Porcelain furnaces are critical in dental laboratories for firing porcelain materials to create dental restorations. Calibration ensures the furnace operates at precise temperatures, which is essential for consistent results. The calibration process typically involves using specific materials or tools designed to measure and verify the furnace's temperature accuracy. These materials must withstand high temperatures and provide reliable readings to ensure the furnace's performance aligns with the required standards.
Key Points Explained:
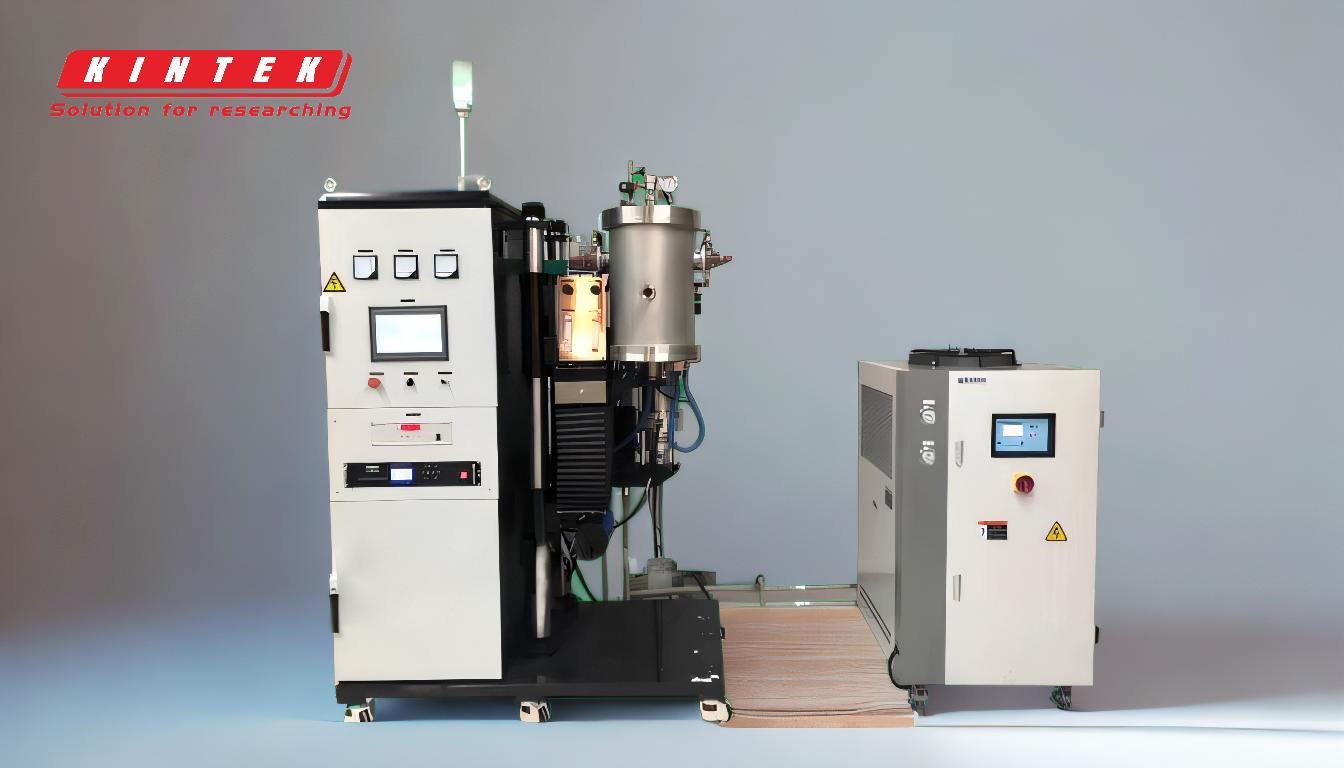
-
Purpose of Calibration:
- Calibration is essential to ensure the porcelain furnace operates at the correct temperature, which directly impacts the quality of dental restorations. Inaccurate temperatures can lead to under-fired or over-fired porcelain, resulting in poor aesthetics, compromised strength, or even failure of the restoration.
-
Common Calibration Materials:
- Pyrometric Cones: These are ceramic materials that bend at specific temperatures. They are placed inside the furnace during a firing cycle, and their bending point is observed to verify the furnace's temperature accuracy.
- Thermocouples: These are temperature sensors that measure the furnace's internal temperature. They provide real-time data and are often used in conjunction with calibration software to ensure precise temperature control.
- Test Rings: These are small, pre-fired ceramic rings used to evaluate the furnace's performance. They are fired under controlled conditions, and their shrinkage or expansion is measured to assess the furnace's accuracy.
-
Importance of High-Temperature Resistance:
- Calibration materials must withstand the extreme temperatures of a porcelain furnace, which can exceed 1,000°C. Materials like pyrometric cones and thermocouples are specifically designed to endure these conditions without degrading, ensuring reliable calibration results.
-
Frequency of Calibration:
- Regular calibration is recommended to maintain the furnace's accuracy. Factors such as frequent use, power fluctuations, or mechanical wear can affect the furnace's performance over time. Calibration should be performed according to the manufacturer's guidelines or whenever inconsistencies in firing results are observed.
-
Manufacturer-Specific Calibration Tools:
- Some porcelain furnace manufacturers provide proprietary calibration tools or kits designed specifically for their equipment. These tools ensure compatibility and accuracy, making them the preferred choice for calibration.
-
Professional Calibration Services:
- For laboratories lacking the expertise or equipment to perform calibration in-house, professional calibration services are available. These services use advanced tools and techniques to ensure the furnace operates within the required specifications.
By using the appropriate materials and following a systematic calibration process, dental laboratories can ensure their porcelain furnaces deliver consistent, high-quality results for dental restorations.
Summary Table:
Calibration Material | Purpose | Key Features |
---|---|---|
Pyrometric Cones | Verify temperature accuracy by bending at specific temperatures | High-temperature resistance, reliable for manual calibration |
Thermocouples | Measure internal temperature in real-time | Compatible with calibration software, precise temperature monitoring |
Test Rings | Evaluate furnace performance through shrinkage or expansion measurements | Pre-fired ceramic, assesses accuracy under controlled conditions |
Ensure your porcelain furnace delivers consistent results—contact our experts today for calibration guidance!