Hot isostatic pressing (HIP) is a versatile manufacturing process used to densify and improve the properties of a wide range of materials. It is particularly effective for materials that require high density, uniformity, and enhanced mechanical properties. HIP is commonly applied to metals, ceramics, composites, and polymers, as well as specialized materials like cemented carbides, rare earth magnets, and carbon-based materials. The process is also used in the production of advanced components for industries such as aerospace, energy, and electronics, where high-performance materials are critical. By eliminating internal defects and achieving near-full density, HIP ensures superior material performance and reliability.
Key Points Explained:
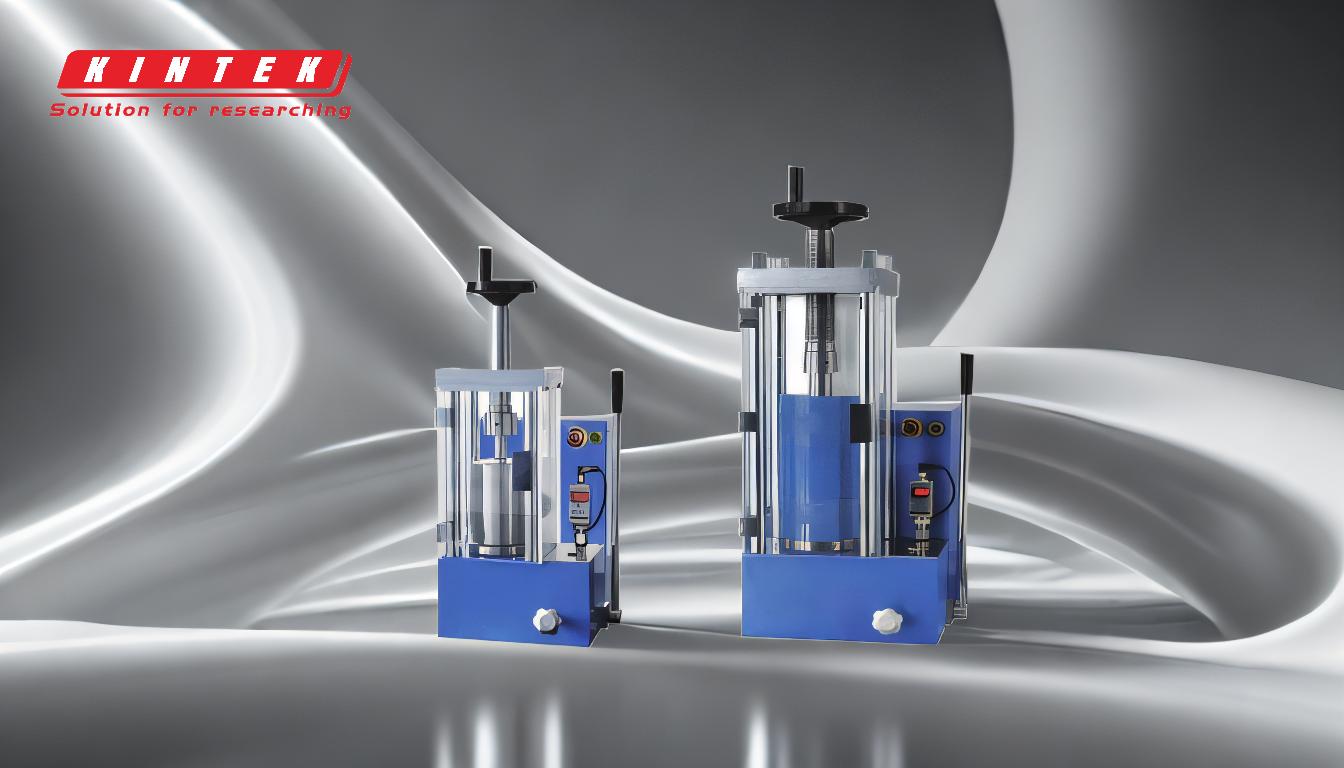
-
Materials Commonly Processed by HIP:
- Metals: HIP is widely used for metals such as titanium, aluminum, and high-temperature alloys. These materials benefit from the elimination of internal porosity and defects, leading to improved mechanical properties and performance in demanding applications.
- Ceramics: Ceramic materials, including advanced ceramics and solid electrolytes, are densified using HIP to achieve high strength, wear resistance, and thermal stability.
- Composites: HIP is used to process composite materials, ensuring uniform density and bonding between different material phases, which is critical for structural integrity.
- Polymers: Certain high-performance polymers are processed using HIP to enhance their density and mechanical properties.
- Specialized Materials: HIP is employed for materials like cemented carbides, lanthanide permanent magnets, and carbon-based materials, which require high density and uniformity for optimal performance.
-
Applications in Advanced Manufacturing:
- Aerospace: HIP is used to produce critical components such as turbine blades, engine parts, and structural components from high-temperature alloys and titanium, ensuring they can withstand extreme conditions.
- Energy: In the energy sector, HIP is used to manufacture components for nuclear reactors, fuel cells, and batteries, where material integrity and performance are paramount.
- Electronics: HIP is applied in the production of advanced ceramics and composites used in electronic devices, ensuring reliability and durability.
-
Benefits of HIP:
- Increased Density: HIP achieves densities greater than 98% of full density, often reaching full density with proper processing conditions.
- Improved Mechanical Properties: The process enhances strength, ductility, toughness, and fatigue resistance, making materials more suitable for high-stress applications.
- Defect Elimination: HIP removes internal porosity and defects, resulting in materials with uniform properties and longer service life.
- Design Flexibility: HIP allows for the creation of complex shapes and lightweight designs without compromising performance.
- Material Bonding: The process enables the formation of metallurgical bonds between different materials, facilitating the production of hybrid components.
-
Process Mechanisms:
- HIP relies on mechanisms such as sintering, creep, and bulk deformation to achieve densification. Creep plays a significant role in the process, especially at high temperatures and pressures.
- The process involves sealing powder or pre-formed components in a flexible mold and subjecting them to uniform hydrostatic pressure using either the wet-bag or dry-bag technique.
-
Industries and Use Cases:
- HIP is essential in industries requiring high-performance materials, such as aerospace, automotive, medical, and energy. It is also used in the production of cutting tools, wear-resistant components, and advanced electronic materials.
By leveraging HIP technology, manufacturers can produce materials and components with exceptional properties, ensuring they meet the rigorous demands of modern applications.
Summary Table:
Material Type | Examples | Key Benefits |
---|---|---|
Metals | Titanium, aluminum, high-temperature alloys | Eliminates porosity, enhances mechanical properties, improves performance |
Ceramics | Advanced ceramics, solid electrolytes | Achieves high strength, wear resistance, and thermal stability |
Composites | Composite materials | Ensures uniform density and bonding for structural integrity |
Polymers | High-performance polymers | Enhances density and mechanical properties |
Specialized Materials | Cemented carbides, rare earth magnets, carbon-based materials | Provides high density and uniformity for optimal performance |
Unlock the potential of HIP for your materials—contact our experts today to learn more!