Heat treatment baskets are essential tools used in various industrial processes, particularly in heat treatment applications. These baskets are designed to withstand high temperatures and harsh environments while holding and transporting parts during processes like annealing, hardening, and tempering. The materials used for heat treatment baskets are carefully selected to ensure durability, resistance to thermal stress, and compatibility with the specific heat treatment process. Common materials include high-temperature alloys, stainless steel, and specialized coatings or treatments to enhance performance. The choice of material depends on factors such as the temperature range, chemical environment, and the type of parts being treated.
Key Points Explained:
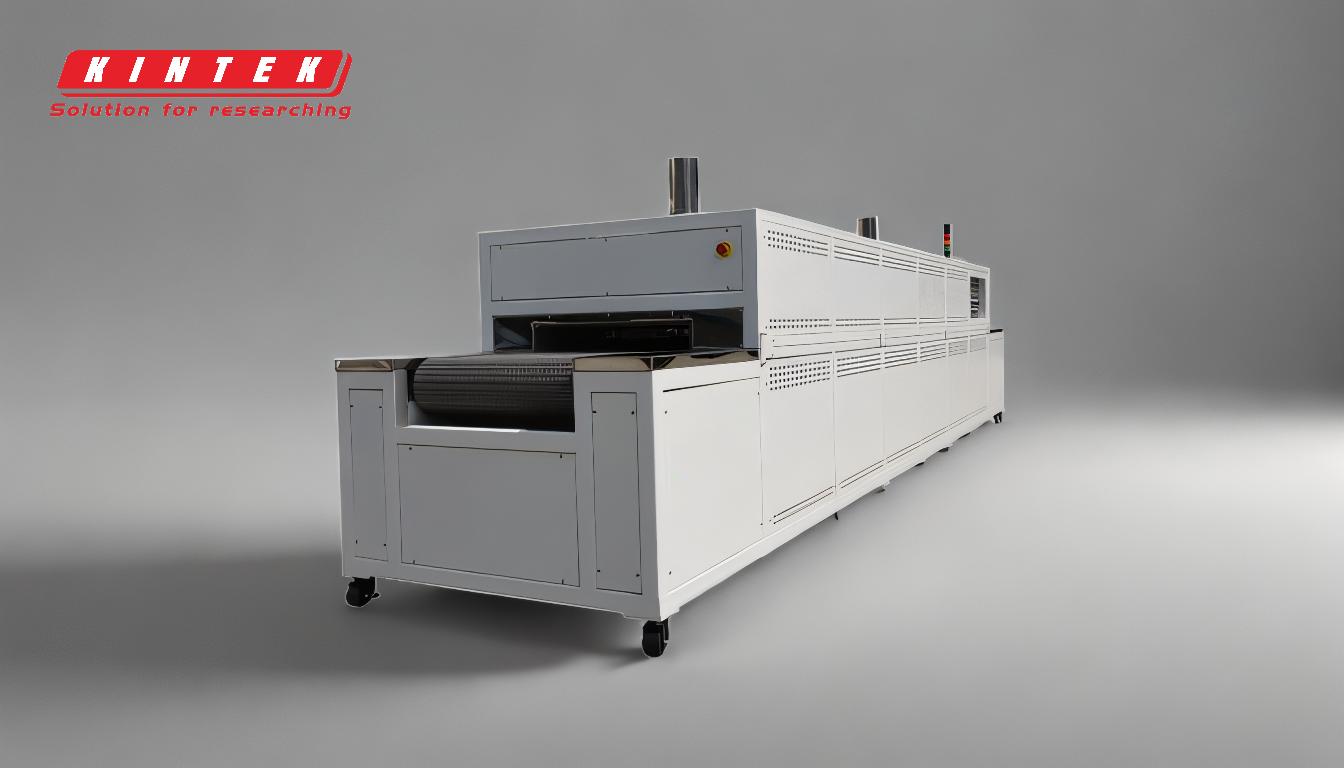
-
Purpose of Heat Treatment Baskets:
- Heat treatment baskets are used to hold and transport parts during high-temperature processes such as annealing, hardening, and tempering.
- They must withstand extreme temperatures, thermal cycling, and exposure to chemicals or gases used in the heat treatment process.
-
Common Materials Used:
- High-Temperature Alloys: Materials like Inconel, Hastelloy, and other nickel-based alloys are commonly used due to their excellent resistance to oxidation and high-temperature strength.
- Stainless Steel: Grades such as 304 and 316 stainless steel are popular for their corrosion resistance and ability to withstand moderate temperatures.
- Specialized Coatings: Some baskets are coated with materials like ceramic or other high-temperature-resistant coatings to enhance durability and performance.
-
Material Selection Criteria:
- Temperature Range: The material must be able to withstand the specific temperature range of the heat treatment process without degrading.
- Chemical Resistance: The material should resist corrosion or chemical reactions with the gases or chemicals used in the process.
- Mechanical Strength: The basket must maintain structural integrity under the weight of the parts and the stress of thermal cycling.
- Cost and Availability: The material should be cost-effective and readily available for manufacturing.
-
Applications and Customization:
- Heat treatment baskets are customized based on the specific requirements of the application, such as the size and shape of the parts being treated.
- They are used in industries like aerospace, automotive, and manufacturing, where precise heat treatment is critical for part performance.
-
Maintenance and Longevity:
- Proper maintenance, such as regular cleaning and inspection, can extend the lifespan of heat treatment baskets.
- The choice of material plays a significant role in determining the basket's longevity and performance over time.
In summary, heat treatment baskets are made from materials that can endure extreme conditions, ensuring they perform reliably in demanding industrial environments. The selection of the right material is crucial for achieving optimal results in heat treatment processes.
Summary Table:
Material Type | Key Properties | Common Uses |
---|---|---|
High-Temperature Alloys | Excellent oxidation resistance, high-temperature strength (e.g., Inconel, Hastelloy) | Aerospace, automotive, and high-temperature industrial applications |
Stainless Steel | Corrosion resistance, moderate temperature tolerance (e.g., 304, 316 stainless steel) | General-purpose heat treatment processes |
Specialized Coatings | Enhanced durability, high-temperature resistance (e.g., ceramic coatings) | Applications requiring extended lifespan and performance in harsh environments |
Need help selecting the right heat treatment basket material? Contact our experts today for personalized advice!