Direct Energy Deposition (DED) is a versatile additive manufacturing process that involves the use of focused thermal energy, such as a laser or electron beam, to fuse materials by melting as they are deposited. The materials used in DED are typically in the form of powders or wire, and they are chosen based on the desired properties of the final product. Common materials used in DED include metals, alloys, and composites, which are selected for their mechanical, thermal, and electrical properties. The process is widely used in industries such as aerospace, automotive, and medical devices, where high-performance materials are required.
Key Points Explained:
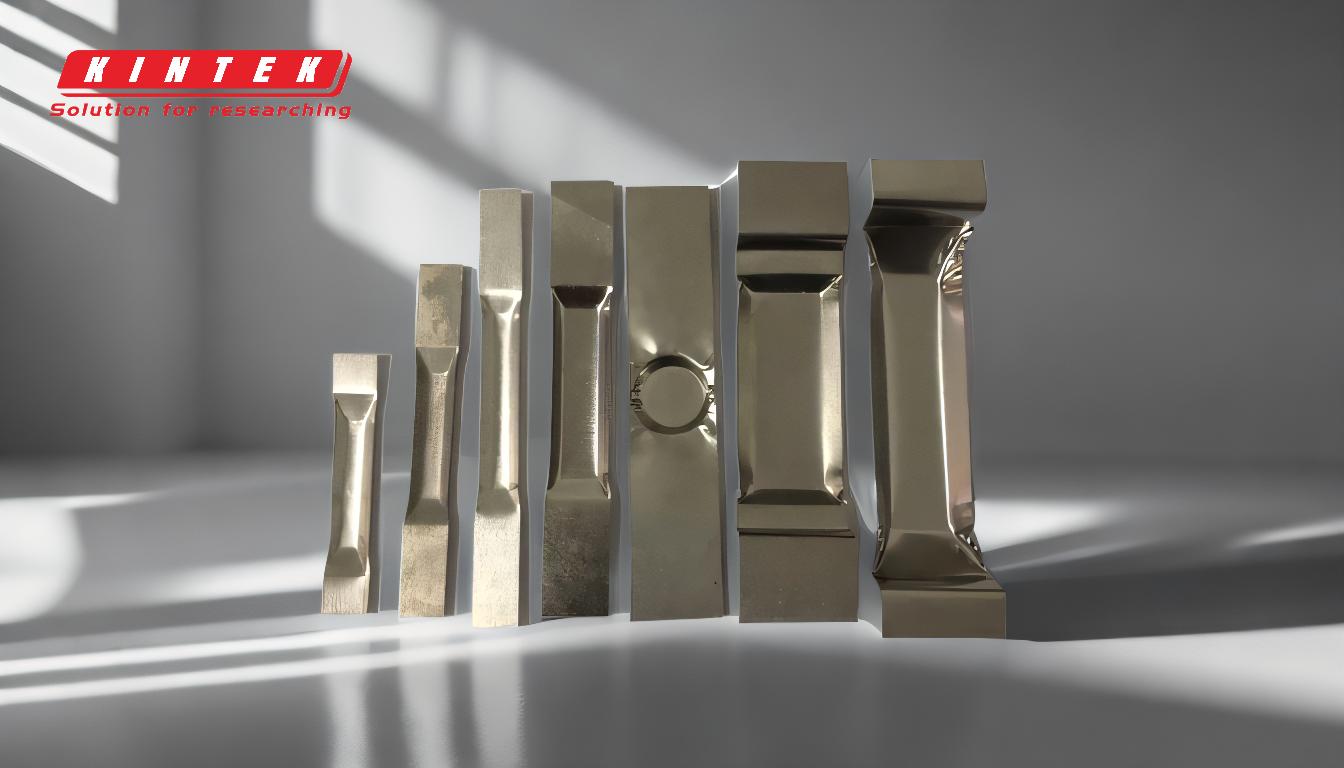
-
Materials Used in Direct Energy Deposition (DED):
- Metals and Alloys: DED commonly uses metals such as titanium, aluminum, nickel, and steel, as well as their alloys. These materials are chosen for their strength, durability, and resistance to corrosion, making them ideal for high-stress applications.
- Composites: Composites, which are materials made from two or more constituent materials with different physical or chemical properties, are also used in DED. These materials can be engineered to have specific properties, such as enhanced strength-to-weight ratios or improved thermal conductivity.
- Ceramics: Although less common, ceramics can also be used in DED. These materials are typically used in applications requiring high thermal and chemical resistance.
-
Form of Materials in DED:
- Powder: The most common form of material used in DED is powder. The powder is fed into the deposition area, where it is melted by the energy source and then solidified to form the final product.
- Wire: In some cases, wire is used instead of powder. The wire is fed into the deposition area, where it is melted and then deposited layer by layer to build the final product.
-
Applications of DED Materials:
- Aerospace: In the aerospace industry, DED is used to fabricate complex components such as turbine blades, engine parts, and structural components. Materials like titanium and nickel-based superalloys are commonly used due to their high strength and resistance to extreme temperatures.
- Automotive: In the automotive industry, DED is used to produce lightweight components that improve fuel efficiency and performance. Aluminum and steel alloys are frequently used in this sector.
- Medical Devices: DED is also used in the medical field to create customized implants and prosthetics. Materials like titanium and cobalt-chromium alloys are preferred for their biocompatibility and strength.
-
Advantages of Using DED Materials:
- Customization: DED allows for the creation of highly customized parts with complex geometries that would be difficult or impossible to achieve with traditional manufacturing methods.
- Material Efficiency: The process is highly efficient in terms of material usage, as it only deposits material where it is needed, reducing waste.
- Rapid Prototyping: DED is ideal for rapid prototyping, as it allows for quick iteration and testing of new designs.
-
Challenges and Considerations:
- Material Properties: The properties of the materials used in DED must be carefully considered, as they can affect the final product's performance. Factors such as melting point, thermal conductivity, and mechanical strength are critical.
- Process Control: Achieving consistent results with DED requires precise control over the deposition process, including the energy source, material feed rate, and cooling rate.
In summary, Direct Energy Deposition (DED) is a powerful additive manufacturing technique that uses a variety of materials, including metals, alloys, composites, and ceramics, in the form of powder or wire. These materials are selected based on the specific requirements of the application, such as strength, durability, and resistance to extreme conditions. DED is widely used in industries like aerospace, automotive, and medical devices, offering advantages such as customization, material efficiency, and rapid prototyping. However, careful consideration of material properties and process control is essential to achieve the desired results.
Summary Table:
Material Type | Examples | Key Properties | Common Applications |
---|---|---|---|
Metals & Alloys | Titanium, Aluminum | Strength, Durability, Corrosion Resistance | Aerospace, Automotive |
Composites | Carbon Fiber Composites | Enhanced Strength-to-Weight Ratio | Aerospace, Automotive |
Ceramics | Zirconia, Alumina | High Thermal & Chemical Resistance | Medical Devices, High-Tech |
Powder/Wire Form | Powder, Wire | Material Efficiency, Customization | Rapid Prototyping, Complex Parts |
Ready to leverage DED for your next project? Contact our experts today for tailored solutions!