngas production |
Ready to choose the right pyrolysis reactor for your needs? Contact our experts today for personalized guidance!